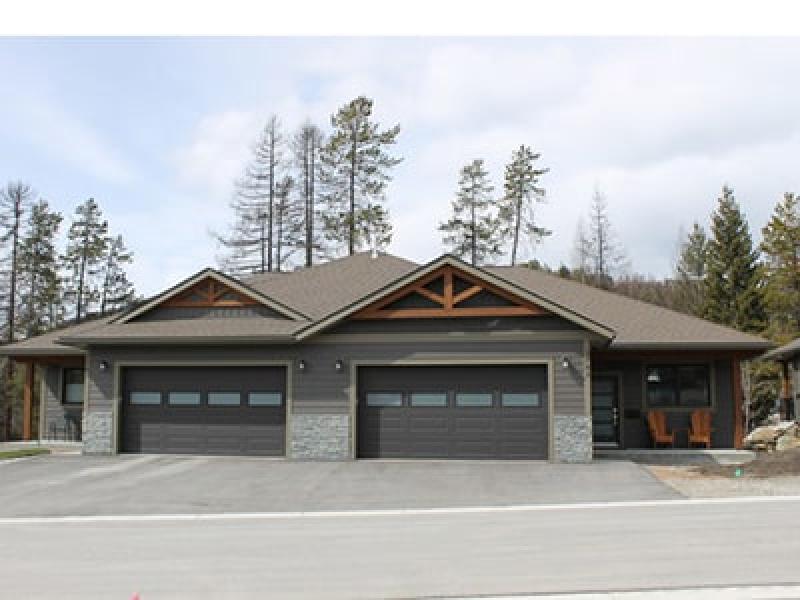
FortisBC Energy Inc. has teamed with Tyee Homes and other provincial builders to develop six net-zero-ready homes case studies for different climates across B.C.
Tyee constructed a home in Kimberley, B.C. that achieved Step 5 of the B.C. Energy Step Code – the highest level – by incorporating passive solar design, a high level of airtightness and a high-efficiency natural gas combination space and water heating system.
Located within a seven-unit duplex development, the home was one of Tyee Homes' first builder development projects.
Tyee and FortisBC found the home 37 per cent more efficient than a typical new home. It also used roughly a third of the natural gas of the average B.C. home.
"FortisBC has been offering incentives for energy-efficient new construction for several years," said Tanya Rumak, the program manager of conservation and energy management at FortisBC. "The program has taken different forms and supported different levels of energy efficiency, essentially ratcheting up year-over-year to encourage builders to continuously go to higher levels of energy efficiency.
“Tyee Homes has been participating in the program for several years. As early as back in the day when we were supporting ENERGY STAR in homes. So they have always been interested in pursuing something higher in terms of energy efficiency.”
FortisBC also completed case studies with Hargrave Construction in Campbell River, Icon Homes Ltd. in Quesnel, Fernwood Developments in Maple Ridge and Smallworks Ltd. in North Vancouver. A home in Kimberley was constructed by resident Sanford Brown.
The B.C. government is targeting for all new Part 9 residential buildings to achieve Step 5 and meet net-zero-energy-ready requirements by 2032.
A regulated utility, FortisBC employs over 2,000 people and serves approximately 1,064,800 customers across British Columbia. It owns and operates approximately 50,493 kilometres of gas transmission and distribution pipelines.
It supports builders through financial incentives, mainly through its New Home Program.
Tyee Homes’ Kimberley development
Tyee Homes used products such as SIGA building wrap and tape to ensure high levels of air tightness. The company achieved air tightness levels of approximately 0.7 air changes per hour, with the equivalent leakage area of approximately 5.2 inches by 5.2 inches. The smaller the leakage area, the less heat will escape the home. The equivalent leakage area in a typical Step 3 home is approximately 12.5 inches by 12.5 inches.
The home incorporated combination boilers for space and water heating, passive solar design and features in-floor radiant heating on both levels – a standard for all Tyee construction.
Moving forward, Tyee plans to continue to work with an energy advisor to see what design modifications can be made to meet Step 5 in all of its units.
Tyee Homes was able to access incentives from FortisBC – $10,000 for achieving the energy performance and $800 for working with energy advisors.
“The residual incremental cost of this home . . . if you look at the overall cost of purchasing a home, really is minimal,” she said. “It could be compared to perhaps upgrading your countertops.”
FortisBC’s case study series
“What we did with this case study series was tried to highlight builders that were pursuing the top tiers of the step code,” Rumak said, “as well as looking at different housing types in different climate zones throughout B.C.”
That includes both multifamily homes and duplexes, she explained. The important thing was to analyze different building types across a variety of climates.
The lowest step codes were the laneway home in North Vancouver and the detached home in Maple Ridge, both Step 3.
The case studies were meant to serve as inspiration for other builders in the province to try something similar, for example with the mechanical systems, the windows or the insulation.
The common theme that emerged was a focus on the building envelope being paramount. It’s also the most difficult aspect to change once the home is constructed, Rumak said.
“I've found after being in (the building industry) for so many years that if there's an example of something that has been done before, then it quickly starts to snowball from there,” Rumak said. “Other builders are keen to try it.”
FortisBC is “always” looking for builders to feature in future case studies, with Rumak stating there are a couple more under development. Not all future case studies will focus on the Step Code. One of the future builds will involve an operationally decarbonized home – e.g. one that uses both electricity and renewable gas.
Rumak has also been seeing more provincial applications in pursuit of higher Step Codes, indicating a market shift.
“They have something to work towards. They know what they have to transition towards,” she said. “So I would say the industry is really keen on learning and figuring out how to implement this before the next code change happens.”