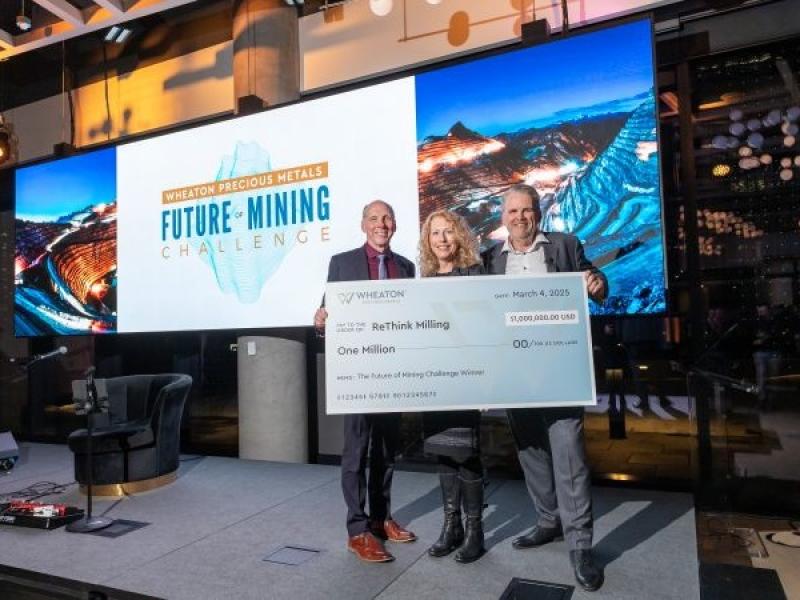
From left, Steve Wilson, chief technology officer of ReThink Milling; Gillian Holcroft, president of of ReThink Milling; Randy Smallwood, the president and CEO of Wheaton Precious Metals. Wilson and Holcroft accepted a US$1-million prize from Wheaton. (Courtesy ReThink Milling)
New grinding technology by Toronto-based ReThink Milling Inc. can significantly improve the energy efficiency and bottom lines of mining operations, a prospect that has earned it a US$1-million prize from Wheaton Precious Metals.
Originally formed as a non-profit and consortium of mining companies addressing the inefficiency of breaking rocks, ReThink is commercializing a technology with two variants to take on the problem. When combined, the company says they can slash the electricity consumption of grinding by almost two-thirds.
It avoids grinding media such as steel balls, instead using two rotating cylinders for more efficient grinding.
This lowers carbon emissions from mining sites that generate electricity with diesel, while requiring less materials for the machinery and transportation of fuel and parts.
“(It has) huge impact on greenhouse gas reductions and the overall operating costs to produce these metals,” Gillian Holcroft, president and CEO of ReThink, told Sustainable Biz Canada in an interview about the implications of the technologies.
The mining sector is a significant source of climate-changing emissions, with consultancy McKinsey estimating it is responsible for four to seven per cent of global greenhouse gas emissions. 440 Megatonnes, a project of the Canadian Climate Institute, said mining is the only heavy industry in Canada that increased its emissions between 2005 to 2022.
The potential of ReThink has led Wheaton, a Vancouver-based precious minerals streaming company, to choose its technology as winner of its Future of Mining Challenge. ReThink will use the funds to upgrade the scale of its technologies as it works toward demonstrations and commercialization.
ReThink’s grinding technologies
The two variants ReThink is seeking to bring to market are Conjugate Anvil Hammer Mill (CAHM) and MonoRoll. Both break down rock and ore into smaller particles so the minerals and metals can be extracted and refined.
CAHM is a coarse grinding machine that can process over 50 tonnes of material per hour. The materials then take on a finer grind via the MonoRoll, which can currently manage two tonnes per hour.
The MonoRoll is capable of “reducing material from half an inch to 100 microns; from a marble size to the thickness of your hair,” ReThink chief technology officer Steve Wilson said in the interview.
