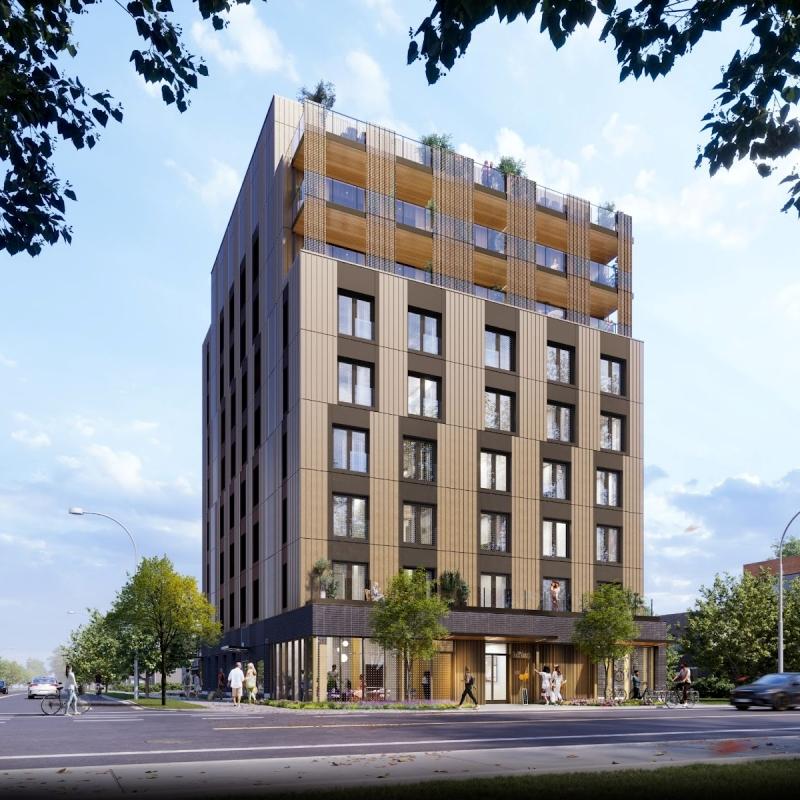
A nine-storey building being constructed piece by piece in a B.C. factory will become Toronto’s highest mass-timber residential structure when it is completed later this year.
The building, located at 230 Royal York Dr., will have 58 market-rate rental units, along with two replacement rentals, and will be manufactured at Intelligent City’s facility in Delta, B.C.
“We’re starting assembly in May, and we are hoping to have the construction envelope done in August and then the interiors have to be finished. The building will be move-in ready end of the year,” Oliver David Krieg, president of Intelligent City, told Sustainable Biz Canada.
The company is partnering with Windmill Developments and Leader Lane Developments on the project, alongside Oben Build, Lang Wilson Practice in Architecture Culture Inc. (LWPAC) and Moses Structural Engineers.
The building’s structure and envelope are expected to be built over four months, according to the company. Mass timber costs could run as much 20 per cent less versus concrete construction, the company said.
Intelligent City has been producing with wood for seven years and was originally founded in 2008.
“We chose mass timber as the building material because it’s a sustainable building material that only emerged in the '80s and '90s in Europe and came to North America just a decade or two ago, and it’s really good for mid- to high-rise construction; it’s very cost competitive,” Krieg said.
Timber is also stronger by weight compared to steel and concrete, which translates to savings in such things as transportation, he added.
The numerous benefits of mass timber
Building this way also helps lower a developer’s carbon footprint.
“The trees absorb CO2 (carbon dioxide) as they grow. In fact, they absorb more CO2 than what the material wastes because they release the oxygen again," Krieg said. "If you look at the sequestration of the CO2, it’s a carbon-negative material. It basically absorbs carbon as it grows, and is still carbon negative, even after harvesting and processing and putting into building compared to concrete and steel.
“But even if you don’t include the sequestration, if maybe it gets burned later, or it gets put in landfills, it still has much lower GHG (greenhouse gas) emissions in its production cycle or life cycle, than steel and concrete.”
For developers, the modular process can provide a much shorter timeline to completion.
“The advantage is ultimately that they can de-risk their construction process, and they can accelerate the construction process, which means they can turn around their capital faster and ultimately build more with the same capital that they have.
