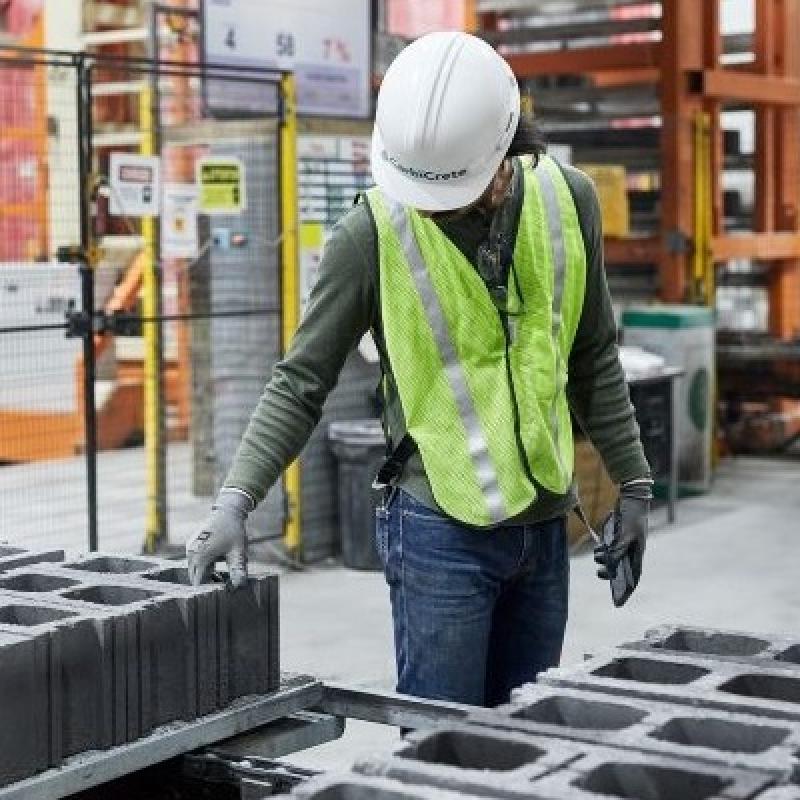
Lafarge Canada Inc. has been selected by climate tech company CarbiCrete to supply a key material needed for making carbon-negative concrete to CarbiCrete's clients.
At its St. Constant facilities near Montreal, cement and concrete manufacturer Lafarge will be grinding and delivering steel slag, a byproduct of steel production. The grinded steel slag is used in CarbiCrete’s concrete-making process as a cement replacement.
Cement production is one of the largest polluting sectors in the world, responsible for approximately eight per cent of global greenhouse gas emissions.
Headquartered in Montreal, CarbiCrete has developed a method of making carbon-negative concrete, which it licenses to concrete manufacturers. The abated carbon dioxide emissions are also sold as carbon credits.
The partnership gives Lafarge’s clients a “huge level of comfort in terms of supply of the product, because it’s a multinational rather than buying slag grinded from someone else,” Chris Stern, the CEO and co-founder of CarbiCrete, told Sustainable Biz Canada.
Turning waste into a concrete ingredient
Lafarge is an ideal partner for CarbiCrete, Stern said, because it has many customers in Canada and the logistics and sales teams to deliver materials.
The two companies were in conversation for a few years, Stern said, and discussed how to best work together.
Lafarge’s customers will have “a well-known company to supply them the product they need to do the CarbiCrete process,” Stern said, and noted Lafarge has extensive experience grinding metal slags.
The grinded steel slag has typically ended up as a waste product in landfills.
When mixed in during CarbiCrete’s concrete-making process, the steel slag powder cures the concrete and permanently sequesters carbon dioxide, trapping the greenhouse gas within the construction material.
The company’s technology can eliminate cement use in concrete and captures 500 grams of carbon dioxide in an 18-kilogram block of concrete, Stern said. The company also claims the concrete cuts material costs by 10 to 20 per cent, and has 30 per cent more compressive strength than a traditional concrete block.
CarbiCrete’s technology is used by Patio Drummond at its precast facility in Drummondville, Que. where it produces hundreds of concrete bricks per day.
Lafarge’s decarbonization efforts
Lafarge has embarked on several partnerships and initiatives to decarbonize its cement and concrete operations.
At its Richmond, B.C. cement factory in July, Lafarge converted all production to ECOPlanet low-carbon cement, which offers a 35 per cent reduction in carbon emissions compared to typical Portland cement.
Lafarge’s foray into carbon capture extended to a partnership with Svante and Dimensional Energy, where Dimensional’s carbon dioxide utilization technology will be used in Lafarge’s cement manufacturing facility in Richmond.
It began piloting its ECOCycle project in St. Constant, integrating demolition waste into cement production to reduce construction waste and carbon emissions.
In March, Lafarge signed a memorandum of understanding with Progressive Planet Solutions Inc. to purchase all the carbon-capturing cement additive produced by Progressive Planet's pilot manufacturing facility.
CarbiCrete’s next steps
As for CarbiCrete, Stern said his company is planning to raise more funding in 2024 and has a partnership with French construction materials company Saint-Gobain. CarbiCrete’s process is being certified for use in France, where Saint-Gobain’s has 17 facilities.
There are also projects in France, Ireland, India, Canada and the U.S. to look out for, Stern added.