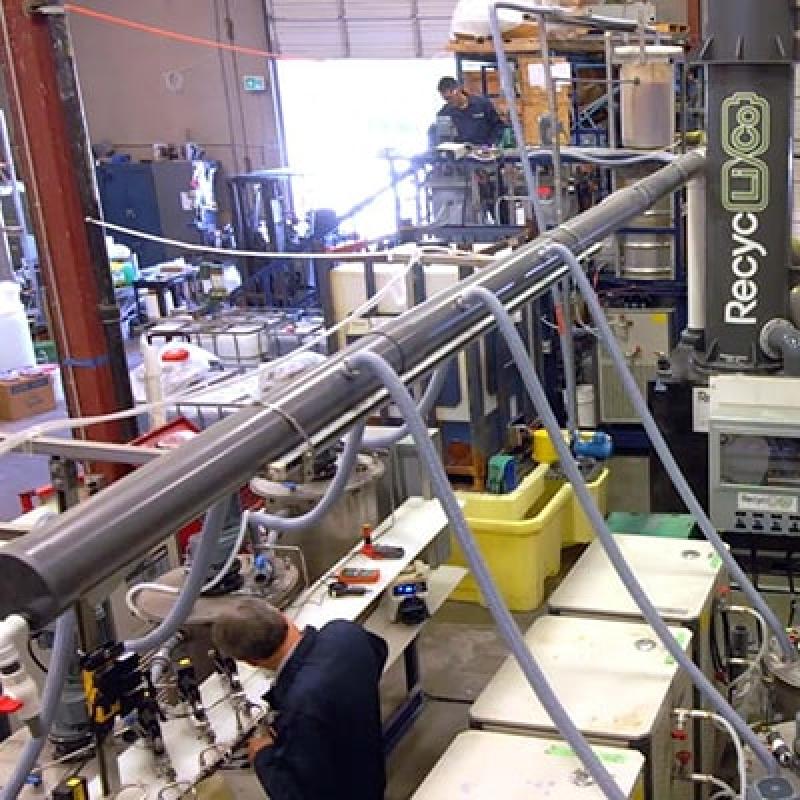
The CEO of recycler RecycLiCo Battery Materials Inc. believes his company can be a major part of a transition which he says will move lithium-ion battery material sourcing from large-scale mining to commercial-scale recycling.
To this end, RecycLiCo (AMY-X) is ready to take its patented, closed-loop Zero Loss Battery Production recycling process around the world to promote what it calls an environmentally friendly and effective means of recovering more desirable minerals from battery waste.
“Eventually at a point, we're going to reach this inflection point where we're no longer mining for a majority of our materials, we're actually recycling for the majority of our new materials,” RecycLiCo CEO and director Zarko Meseldzija told SustainableBiz in an interview.
“Even if you look at the lead-acid battery industry, the majority of the materials being used the new lead-acid batteries is coming from the recycling operations as well. That's really where we see our technology being able to do the same.”
Originally, the Surrey, B.C.-based company was known as American Manganese Inc. and in 2012, was planning on bringing low-grade manganese deposits in Arizona to production.
Meseldzija said conventional methods of manganese production were not economical thanks to the low grade, but the company had developed a cost-competitive process for extraction.
“It was around 2016 where (regarding) that patented technology, and really the properties of manganese and some of the metals you see in lithium-ion batteries, specifically the cathode . . . we saw these parallels in being able to test and see if those similar processing techniques would work.”
That process promises near 100 per cent extraction of cathode materials including lithium, cobalt, nickel and manganese from lithium-ion battery waste. The result is reusable material known as cathode precursors. A cathode is one of the electrodes in a battery.
RecycLiCo’s Zero Loss Battery Production process
RecycLiCo’s process pulls critical minerals out of the black mass – the industry term for crushed and shredded end-of-life battery cells – and puts them in a solution that separates out any further impurities.
Meseldzija said what sets this process apart from other hydrometallurgical processes is its reuse of certain chemical reagents and much of the water.
He compared the process to other recycling methods, such as pyrometallurgy, which breaks down the material into its individual constituents. By selling precursors, RecycLiCo skips the energy, chemical and water costs associated with recombining the critical minerals.
Since 2016, the company has progressed from lab testing to a demonstration plant in Vancouver. In November, the plant advanced to the lithium recovery stage alongside its research and development partner Kemetco Research Inc.
The process is capable of producing battery-ready materials from cathode chemistries including lithium iron phosphate, lithium manganese oxide, nickel manganese cobalt, nickel cobalt aluminum and lithium cobalt oxide.
Meseldzija described RecycLiCo’s business model as asset- and capital-light. Instead of constructing a new facility at every location in the world that needs batteries recycled, the company is opting to partner with companies and set up its technology at the source.
“It's not so much for us to build our own stand-alone recycling plant and take waste from different electric vehicle companies and battery companies,” Meseldzija said. “It's more to adopt their technology within their facilities, where they're producing waste from end-of-life batteries from battery production itself.”
In addition to recycling materials, this avoids emissions caused by shipping the materials back and forth. It also means battery recycling production will vary depending on the partnership, with Meseldzija suggesting between 2,000 tonnes to 20,000 tonnes of annual capacity at individual sites.
The technology and process can handle multiple tonnes per day.
RecycLiCo had enlisted U.K.-based consultant Minviro to undergo third-party testing of its process, which verified it produces 62 per cent less carbon dioxide emissions than competing hydrometallurgical processes.
Aside from Canada, the process is patented in the U.S., India, China, Japan, South Korea and Australia.
RecycLiCo’s recent partnerships
“I think we're really at that scale-up-ready stage. So I think, given the lab-scale work, we've done piloting work, demonstration plant work, (given) a lot of these positive results we're getting from industry we're really kind nearing those stages,” Meseldzija said.
“2023 is a year to be kicking off some commercial agreements.”
Already in 2023, RecycLiCo has announced partnerships in Korea and Japan. In early January, it announced a memorandum of understanding with Korean electronics manufacturer Sonid Inc. to establish a lithium-ion battery recycling facility.
An unidentified Korean cathode manufacturer used RecycLiCo’s recycled-upcycled nickel manganese cobalt oxide precursor in a battery cell, noting that it outperformed other recycled cathode precursor materials.
RecycLiCo also delivered samples of its battery-grade lithium carbonate and lithium hydroxide to battery manufacturers in Japan and South Korea. Those manufacturers were also unnamed, referred to only as the “top manufacturers in the region,” in a company release.
They are currently reviewing the samples and RecycLiCo hopes that will lead to new agreements in coming months.