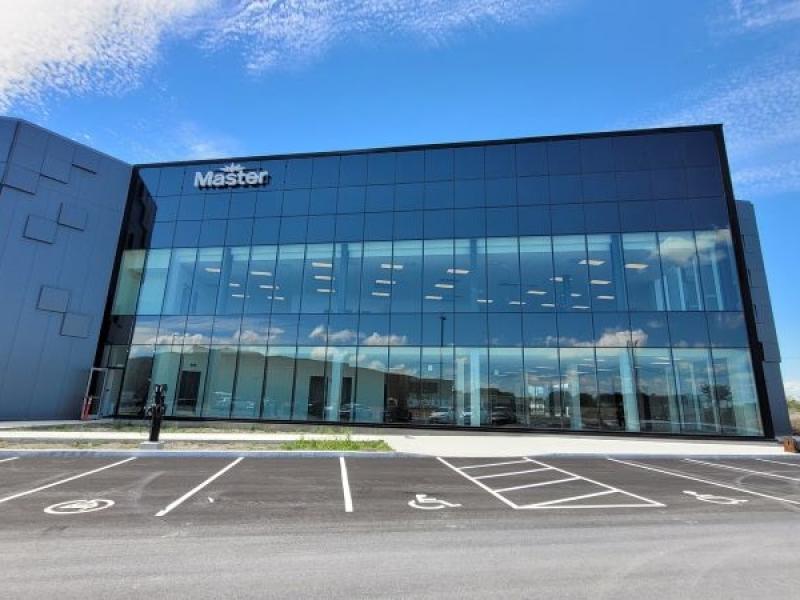
A new LEED Gold-certified distribution centre in Montreal is the first of its calibre for HVAC equipment designer and distributor The Master Group, embodying its effort to shrink its carbon footprint.
Opened in mid-November, the company’s 300,000-square-foot eastern distribution centre in Saint-Bruno-de-Montarville consolidated two previous distribution centres, moving operations to the Écoparc Saint-Bruno built by Montoni Group.
Designed for zero-carbon operations, the building is heated with electric heat pumps, incorporates solar panels for energy generation and supports low-carbon transportation.
Master Group is one of the largest HVAC companies in Canada, president John Kaul told Sustainable Biz Canada in an interview. It supplies tens of thousands of dealers and installers through 56 branches in Canada and 30 in the U.S., with two other distribution centres in Calgary and Vaughan (Toronto area) – adding up to a building footprint in the millions of square feet.
The decision to prioritize sustainability in its newest distribution centre is directly related to the company’s main business in HVAC equipment, Kaul said. Electrification of buildings requires switching from fossil fuel-based equipment, leading the company to offer more heat pumps in response to market demand.
To fulfill its sustainability strategy, the company put greater attention on the carbon from its own operations and buildings.
Mastery of its mechanical system
Construction of the building started in the spring of 2023 and while Kaul could not disclose total costs for the development, Master Group's investment was $12 million.
Construction materials used for the distribution centre are fully recyclable. To minimize waste when consolidating the two Montreal sites, the company recycled, reused or refurbished 90 per cent of the interior parts, equipment and furnishings into its new facility.
The most innovative feature of the eastern distribution centre is its mechanical system, which is at the “cutting edge” according to Kaul. Designed by Master Group’s engineering team, he said it utilizes highly efficient heat pumps. Combined with air tightness, insulation and a new airflow system, the building is expected to cut annual heating consumption by over 75 per cent and cooling by 30 per cent.
Though not new to Master Group, the inclusion of solar panels allows it to generate renewable energy.
Four electric vehicle chargers are at the distribution centre, joined with bike racks to accommodate cyclists.
Water is another area of sustainability Master Group has prioritized; rainfall is to supply about half of the water for the plumbing system.
To marry well-being and sustainability, a green roof, greenhouse, a conservation zone, rain garden and sports track are present, elements of the building Kaul is proud to highlight.
Sustainability through distribution
Transportation and freight is Master Group’s largest source of operational greenhouse gas emissions, so the decision to build a large distribution centre is based around reducing the greenhouse gas emissions from transportation, he explained. The buildings enable this by placing logistics closer to its customers.
An example is an upcoming investment in a large distribution centre in the U.S., which is be announced in Q1 2025.
Additionally, Master Group uses routing technology to find the most efficient paths to the end-user.
Kaul said further steps for sustainability will be addressing waste from its operations and reducing the carbon from its choice of building materials.
With the Canadian government providing financial support for decarbonization of heating systems, Master Group is working to provide the heat pumps to take advantage of grants for residential and commercial buildings, Kaul said.