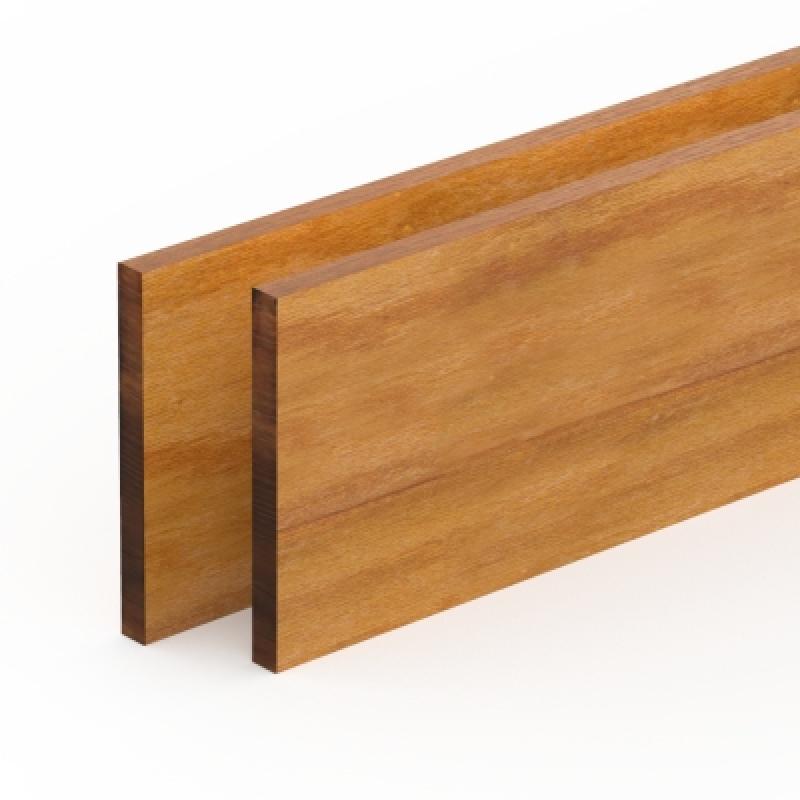
Materials start-up InventWood hopes to transform the sustainable construction sector with its patented MettleWood product, which uses advanced technology to turn wood into a material 60 per cent stronger, 80 per cent lighter, and more sustainable than conventional steel products.
MettleWood is the trademark name for Super Wood, the densified and delignified form of wood invented by a team of University of Maryland (UMD) researchers led by materials science and engineering professor Liangbing Hu.
Hu is also the director of the Maryland Center for Materials Innovation, located on the UMD campus at College Park, Md.
He founded InventWood in 2016 as a UMD spinoff company. It began developing Super Wood as a sustainable material that could replace carbon-intensive steel and concrete in the construction process and effectively serve as a long-term means of carbon storage.
Looking toward the future, his company hopes to develop a wide range of greener materials that could ultimately replace the glass, metal and plastics found in buildings and vehicles.
InventWood recognized in Washington
Hu and fellow InventWood executives were honoured at the American Possibilities: White House Demo Day event held on Nov. 7 in Washington, D.C.
InventWood was one of 40 tech innovators showcased at the annual event which is intended to promote significant inventions as well as the latest advances in the field of technology.
"The invitation to this event is recognition that Professor Hu has become one of the top innovators in academia and the United States," University of Maryland president Darryll J. Pines said in a release.
Densifying and strengthening wood by removal of lignin polymers
Hu led his team of researchers at UMD to develop the chemical treatment process that increases the strength of ordinary wood by partially washing away the lignin – the polymer that holds cellulose fibres in wood together – inside the wood's molecular structure.
This process breaks down the cellular walls of the wood membranes and uses compression to bring the cellulose nanofibres into alignment, simultaneously strengthening the wood while reducing its thickness by 80 per cent.
"It’s a nanocomposite," Hu explained in a February interview with Chemistry World. ". . . My goal is to amplify the performance of nanofibres inside this big, porous composite (by) making wood as dense as possible, which makes it strong . . . or making it as porous as possible, which results in good insulation material and allows you to tune the optical properties . . . you can pretty much do anything."
Following his research and discovery of Super Wood, Hu, who has described himself as a "wood nanotechnologist," licensed his patented Super Wood technology to InventWood, the company he launched under the auspices of the University of Maryland.
Now marketed under the tradename MettleWood, the product could be the harbinger of a significant decarbonization of the built environment by serving as an alternative material to the structural beams, columns and connections that are normally composed of carbon-intensive steel and concrete.
According to InventWood, this has the potential of reducing carbon emissions by 37.2 gigatons over the next 30 years and is one of only very few technologies capable of lowering the carbon footprint of the construction sector by replacing steel and concrete with MettleWood and like materials.
InventWood building wood manufacturing pilot plant in Maryland
Last November, InventWood was buoyed by a $27 million U.S. Department of Energy ARPA-E SCALEUP grant. These funds will be primarily allocated towards the construction of a 90,000 square-foot R&D and pilot plant in Frederick, Md.
The manufacturing facility will have the capacity of producing one million square feet of MettleWood board per year that will initially be targeted for use as exterior cladding for high-rise buildings.
"Traditionally, one of the main obstacles to using wood cladding in tall buildings has to do with fire resistance," Josh Cable, InventWood CEO, said following the announcement of the ARPA grant. "Because of its density, MettleWood is highly fire resistant and even self-extinguishing.
"As a result, we believe MettleWood can achieve the Class A fire rating needed to overcome this challenge."
Apart from cladding, MettleWood could allow architects and design teams to replace carbon-intensive steel and concrete structural beams with a stronger, lighter wood-based alternative.
"The future of advanced cellulose-based building materials is extremely promising, and InventWood and its technologies are uniquely positioned to capture this opportunity," Cable added.
Dr. Hu to the rescue
This summer, Hu was named Distinguished University Professor, the highest honour the University of Maryland can bestow on a faculty member. He obtained his PhD in physics at UCLA in 2007 where he studied carbon nanotubes as the basis for his doctoral thesis and subsequently did postdoctoral work at Stanford University in Palo Alto, California.
Over the past decade, he has been the co-author of 25 patents and has a further 45 patents pending.
It was during his original studies on carbon nanotubes at UCLA that he was first drawn to the extraordinary potential for transforming wood into a variety of materials with multiple applications. One of his most important discoveries was that the structure and ion-transport capabilities of cellulose nanofibres in wood are similar to those of carbon nanotubes, while being sustainable and low-cost.
Harnessing wood to decarbonize the built environment
Steel and concrete account for 21 per cent of total carbon emissions and are primarily used in the built environment, according to Architecture 2030. Cement and steel are the principal materials used in buildings, cars and skyscrapers.
According to a March 2022 paper in Nature, the construction industry is "among the dirtiest on the planet." Figures cited in the study show production of cement alone generates 2.3 billion tonnes of CO2 emissions per year, while the manufacture of iron and steel releases a further 2.6 billion tonnes in greenhouse gas emissions.
This accounts for 6.5 per cent and seven per cent of global CO2 emissions, respectively, attributable to concrete being the second-most consumed product on the planet after clean water and that steel relies on highly carbon-intensive methods of production.
Hu believes his densified MettleWood product is not only stronger, lighter and more durable than steel, but that it can ultimately "replace steel and concrete".
"For steel, you get about 1.85 kg of carbon dioxide emissions per kilogram. For wood, you remove about 1.8 kg," Hu explained. "Essentially, trees act as giant carbon dioxide stores. Growing wood sustainably to use as a steel substitute isn’t just renewable: it’s better for the environment."