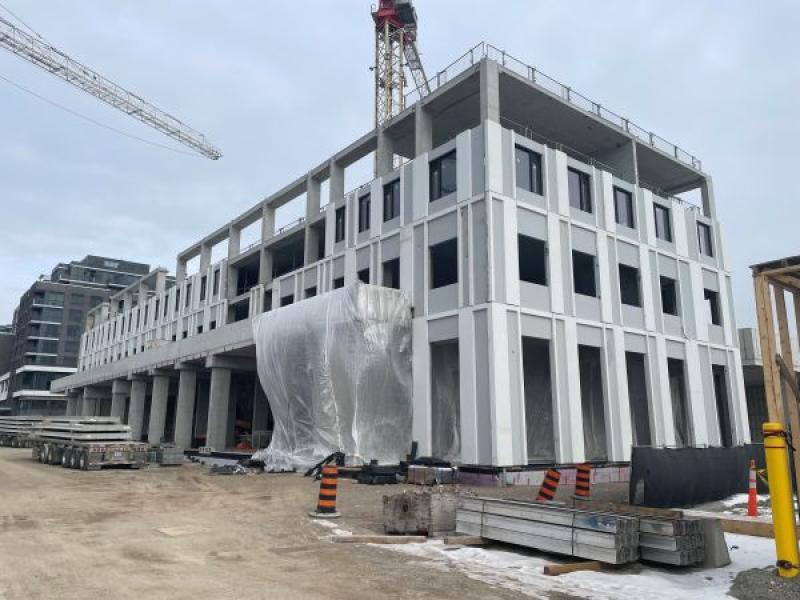
An 11-storey rental building slated for KingSett Capital’s Valhalla Village development in Etobicoke will be one of the first in North America made from prefabricated concrete components, courtesy of Modular Precast Systems Inc.
The Bradford, Ont.-based company is providing the parts from its 110,000-square-foot facility, which are designed to be easily assembled on site. It partnered with Italian company Structurama and Bolton, Ont.-based Avenue Building Corp. on the modular construction technology.
Not only does it speed up construction by two to three months over traditional means, it cuts costs by 10 to 15 per cent and reduces the embodied carbon by 18 per cent, according to the company.
The work on Valhalla Village is a major step up for the company, Modular Precast Systems CEO Glen Pestrin said in an interview with Sustainable Biz Canada. It marks its first structural project — one that is load bearing — after focusing primarily on architectural precast, the non-load bearing portions such as facades.
“Just like anything new there was a little bit of a learning curve in the beginning, but now things seem to be streamlined and on schedule, and our hopes are to beat the schedule,” he said.
Toronto-based KingSett, a private equity real estate investment firm and developer, has prioritized sustainability at Valhalla Village. It is designed to be net-zero carbon with features such as tapping into geothermal heating and reducing embodied carbon by optimizing the unit sizes and building mechanical systems.
Faster, cheaper construction, with less carbon
At Valhalla Village, Modular Precast Systems is employing precast floor slabs, beams and columns. Assembling the components, Pestrin said, is as simple as putting Lego blocks together, requiring minimal training and less than a third of the workforce compared to regular construction.
The sweet spot for its modular construction is mid-rise buildings, a “massive market in the City of Toronto”, Pestrin said. It will be effective up to 17 to 18 storeys, and could be utilized up to 30 storeys.
By making the components at its facility, the company can be more efficient with concrete as the process takes place in a controlled environment with reusable forms, Pestrin explained. As it pares away excess concrete consumption, less of the carbon-intensive material is generated.
Further carbon reductions are achieved by minimizing material deliveries and propane consumption on construction sites during colder months, and generating less waste on the job site.
A life-cycle analysis that compared a tower made from Modular Precast Systems’ construction method versus cast-in-place found the precast method shaves 21 per cent of the greenhouse gas emissions from transportation and 72 per cent from construction, contributing to an overall reduction in embodied carbon.
