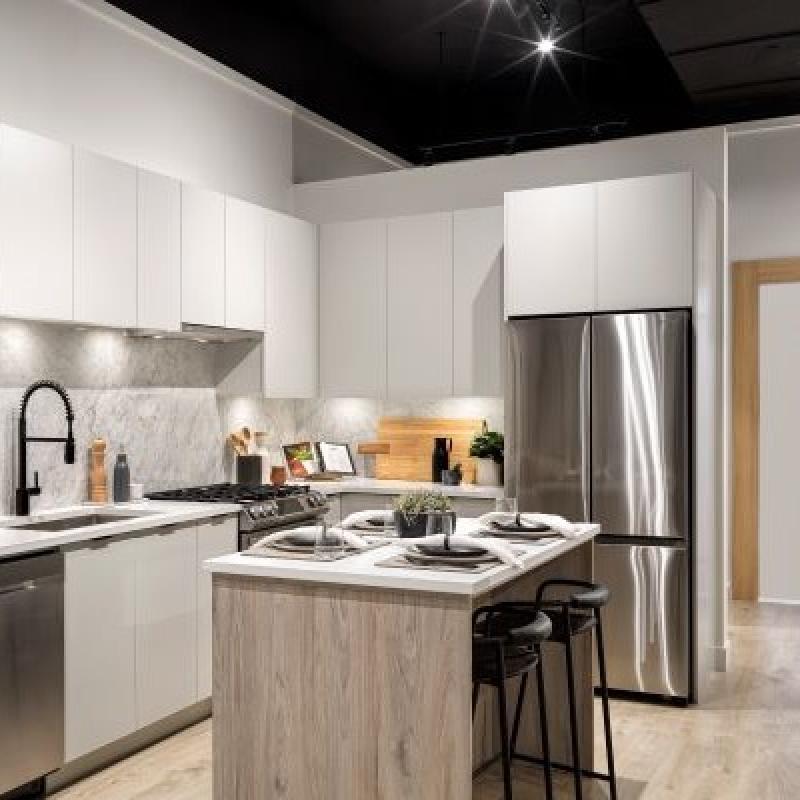
The term “mass timber” might conjure up straight-grained lumber milled from gigantic old-growth Douglas fir and Western red cedars forests — the backbone of B.C.’s housing and forestry industry until quite recently. In fact, the opposite is true.
Today's mass timber is often sourced from sustainably-certified tree farms utilizing second- and third-growth trees that are cut and glued into a variety of configurations.
Mass timber is often used in a hybrid form with existing concrete and stick-frame construction and is primarily found in LEED-certified schools, libraries or office buildings. In addition to offering structural load bearing, exposed glue-lam beams and latticework provide striking visual interest when used in lobbies, atriums and rooflines.
One prominent Vancouver-area developer is making a big bet on the future of mass timber to build many of its new homes around the Lower Mainland. During the past 50 years, Adera Development has constructed over 11,000 homes — mostly mid-level condos and townhomes using either conventional concrete or wood-frame construction.
Adera welcomes U.S. mass-timber advocates
Last week, Adera chief operating officer Rocky Sethi conducted a tour for visiting American mass timber advocates to highlight two projects in the Vancouver suburb of Coquitlam that utilize Adera’s trademarked SmartWood technology.
One of these projects, a 59-unit purpose-built rental building called RED Como Lake, is nearing completion.
The building block, literally, of Adera’s SmartWood construction is its use of cross-laminated timber (CLT), a multi-layer mass timber product that matches the strength and durability of concrete and steel at a fraction of the weight.
The knock against inexpensively constructed rental units from the stick frame 2x4s are many: poor soundproofing, susceptibility to damage from fire and floods, and a building life-cycle that is seldom longer than 60 years.
“CLT opens the door to a new, ecological way to construct mass-timber buildings," Sethi said. "This new class of building material is as strong as concrete and steel but comes in at a price point that falls between light-wood frame and concrete.”
Adrea, Kalesnikoff partnership
To develop its SmartWood product, Adera partnered with Kalesnikoff, a highly-regarded sustainable forestry company started almost a century ago which owns tree farms in B.C.’s West Kootenay. The features, advantages and benefits are numerous and diverse.
The Journal of Sustainable Forestry estimates substituting wood for current construction materials would save 14 to 31 per cent of global carbon dioxide emissions annually.
Sethi pointed out SmartWood’s air components sequester carbon, thus reducing each home’s carbon footprint.
According to a recent Vancouver Sun article, 307 mass-timber wood buildings have been built in B.C. — which is almost as many as the 356 buildings that currently exist in the entire United States. The same article also states the carbon-sequestering properties of wood can confer a huge environmental benefit.
This type of technology is already being used in some of downtown Vancouver’s most premium office spaces such as TELUS Garden.
“If you look at many of the new premium office projects that are commanding attention — to say nothing of top dollar — you’ll see that the ones that command the highest lease rates also tend to focus on occupant wellness," Sethi said. "Mass timber office buildings offer the unique characteristic of the natural wood, which is biophilic; in other words, that help human beings to connect with nature."
The attractions of mass timber
Think of engineered hardwood floors, richly laminated exposed beams with skylights and atriums that flood the interiors with natural light.
“You’ll see quite a few tradesmen who are contracted to visiting our sites and they inform us how much they appreciate working at a jobsite where the building is quieter and feels more solid than using traditional materials and methods. Our new communities (SÕL in Coquitlam, and Pura in Surrey) are targeted at people who want a high degree of energy efficiency and environmental sustainability.”
With a total weight by volume that’s only 20 per cent of conventional concrete buildings, SmartWood homes have a shorter completion timeline, since many of the components are pre-fabricated and shipped to the jobsite. Additional time is saved by forgoing the concrete curing process.
Lighter mass also means the building doesn’t settle into place in the way concrete structures do. Building settlement is minimal compared to buildings with a concrete floorplate.
Breaking a sound barrier
There’s more to mass timber than pretty layers of gorgeously laminated cedar and fir. To truly be successful in a highly-competitive marketplace, Adera needed to solve an issue that has plagued multi-storey projects since pretty much cave-man days — namely, sound transmission between shared walls and floors.
At SoL’s presentation house, Adera has constructed two rooms to show the significant difference in not only the noise level but the timbre when it comes to reducing, if not eliminating, sound leakage.
Sethi also points out how CLT offers proven superiority over stick frame construction when it comes to fire resistance. “We’ve demonstrated the fire plans for our buildings to municipal officials and frankly, they’ve been blown away by how well our buildings perform.”
One major knock against B.C.’s forest industry has always been that a vast percentage of logs cut in the province end up being exported in raw form to Asian and American markets, where they are milled by local companies.
Mass timber adoption is being encouraged by the provincial New Democratic Party-led government to develop more value-added jobs in manufacturing and drive world-class innovation through assisting in research and development.
“Mass timber is still in its infancy," Sethi said. "BCIT (British Columbia Institute of Technology) has just announced a new program that will fast-track education for existing trades workers to familiarize them on how to work with mass timber.”
Adera’s SmartWood brand has already achieved first-mover status, offering a catchy way to engage and educate potential homebuyers and sell them on a proven, branded technology.
EDITOR'S NOTE: This article was updated after publishing to incorporate additional quotes and information from Adera.