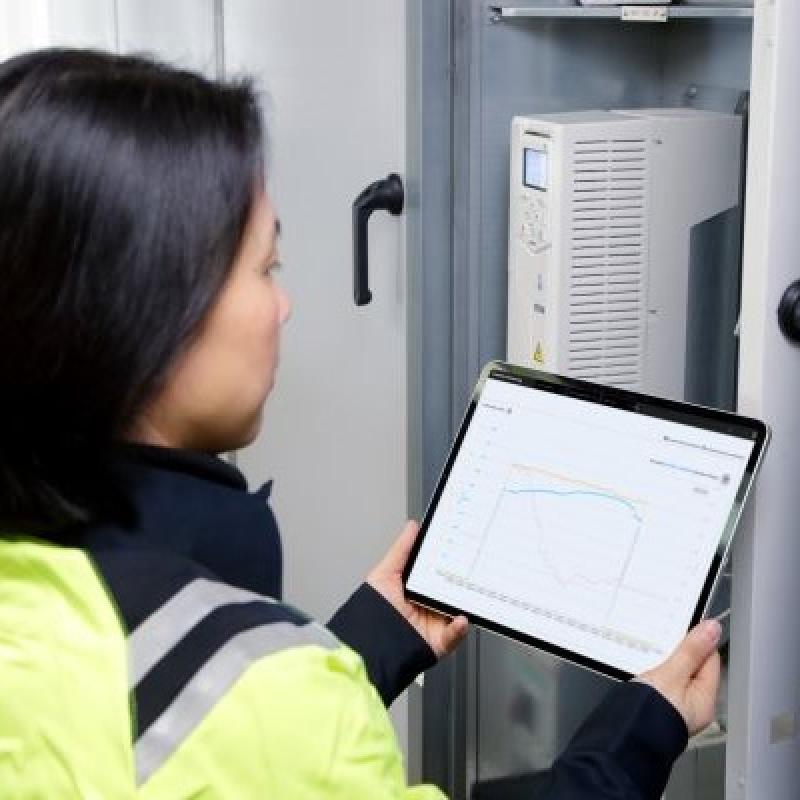
Modern property managers are being hit with rising energy costs and taking an increased interest in environmental goals, but also face an expectation for growth. One way to achieve all of this, ABB Canada says, is energy efficiency through digitalization.
The technology is designed to lower energy costs and improve competitiveness, helping building owners and operators achieve all of their goals.
“We can’t be sustainable or competitive if we’re not energy efficient. There’s no question between 'how do we maintain our competitiveness and still be sustainable and energy efficient?' The two go together completely,” Robert Palajsa, ABB Canada’s territory manager for smart power and smart buildings for southern Ontario, told SustainableBiz.
The Swiss technology company with its Canadian head office in Montreal, has been exploring digitalization, cloud-based services and use of data to optimize buildings and processes.
More broadly, ABB Canada is creating a blueprint for how industries can start on their sustainability journeys.
“We know how our energy costs have risen over the years, and this is a global phenomenon,” Palajsa continued. “To be energy efficient, it’s only making you more competitive. It’s only allowing you to be more competitive in the local market and the global market.”
Why energy efficiency is key for companies
The benefits of energy efficiency are significant — not just for the bottom line, but for a company’s competitiveness.
A mid- to large-sized industrial facility will have an electricity bill of tens of thousands of dollars per month, Palajsa said. If the owner can reduce the cost by 20 to 40 per cent, it boosts competitiveness and produces a return on investment in the long-run against a peer who does not adopt energy efficiency.
ESG-related components can be a key factor in accessing funding, and energy efficiency may also draw in younger generations who pay attention to a company’s environmental record, he noted.
Steps for energy efficiency
It starts with a plan, Palajsa said, but his experience indicates many companies do not know where to start. To illustrate, he offered insights from a guide ABB developed in 2021 with its partners which lays out how an industrial company can devise an energy efficiency plan.
The first step is to perform an energy audit. A company must establish a consumption baseline to develop or implement a strategy for the savings it wants to achieve.
Then the company must perform an asset audit to figure out which devices it uses, how they are controlled, if they are right-sized and efficient.
A company should understand how digitalization can be implemented. Digitalization of a facility is crucial because real-time data acquired by monitoring devices shows energy consumption and its impact on overall usage.
The data can then be analyzed for decisions like using higher-efficiency motors or automating a building’s cooling and heating system.
These steps apply to more than industrial buildings, Palajsa said, noting they are also applicable to commercial buildings, universities and hospitals.
ABB’s Ability offering
To improve building energy efficiency, ABB Canada offers a scalable software-as-a-service product called Ability that uses sensors or compatible equipment to send data to a centralized source (cloud-based or a local computer) that monitors energy use in real-time and finds efficiencies.
With more electrification and digitalization of building components, a common platform to collate the data becomes critical, Palajsa said.
For example, if a mechanical system is rated for 10,000 cycles and is reaching 9,000 cycles, Ability can alert the client the system is nearing its end-of-life. This pre-emptive maintenance helps to minimize breakdowns, Palajsa said, which is especially salient during the supply-chain challenges facing some industries today.
Another advantage is Ability’s load shedding. If an industrial plant starts operations in the morning during peak demand, the company pays more. Instead, Ability can turn off machinery’s non-critical loads until energy requirements drop to a sustainable level, which is when non-critical loads can be raised.
“ABB Ability allows you to in real-time monitor that, see what your peak demand is, see what your current loads are across your facility and then make those educated and simple steps . . . to reduce that,” Palasja said.
On average, users save 20 per cent to 40 per cent on energy, ABB Canada claims. Palajsa cited one company in Woodstock, Ont. that has saved over $750,000 on electricity costs per year with the help of Ability. In Europe, IKEA stores increased the energy efficiency of their HVAC systems by 25 per cent.
ABB Canada is working with a university in Toronto to improve its sustainability goals with a similar smart building solution.
Palajsa said other clients include a hospital that is digitizing its electrical systems and greenhouses looking to optimize heat and lighting consumption. Malls and apartments are also among other suitable properties for the platform.
Editor's note: ABB clarified the university in Toronto is not using Ability, but a different building automation platform.