Outlining the speed and efficiency of Modular Precast Systems' technique, Pestrin said the company is completing one 18,000-square-foot floor with exterior cladding every 10 to 12 days.
Construction is on schedule and is expected to be completed in April.
Industry complacency holds back prefabrication
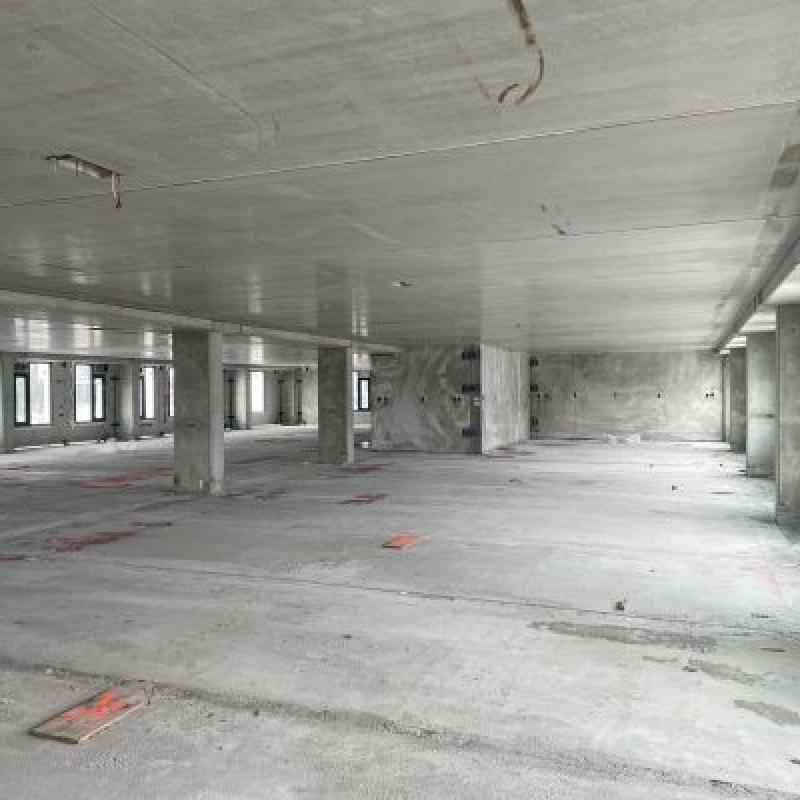
Pestrin, who is also the CEO of Toronto-based York Marble, Tile and Terrazzo Inc., is commercializing an interest in precast construction he formed decades ago. When he worked at his father’s architectural precast facility in the 1980s, he learned about the method and was drawn to the idea.
“It gave me a strong foundation on the basic principles,” he said about the experience, and allowed him to make informed decisions on the equipment to purchase and where to update his knowledge with his newest company.
He founded Modular Precast Systems in 2020 for three reasons:
- discovering an opportunity in the small Toronto market;
- his business partner Christopher Liberta, the CEO of State Window Corporation, was interested in vertically integrating his company’s systems into other products such as architectural precast; and
- inspiration from the large number of structural precast buildings in Europe.
Since taking on Valhalla Village, the company has received letters of intent for other projects.
Pestrin believes prefabricated buildings can help address the problems in Canada’s housing market, particularly high costs and limited supply. But despite well-documented advantages — faster build times, lower costs, overcoming Canada’s labour shortage, and structural longevity — modular buildings are uncommon in the country.
Complacency is the main reason prefabricated construction has not caught on in Canada, Pestrin suggests. Banks and the construction industry are more comfortable with conventional construction and are reluctant to explore innovations. Other restraints are the need for standardization and a market that demands features modular construction cannot provide, he added.
“The need for change hasn’t been incentivized enough for people to try something new and different.”
EDITOR'S NOTE: This story was updated after publication to correct the nature of CEO Pestrin's father's business, which was an architectural precast facility, not a real estate company. Sustainable Biz Canada regrets the error. Additional information and clarifications have also been added to the story.