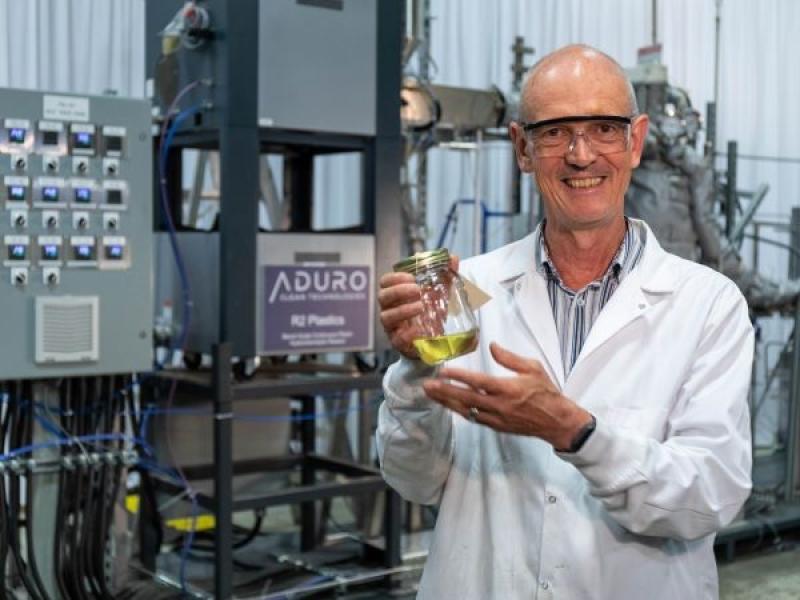
Years of research into making bitumen flow more freely has steered Aduro Clean Technologies (ACT-CN) onto a very different path these days - one which focuses on recycling plastics and helping to make cleaner fuels.
The London, Ont.-based company is the developer of Hydrochemolytic Technology (HCT), a process that breaks down long carbon chains in water to their more simple constituents through the use of chemical catalysts.
The process means sometimes difficult-to-recycle plastic waste can be turned into a recyclable liquid form. The chemical process can also separate the lighter and heavier components of bitumen to produce fossil fuels with lower greenhouse gas emissions, or generate fuel from vegetable and animal fats.
“Then you have a hydrocarbon product that you can do different things with," Aduro chief revenue officer Eric Appelman told Sustainable Biz Canada in an interview. "You could set it to fuel, and it’s a very good fuel feedstock . . . For every carbon atom that you keep in a loop, you save CO2 (carbon dioxide) in the end."
The company was recently featured on Viewpoint with Dennis Quaid, profiling its potential as an emerging sustainable technology.
With approximately 20 staff members in Ontario, Aduro Clean Technologies is nearing the planning stage for its pilot plant, a first step toward commercialization of the process.
Aduro’s origins
Co-founded in 2011 as Aduro Energy, Inc. by CEO Ofer Vicus and chief technology officer Marcus Trygstad, the company is based on research from chief scientist Anil Jhawar to find a simpler, more sustainable way of diluting viscous bitumen from Alberta’s tar sands.
Metal compounds separate carbon bonds in the feedstock, making HCT a sustainable chemical reaction as it requires minimal energy and fossil fuel use, and produces few greenhouse gas emissions. But as interest in the research slowed, Aduro pivoted to the biodiesel field and plastic waste management, according to Appelman.
HCT, it turned out, could also be used to convert plastic waste into a reusable feedstock, except with no fossil fuels required. Unlike pyrolysis, which uses heat, HCT is simpler and can work with cheaper, more abundant feedstock, Appelman explained.
“Every carbon atom that you can recycle is gonna help.”
Applications for HCT
Aduro has discovered three main applications for its solution: plastic recycling, lightening bitumen and renewable fuel processing.
Commonly used plastics polyethylene, polypropylene and polystyrene can all be recycled into a feedstock.
Appelman said this ensures the plastic waste stream can be valorized, giving plastic waste that would otherwise be lingering in landfills a second life as a fuel or recyclable material. This reduces demand for more petroleum to create more plastic or fuel, which cuts greenhouse gas emissions, he added.
“We are able to take pretty dirty plastic waste and convert it in a process that is not causing much of a loss in value,” Appelman summarized.
Bitumen and heavy oil require intensive processing to produce a usable fuel. According to Aduro, it means energy-intensive methods or diluting bitumen with lighter hydrocarbons produced from petroleum or natural gas.
HCT can separate heavy hydrocarbons using a chemical conversion rather than energy-intensive methods such as cracking. A side benefit is recovering metals such as nickel.
Finally, HCT separates oxygen from biofuel feedstocks like cooking oil or tallow for purer hydrocarbons. The resulting fuels can be an alternative to fossil fuels.
Where Aduro stands
Aduro has an HCT demonstration unit in Sarnia, Ont., which is capable of handling “just a couple of litres,” according to the Aduro chief revenue officer. Feedstocks from a local recycler are taken in by Aduro for testing.
Though the scale is currently small, the company’s expectations are being met and confirming its lab research in London can be scaled up. The quality of the output is exceeding expectations as well, he said. Aduro is also developing a solution for the waste at the end of its process.
More plastic waste from Germany is being ordered for testing with contaminated plastics, and Aduro is in talks with a major petrochemical firm for partnering on the pilot.
Instead of owning its operations, Appelman said Aduro expects to license its technology to other parties, where those users can apply their own tweaks to meet their needs.
The company hopes to attract institutional investors. Appelman expects Aduro to start construction on its first integral pilot plant and to have a firm concept for a factory in the coming months.