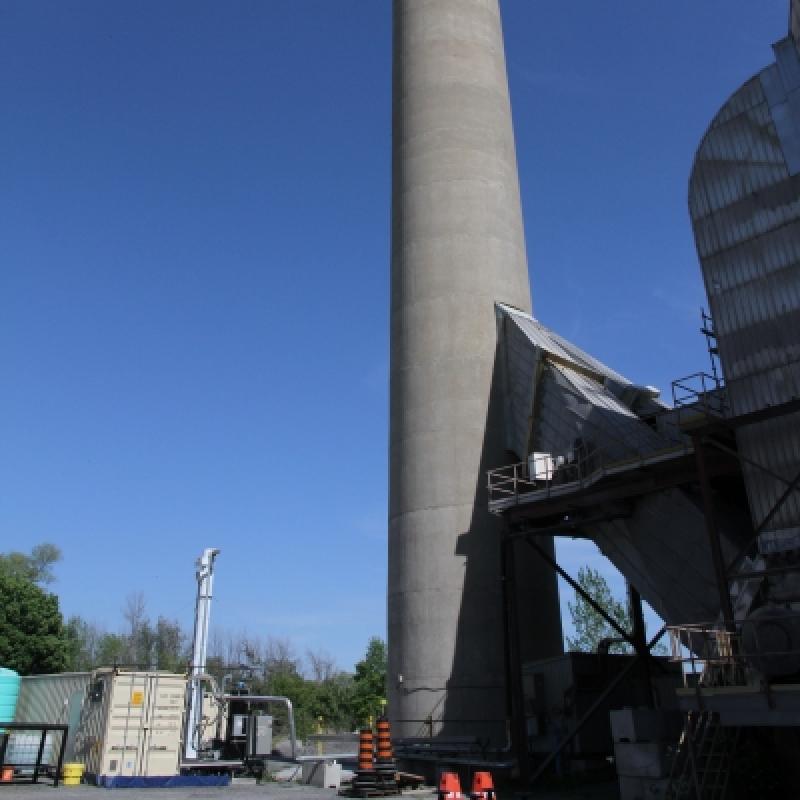
Lafarge Canada has launched a pilot project with the goal of capturing and transforming carbon dioxide (CO2) emissions from its cement-making operations.
Working with Ottawa-based carbon technology company Hyperion Global Energy Corp., the global cement and concrete manufacturer is allowing the company to use its process output at its Bath, Ont. facility.
“It’s an important part of our decarbonization strategy. There’s no one strategy. There’s no one silver bullet, but we are pursuing a number of strategies and this is one that is very interesting,” Rob Cumming, head of sustainability and public affairs at Lafarge Canada Inc. (East) told Sustainable Biz Canada.
“We provide them with our facilities to use, our CO2, so to speak.”
At its heart, the tandem carbon recycling technology uses a circular process to transform waste emissions from flue gas into minerals that also capture and sequester up to 98 per cent of carbon, which is then used in cement-making production.
“The tandem system that (Hyperion CEO) Heather Ward has developed with our partners is a great example of technologies that we refer to as mineralization," Cumming said. "I think that’s one of the more promising category solutions for our industry because when you mineralize something, you’re producing essentially aggregates - stones and gravel.
"We are one of the companies that sells those items.”
How Hyperion's carbon-capture system works
Hyperion deploys a drop-in, metal shipping container system that captures output and converts it on site. The technology offers the equivalent of taking 30,000 cars off the roads for every system it deploys, according to the company’s website.
The final product will be used in Lafarge’s ECOPact low-carbon concrete product.
“Fundamentally it makes limestone into very, very fine particles or very powdery, if you will. The calcium chloride, it reacts with the CO2 in their proprietary process and you come up with calcium carbonate, CaCO3, to give you the formula, for calcium carbonate, which is limestone,” Cumming said.
“To produce that kind of fineness of product, you’ve got to grind very, very heavily with a lot of energy intensity . . . The actual process itself (produces) very fine particulate to start with. I think that’s another strong feature of this type of technology.”
This is in contrast with current methods, he added.
“In our process, we’re actually doing the opposite: we’re taking limestone and heating it up to drive off CO2 molecules, which gives us lime, which react with other materials to form sand. It’s this very circular kind of process for taking that released CO2 and repurposing it into a limestone product.”
