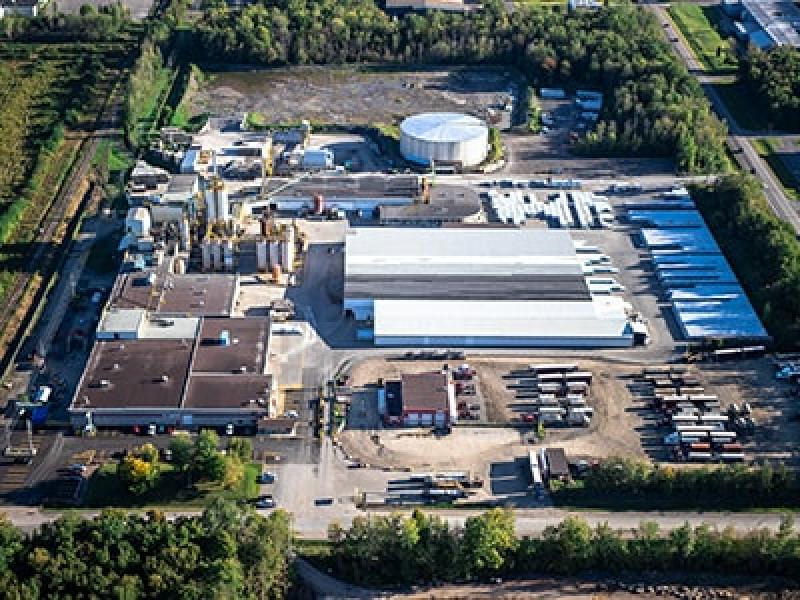
IKO Industries Inc. recently commissioned its asphalt shingle recycling line at its Hawkesbury, Ont. manufacturing facility.
Planning for the two-storey, 28,000 square foot facility began in late 2019. Groundbreaking took place in 2021 and it was completed last fall. The facility will recycle all unused material from manufacturing at the Hawkesbury location — with the aim of eventually creating a zero-waste facility.
When it reaches its capacity later this year, the IKO facility will be able to recycle up to 150 tonnes of shingle material per day. According to the company, a typical shingle recycling facility produces about 5,000 tonnes of recycled content annually.
“We had some additional land available that we had acquired that would allow for expansion of operations,” Derek Fee, IKO’s manager of corporate communications told SustainableBiz.
“We have had some delays in getting to this stage because of the restrictions that the pandemic imposed upon this particular capital project, but it is also one of the plants that has been in our production chain the longest. The original facility in in Hawkesbury dates back to the mid 70’s.”
IKO is a family-owned business established in 1951 in Calgary. Its first asphalt shingle facility was built in 1959 in Brampton, Ont., where it has its corporate headquarters today. The company has more than 3,500 employees and more than 25 manufacturing plants in Canada, the U.S., England, Belgium, Holland, France and Slovakia. The company ships roofing products to 96 countries around the globe.
IKO’s Hawkesbury recycling facility
Hawkesbury, with around 130 employees, is one of the company’s eight modern shingle manufacturing facilities. Fee did not disclose the production capabilities of the facility, only saying that it is producing in the range of “single-digit millions or more bundles of shingles” annually.
There is currently no firm date for when the Hawkesbury facility will reach full capacity, although Fee stated it would be later this year.
“The intent here presently, is to create a situation where we're able to create a plant that is effectively a zero-waste plant,” Fee said. “We're not at the stage yet, where we're going to be in a position to look at post-consumer waste as being part of that process just yet.”
Fee also said it could include recycling batches of shingles that don’t meet the company’s standards.
The company partnered with ASR (asphalt shingle recycling) Systems, based in Tennessee and Connecticut, to develop the shingle recycling system. ASR was founded by former IKO employee Dan Horton.
According to Horton in a release, IKO is the first manufacturer to develop a shingle recycling centre that reuses the recycled raw material output in the production of new shingles.
“He was at one time an employee of our company before he went out and started his own business. So the technology and the development of this business, a lot of that credit goes to Dan, because that was what he left to do,” Fee said. “But certainly… those technologies were new to us.”
IKO’s future recycling
There are currently no plans for a standalone recycling facility, with Fee explaining that IKO sees the Hawkesbury location as a pilot project the company can learn from and hopefully apply to its other shingle plants in North America.
The eventual goal is to achieve zero waste at all facilities. IKO also recently began a pilot recycling line in its Hagerstown, Maryland location that opened in 2022.
The company also has yet to fully explore the various applications for the recycled shingle material.
“I'm not gonna pretend to know what all of the applications are. I think we're probably still learning that,” Fee said.
“But at the present time, out of the material that you have as an end-product from this process, you’re going to reuse about half of it approximately in the roofing line as a component of coating material for new shingles, and then the other half would presently be things like sand and granules that would be sold to the road paving industry.”