Both run more efficiently than conventional equipment such as high-pressure grinding rolls and ball mills, ReThink said, and can serve as a one-to-one replacement.
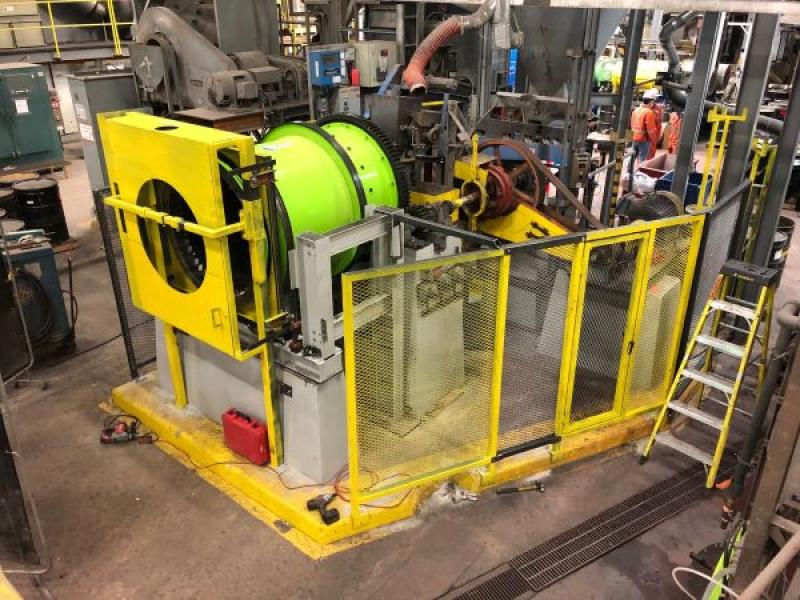
The electricity in most mining operations is generated by fossil fuels such as diesel. ReThink’s equipment is designed to tackle the carbon emissions from electricity on mine sites due to its high efficiency.
If CAHM and MonoRoll are combined, the electricity consumption of a grinding circuit can be slashed by 65 per cent, enabling greenhouse gas emissions from grinding to be mitigated by 70 per cent. An additional benefit is that it does not require steel balls to assist with the grinding — in contrast to most fine grinding machinery — so greenhouse gas emissions are further abated.
CAHM and MonoRoll can also shrink transportation emissions by reducing the demand for transporting diesel and steel balls to remote mines, Holcroft added.
Wilson said if both were used across Canada, an estimated 3.5 megatonnes of carbon dioxide would be saved per year — equal to taking 800,000 passenger vehicles off the road.
The two technologies can also save on cost as much as carbon, he said. ReThink estimates $20 million to $50 million of cost savings in fuel and electricity per year if adopted.
The path to commercialization
ReThink is confident its products can work on all rocks and ores, and also expects it will have applications in the cement and aggregate industries.
Both have been piloted at the Quebec City facility of Corem, a non-profit that supports the research of mining corporations.
Before it can reach commercialization, ReThink plans to scale up the capabilities of CAHM and MonoRoll, Holcroft said.
Using funds from Wheaton, the company plans to upgrade CAHM to process 100 tonnes of materials per hour, doubling its current capacity. For MonoRoll, the goal is to boost capacity 10-fold to 20 tonnes per hour and make it transportable.
ReThink is looking to raise $15 million to run a mine site demonstration to prove the commercial viability of its technology. If successful, Wilson expects it will be operating in Canada by Q3 to Q4 2026.
The intention is to demonstrate CAHM and MonoRoll, but each system can be showcased separately and at different sites. To test both, ReThink estimates it will need $18 million in funding.
If there is “huge demand” for its machines, Holcroft said it would make the most sense for ReThink to license its technology to several manufacturers. Alternatively, the company could sell its equipment and follow up with licensing fees.
“We don’t want this thing to take 10 years to commercialize. We have a plan that, if we get the money, we will be able to have a first commercial unit operating by the end of next year,” she said.