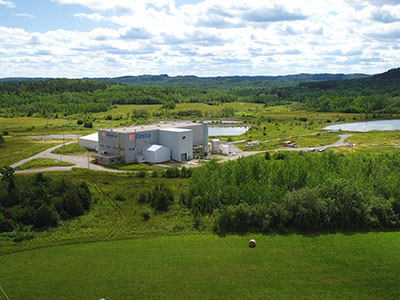
An aerial view of Electra’s battery materials park in Timiskaming Shores, Ont. (Courtesy Electra Battery Materials Corp.)
Electra Battery Materials Corp.’s scoping study for an integrated electric vehicle (EV) battery materials park in Timiskaming Shores, Ont. hopes to position the company as a key player in the expanding battery supply chain.
It’s not just Electra that is well-positioned in the Canadian battery supply chain. A new report from Clean Energy Canada and the Trillium Network for Advanced Manufacturing predicts given swift government action, a domestic EV battery supply chain could support up to 250,000 jobs by 2030 and add $48 billion annually to the Canadian economy annually.
With no government action, the supply chain would create 60,000 jobs and contribute $12 billion in GDP during the same time frame, according to the report.
“North American OEMs (original equipment manufacturers) in particular have started to realize that there was too much reliance on China. In fact, there are a couple of metals that are key to NMC (nickel, manganese, cobalt) batteries, between 75 and 90 per cent are processed in China,” explained Joe Racanelli, Electra’s vice president of investor relations. “Given some geopolitical developments over the past couple of years, the realization is that that’s not going to be advantageous or strategic.”
The study examined the economics and carbon footprint of a nickel sulfate refinery at the proposed Electra battery park in 2025 or 2026 producing 10,000 tonnes per year of battery-grade nickel sulfate and nickel equivalent precursor cathode active material — essential components of EV battery production.
According to a release about the study, Chinese refineries produce approximately 75 per cent of battery-grade nickel sulfate today.
“More importantly, it (China’s supply chain) won’t allow the OEMs to actually achieve the expected demand growth, so there’s a new interest in trying to determine and forge a new supply chain in North America.”
Electra’s battery park
The first part of the battery park involves the recycling of black mass in the fall of this year — an industry term for the waste comprising end-of-life battery cells. Then comes the commission of a cobalt sulfate refinery in the spring of 2023. Finally, the nickel sulfate refinery comes into play, all on the 600-acre property.
“Once we finalize the economics and get the appropriate approvals (and) sources of funding, we anticipate that happening within the next three to four years in total of all those activities taking place,” Racanelli said. “For the nickel sulfate refinery, we looked at a number of different feed types and the next stage will be used for fine tuning and selecting a couple of them to make the economics even more compelling.”
A refinery of that size would cost $731.2 to $864.1 million, with operating costs between $166.1 and $176.8 million per year.
Conversely, it’s expected to contribute $299.2 million of GDP impact during the construction phase, plus $551.8 million during the first 10 years of operation.
Scope 1 and 2 emissions would range from 14,000 to 16,000 of tonnes of carbon dioxide equivalent per year.
The location was attractive to Electra (ELBM-X) not just for proximity to its Toronto headquarters and the North American automotive industry, but also because the province’s hydroelectricity can power the battery park.
“We will be basically 50 per cent less carbon-emitting relative to similar size refineries that would be done in China,” Racanelli said. “From an end-user perspective, OEMs in the space are obviously looking to improve ESG commitments.”
The study was completed in collaboration with the federal and provincial governments as well as Glencore plc and Talon Metals Corp. in Toronto.
In June, Electra began discussions with the Quebec government on a new cobalt refinery in the emerging battery materials park in Bécancour, Que. According to Racanelli, that area has already attracted more than $530 million in investments from governments and companies interested in participating such as General Motors, BASF and Brazilian nickel miner Vale.
The North American supply chain
BloombergNEF’s second annual ‘Global Lithium-Ion Battery Supply Chain Ranking‘ in October 2021 found Canada placed fifth in battery supply chain potential, behind Sweden, Germany, the U.S. and China in that order.
At the same time, a recent survey had Canada drop to 13th out of 14 countries in global accounting firm EY’s EV Readiness Index. In 2021, it placed eighth.
According to the Clean Energy Canada report, Canada is the only country in the western hemisphere with known reserves of all the minerals necessary to manufacture EV batteries. It ranks sixth globally in lithium reserves, seventh in nickel and eighth in cobalt.
In August, the Canadian government signed memorandums of understanding with Volkswagen AG and Mercedes-Benz AG. According to a release, the Volkswagen agreement will focus on “deepening cooperation on sustainable battery manufacturing, cathode active material production and critical mineral supply, among others, and on setting up a Canadian office for PowerCo, (launched in July) Volkswagen’s newly formed battery company.”
The same release states the Mercedes agreement will focus on deepening connections with companies along the battery supply chain, establishing a sustainable critical mineral supply chain and identifying potential Canadian investments.
Auto facility investments and infrastructure requirements
In May, SustainableBiz reported on Stellantis’ $3.6-billion in investments at auto facilities in Windsor and Brampton to facilitate the production of EVs. In July, the Belgian Umicore N.V. announced a $1.5 billion investment to build an industrial-scale cathode and precursor materials manufacturing plant in Loyalist Township, Ont.
In this year’s federal budget, the government earmarked $3.8 billion to the development of a critical minerals strategy. As of June, total battery cell manufacturing investments in Canada in terms of gigawatt-hours stood at 120 compared to 700 in the U.S.
“The permitting process needs to be looked at, the investment process needs to be looked at, existing infrastructure needs to be looked at,” Racanelli said.
Globally, the battery market stands to be worth at least $477.7 billion by 2030. EVs use six times as many mineral inputs as gas vehicles, and by 2040, the International Energy Agency projects demand for critical minerals to grow by at least 30 times to meet demand for batteries.
“We have an abundance of raw materials that are needed for the supply chain but taking them from the ground and getting them into electric vehicles, it’s going to take some time and effort,” Racanelli concluded. “As mentioned, support from the permitting process and investments to ensure that facilities are developed, and ensuring that infrastructure to support the distribution and availability of that supply, is also going to be key.”