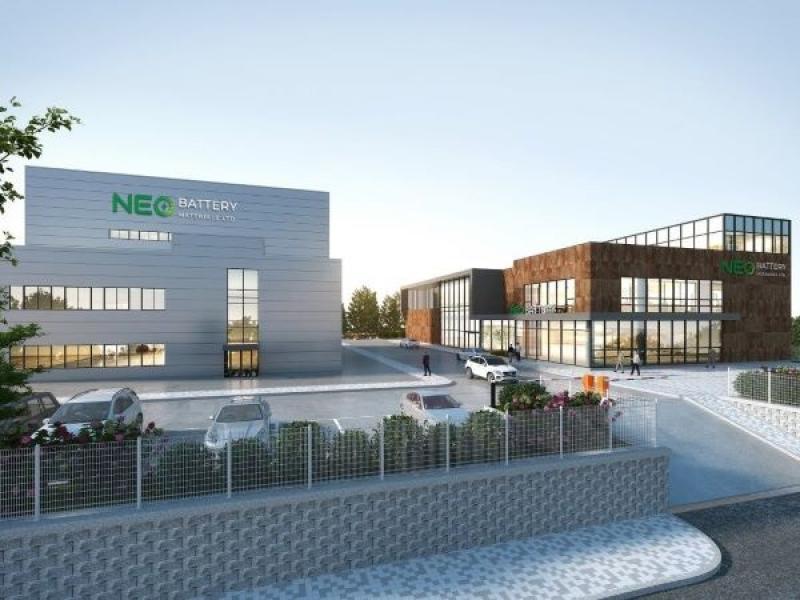
A planned joint venture between NEO Battery Materials Ltd. (NBM-X) and Australian company Lotus Energy Recycling would result in NEO receiving the materials it needs to produce highly effective electric vehicle (EV) batteries from used solar panels.
The letter of intent signed in October lays out a blueprint for Toronto-based NEO to use Lotus’ technology in Canada.
High-purity silicon from Lotus’ recycling technology would go toward producing silicon anode materials that are coated with a polymer developed by NEO, which improves the performance of lithium-ion EV batteries. The anodes have been shown to have superior resiliency, faster charging speed and increased energy capacity compared to graphite competitors, according to the company.
“We know for a fact the first generation of the solar panels that have been deployed, let’s say late 2000s, early 2010s, they would most likely be retiring somewhere around 2030, 2032,” Danny Huh, senior vice-president of strategy and operations for NEO, told Sustainable Biz Canada in an interview. “There is going to be a massive influx of these effectively dead solar panels.”
In response, the company is aiming to extract the valuable resources that can be re-used, in order to reduce the amount of waste that goes to landfill.
A commercial battery facility in Canada will be critical to the joint venture, according to the plan, with the lease for the land it will be sited on being addressed.
Partnering with Lotus on solar panel recycling
Lotus’s recycling technology would be hosted in a separate building on NEO’s proposed 350,000-square-foot site, taking in end-of-life panels from solar cell operators or solar farms through supply agreements in North America. The first phase is anticipated to produce 240 tonnes of silicon anodes per year, then scale up substantially to 5,000 tonnes at its last stage.
To house its facility, NEO signed a non-binding letter of intent with a Canadian municipality in September to lease land.
The process shreds solar panels, filtering out materials such as glass and metals. The silicon cells are subject to acid leaching to separate the silicon from the other materials at 99.99 per cent purity, according to Huh. The purity of the base silicon from the solar panels is so high it can be added directly to its products, he added.
At full capacity, enough material to supply one to two million EV batteries per year will be made, Huh said.
The company is pursuing the joint venture with sustainability and waste-cutting in mind, seeking the “next extent” of circularity, according to Huh. It's a partnership that came about by coincidence, as Lotus asked NEO to test its recycled silicon just as NEO was considering such a project.
An estimate by the International Renewable Energy Agency suggests Canada could dispose of 800,000 tonnes of expired solar panels by 2050. As only about 10 per cent of solar panels are recycled, the waste problem will only intensify as the technology gains wider adoption across the globe.
NEO has also partnered with South Korean silicon recycling company INNOX eco-M to take recycled silicon and silicon-oxide powders from semiconductors as a feedstock for its anodes.
“We’re trying to achieve circularity within not only the battery supply chain, but also the semiconductor and solar supply chain,” Huh said.
NEO’s silicon anode
NEO’s silicon anode helps overcome a critical problem with the material, which will break down after around 100 charge cycles, Huh described. Compared to peers, it is far more flexible, helping to raise EV battery driving range by over 20 per cent, according to the company. The manufacturing process is also done at 60 to 70 per cent less cost than competitors, it adds.
The company is optimizing its silicon anode in South Korea, where it maintains research labs and pilot projects that can produce four tonnes of material per year if operating 24 hours every day.
NEO’s joint development agreement with a Fortune Global 500 chemicals company to improve the performance of its silicon anodes is bearing fruit, Huh said. Certain metrics have met or exceeded industry standards, so the scale of testing is being elevated.
More details on its commercial facility will be announced in the next 24 months, Huh said, which would include the status of its land agreement and procurement of engineering and construction firms.