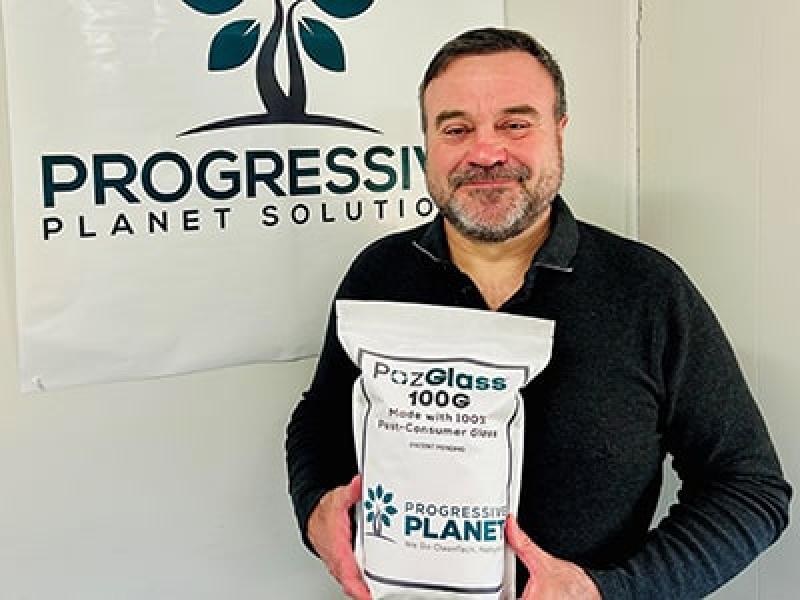
Progressive Planet Solutions Inc. and Lafarge Canada Inc. have signed a non-binding memorandum of understanding (MOU) for Lafarge to purchase all the carbon-capturing cement additive produced by Progressive Planet's pilot manufacturing facility currently under construction.
Earlier this month, Vancouver-based Progressive Planet (PLAN-X) announced it is constructing a pilot plant to produce 12 tonnes of PozGlass 100G per day and sequester emissions generated at its Kamloops operations. It will be operational in 2024.
Ground-glass pozzolan, or post-consumer glass, is typically used to replace up to 30 per cent of Portland cement in concrete. PozGlass 100G, made of 100 per cent recycled consumer glass, permanently sequesters carbon dioxide (CO2) in post-consumer glass while also reducing sodium.
PozGlass 100G improves the properties of ground-glass pozzolan, with the result being a low carbon footprint, better strength and more resistance to alkali-silica reactivity.
Steve Harpur, Progressive Planet’s CEO, said the MOU is designed to work toward a final agreement where Lafarge offtakes all the PozGlass 100G from Progressive Planet’s pilot plant - up to 3,200 tonnes per year. Lafarge will then test PozGlass 100G, use it in its operations and develop markets for it.
“We are not a cement company that has the distribution, the marketing (or) the infrastructure. In my mind (it’s) a very strong win-win, where we develop the technology and produce the product and they purchase it from us. They've also agreed to provide technical assistance to us as we build the plant,” he said.
The Progressive Planet and Lafarge relationship
The production of cement, the binding agent in concrete, is responsible for about eight per cent of the world’s CO2 emissions. According to the Portland Cement Association, each pound of cement manufactured produces about 0.9 pounds of CO2.
“Typically, the Portland cement is about 10 to 13 per cent of the (concrete) mix,” Harpur explained. “The balance of the weight of that mix would be water, sand and aggregate . . . You could say there would be 10 times more concrete than the cement."
PozGlass 100G can be mixed with Portland cement at up to a 50 per cent ratio and can also replace fly ash in concrete. Fly ash is a by-product of burning coal, and releases CO2 when heated. It is one of the most common pozzolans used in the construction industry.
All coal-fired power plants in Canada are mandated to shut down by December 2029, meaning the industry needs a replacement for fly ash.
According to Harpur, the intention is that PozGlass 100G will not cost more per tonne than Portland cement.
In mid-January, Progressive Planet was approached unsolicited by Lafarge, who was impressed with what the company was doing with post-consumer glass.
"We are excited to provide technical guidance and support to Progressive Planet as they move through design, construction and operation of their pilot plant to show PozGlass can meet industry performance expectations and be produced at industrial scale,” Brad Kohl, president and CEO of Lafarge Western Canada said in a statement.
Lafarge’s products include aggregates, cement, ready mix and precast concrete. It employs over 6,900 at 400 sites across Canada.
Progressive Planet’s facility
Progressive Planet has hired Brightspot Climate Inc., a Calgary-based greenhouse gas emissions consulting firm, to measure the carbon footprint of PozGlass using data gathered from the pilot plant. Harpur estimates that once the facility is operational, Brightspot will have an established carbon footprint for it within 24 months.
The facility itself will be “several thousand square feet,” and utilize PozGlass 100G in it’s construction, something Progressive Planet has already done in one of its buildings.
"We've already put our first PozGlass in in May of 2022. I actually have a picture of where I wrote into the cement pad in our building – PozGlass 100G and my handprint,” Harpur said.
“What we are attempting to do with this pilot plant is prove the carbon footprint of our entire plant versus comparing it to a Portland cement production facility and to prove that the economics work.”
Earlier in March, the company reached an agreement with the non-profit Recycle BC to provide a steady supply of post-consumer glass for the plant. Recycle BC provides services for over two million households in the province.
The eventual goal for the company is to have its PozGlass 100G production co-located at cement kilns, as the PozGlass 100G process takes CO2 from flue stack emissions. It is also constantly looking to improve on its product.
We've made improvements to PozGlass every month for the last year in our lab. There is constant innovation going we are also working on creating glass that is made to replace cement as not from virgin materials,” he said.
“As long as I'm the CEO of this company, innovation will be a key component of what we do. We will be looking to improve PozGlass over the course of the pilot plant.”