"The big challenge with construction is that you lock in your capital until the building is finished. If you can accelerate that by three or four months, then you get your capital back faster; your cost of money goes down, and you can deploy more projects,” he said.
What exactly is mass timber?
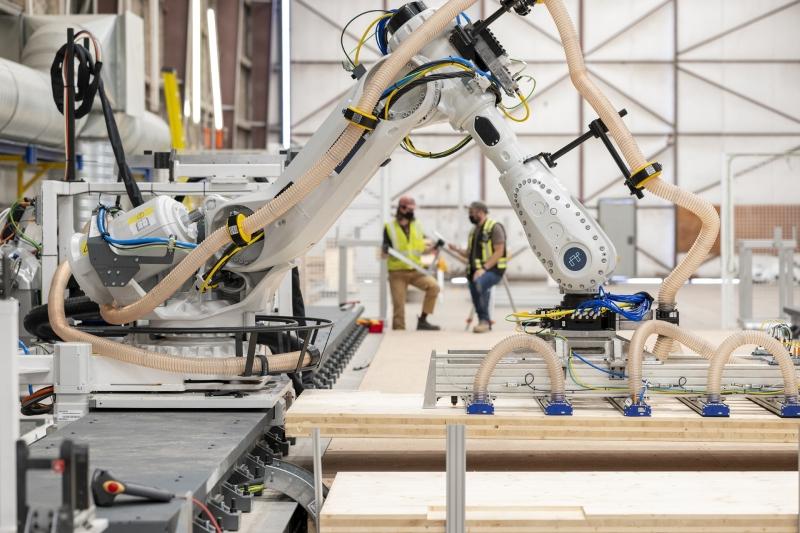
“Mass timber is lumber glued together into larger panels. Technically, they have to be at least 96 millimetres thick to be considered mass timber under the building code," Krieg explained.
"It is essentially similar to plywood, except instead of laminating veneer, you’re laminating lumber together into large panels, and those panels can be as big as a truck. They’re really massive, and because they’re glued together in different directions, they are dimensionally also very stable.”
It is also safe enough to be used for residential purposes, according to Krieg.
“It’s a fire-safe material. It can be used in high-rise because it is so solid and massive. It doesn’t actually burn. It chars and that’s why you can leave it exposed.”
The Intelligent City model is also effective at keeping residential energy costs down, he said.
“The envelope panels that we make are highly energy efficient, so they are very well insulated so you have just a nice environment and generally, the building is a very efficient building.”
The mass timber environment is also biophilic, meaning it’s natural and organic nature are esthetically pleasing for humans to be near.
“Mass timber has been actually proven to balance the interior moisture and air quality, because it is a breathing material, and it’s a more natural environment as well. It really is a nicer place to live in,” he said.
The lasting impact of mass timber
There are no concerns about durability, according to Krieg, as it’s just a matter of taking proper care of the buildings. “. . . if you look at other timber structures, like temples in China and Japan, they have been standing there for 800 years because they are protected. If the material doesn’t get too wet or cold, it will last.”
As well, concrete building can be inherently flawed sometimes due to the specific construction method.
“If you look at concrete towers, most of them are constructed in the way where the concrete slabs stick out and become balconies. So that means the inside of that slab is insulated inside your apartment, and the outside is in the outside temperature, and so you have a huge temperature difference between inside and outside that deteriorates the structure of the building,” Krieg said.
Mass timber is also on the radar of Prime Minister Mark Carney, who visited Intelligent City's headquarters this week. "This is exactly the type of innovation that we need to tackle the housing crisis and the economic crisis that has been brought on by President Trump's trade war," he said.
Increased deployment in Canada
Canada is well positioned to deploy mass timber construction on a wider scale than is currently being done.
“I think that almost all housing — especially in the mid- and high-rise segment — could be made out of mass timber and could be prefabricated using systems like ours. A lot of these buildings could be built in a similar way because Canada’s forests have enough sustainable growth that you could build all residential construction three times over with the available harvests that we have annually,” Krieg said.
“If we deployed or harvested these resources in a sustainable manner, we could really switch our industry over and really use the resources we have in our country.”