The goal of the pilot program is to remove as much as 1,000 tonnes of CO2 per year from the facility’s operations, according to a press release. Hyperion aims to ramp up output by as much as 10 times during the coming year.
Lafarge looks to transform its production methods
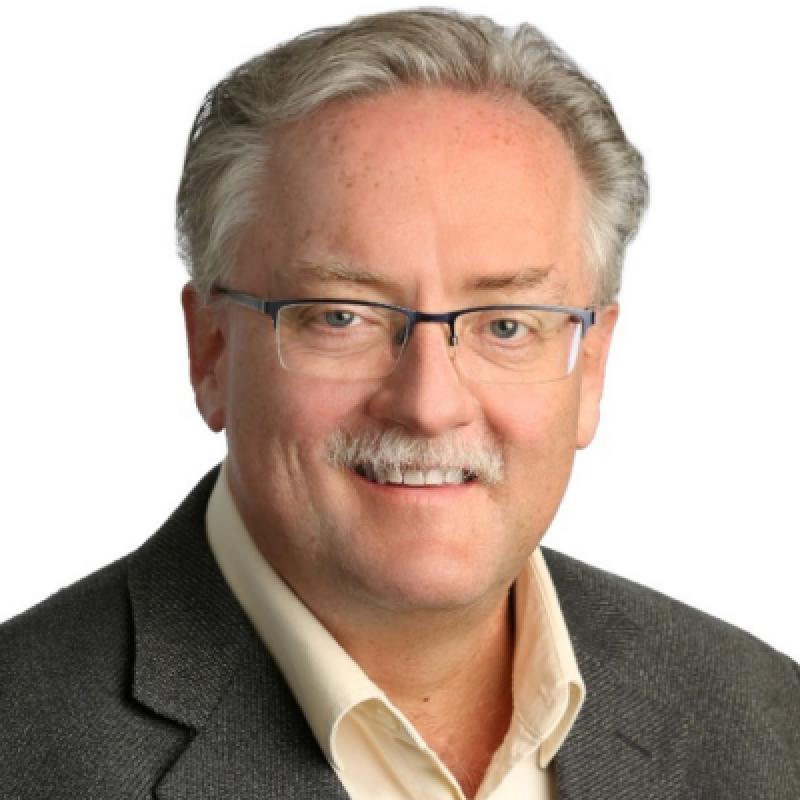
By using this unique system, Lafarge hopes to revolutionize its own production.
“If you look at traditional carbon-capture utilization strategies, you have to capture the carbon first, and then you do something with it. The mineralization technologies, many of them, including the tandem process, the actual chemical reaction process itself captures CO2, so they can take our flue gas pretty much as is from our process and produce a product right out of it,” Cumming said.
Late last year, Lafarge announced another carbon-cutting effort to offer steel slag to be used in an innovative concrete produced by Montreal company CarbiCrete. As well, the company decreased its carbon output in a Richmond, B.C. facility by 35 per cent.
Lafarge is Canada’s largest producer of aggregates, cement, concrete and asphalt, operating 400 sites and employing 6,900 workers.
A clear-cut approach for Lafarge
For Lafarge, the goal of the initiative is simple, Cumming said.
“I think it’s proof of concept. I know Heather’s team is hoping to increase by tenfold in the next round of testing to demonstrate commercial readiness. They’re taking this opportunity to optimize and fine-tune the process. We’re analyzing the results of the product itself, and providing advice back to them.”
With efforts such as this, the company is hoping to improve on its recent successful carbon emissions reduction efforts. Its carbon intensity has decreased by 25 per cent over the past three years, according to Cumming.
And it’s well on its way to a goal of a 40 per cent reduction by 2030.
“It’s hard to be an innovator and developer of a new process, so we’re very pleased to help her team to move forward and also talk to the broader world about what the industry is doing," Cumming said. "These kinds of technologies that Heather’s developing is what we’re going to look at in post-2030 commercialization, as we adopt these newer technologies.”
Despite news of increasing CO2 levels, which is “tough” and can leave him “discouraged,” Cumming said he has high hopes for the success of the project.
“I’d love to see a commercial system in five years, is one of our plans. I’d like to see further development around competition for low-carbon building materials, to create that market, or give preference to lower carbon products. Those are the kinds of things we’d like to see and I think it’ll just spur more and more innovation over time.
“This is what gives me some optimism.”