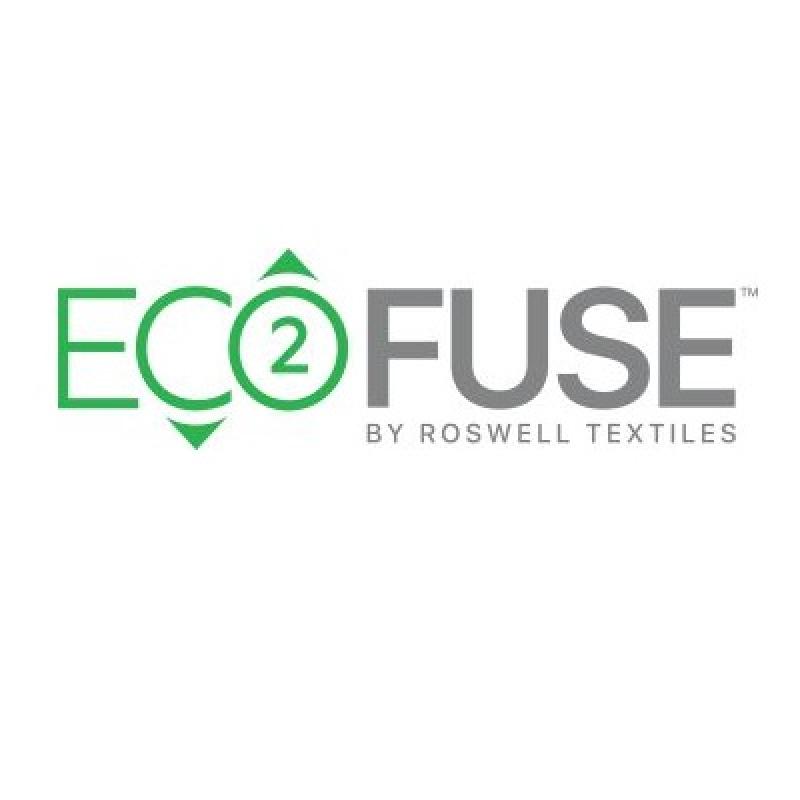
Roswell Textiles, a Calgary-based fabric manufacturer, has launched a plant-based biopolymer named ECOFUSE as a greener alternative for filters and masks traditionally made out of plastic.
The company was formed in 2020 to answer a call from the federal government to supply meltblown filtration media for Canadian personal protective equipment (PPE) manufacturers during the COVID-19 pandemic. To start the business, it received funding to develop the first commercially available, made-in-Canada meltblown nonwoven materials.
Co-founder and president Kyle Fiolka told SustainableBiz Roswell Textiles pivoted to developing sustainable fabrics after he and his two partners were struck by the amount of single-use waste leaving the company’s doors destined for incineration or a landfill.
It transitioned from a petroleum-derived plastic named polypropylene to a more sustainable feedstock. It developed its own process and machinery to produce the plant-derived biopolymers.
“We wanted to reduce the amount of waste that was going out the door, or change the type of waste so maybe it could be handled differently at the end of life, or change the carbon footprint of the material going out the door so that ultimately converters of this PPE and end users would have a lower carbon footprint of their product than what the conventional polypropylene was offering,” Fiolka said.
The result is ECOFUSE, a biodegradable material which reduces waste and cuts carbon dioxide emissions related to its life-cycle by almost two-thirds compared to plastics on the market.
About ECOFUSE
ECOFUSE is a meltblown biopolymer which is spun-woven using high velocity hot air to draw down the polymers into microfibres through a single process. Roswell Textiles, Fiolka said, opted to use biopolymers in a novel application because the company wants control over ECOFUSE’s creation and sustainability features.
The feedstock is derived from corn, sugar cane and sugar beets sourced from North American and international suppliers.
Fiolka said ECOFUSE feels and looks like a conventional polymer while maintaining a stable shelf life and holding to standards for flammability, hydrophobicity (water resistance) and filter efficiency.
“The product needs to perform really well and be cost effective, otherwise there’s no impact on net carbon reduction in an industry, as there is lower adoption. Our goal is focused on making sure that, from a performance perspective, we meet or exceed the expectations, and we’re as close to on-price expectations as you can get to conventionals,” he said.
ECOFUSE can be utilized for filter media like face masks and respirators. Roswell Textiles is also exploring prototypes for absorbent pads, HVAC filters and food filtration.
Low carbon and compostable
Fiolka said ECOFUSE offsets carbon because it replaces plastics made by converting hydrocarbons. Roswell Textiles says it cuts carbon dioxide equivalent emissions by 65 per cent compared to polypropylene, and some products are compostable in an industrial composting facility.
As ECOFUSE decomposes, it breaks down into its core elements including carbon, oxygen and water, Fiolka explained. It leaves behind no residuals and no water or soil contamination.
ECOFUSE meets the ASTM D6400 standard for industrial composting. The actual timeline for decomposition depends on the individual product.
It also meets the requirements for the United States Department of Agriculture’s BioPreferred program that indicates ECOFUSE is 100 per cent bio-based.
Even if it is incinerated, Roswell Textiles says the gases are less damaging to the environment than fumes from polypropylene.
Where Roswell Textiles hopes to be
Roswell Textiles can produce 720 tonnes of ECOFUSE per year. This year, production will reach 1,320 tonnes
ECOFUSE is used by Precision ADM Medical, a Winnipeg-based medical product manufacturer behind VIRALOC ECO and PRECISION ECO.
Roswell Textiles has other customers it cannot disclose, according to Fiolka, as some clients are using ECOFUSE in prototypes or are in the launch phases of their own products.
The company is raising funds to scale up and is looking for partners to use ECOFUSE in commercial applications.
There is also the potential to use ECOFUSE as a carbon offset. Because it reduces CO2 by displacing plastics with biopolymers, offsets can be created through a voluntary carbon credit program such as Verra, which Roswell Textiles is exploring.
Fiolka hopes to see the products used in many industries beyond its established space in PPE and the medical field and into industrial, commercial, and food and beverage applications.