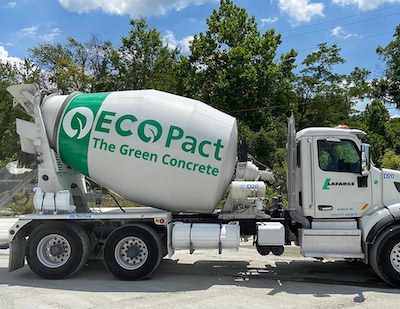
Lafarge Canada is beginning its rollout of its ECOPact line of “green” concretes across Canada. (Courtesy Lafarge)
Lafarge Canada is rolling out its ECOPact carbon-reduced concretes across Canada and the Americas after encouraging results in Europe. If widely adopted by Lafarge clients, ECOPact could make a sizeable contribution to sustainable construction: the company sells roughly 15 million cubic metres of ready-mix concrete annually.
Boasting 6,000 employees and 400 sites across Canada, Lafarge says it is moving toward a significantly reduced carbon footprint and circular construction incorporating high-grade, used building materials. The ECOPact green concrete line offers a certifiable carbon-footprint reduction of 30 to 70 per cent.
“The strength of Lafarge Canada is harnessed in our collective and collaborative efforts to reduce our carbon footprint at the source of all constituents we produce (aggregate and cement) and in harmony with our sustainable concrete-mix design approach and strategy,” said Jessica Assaf, Lafarge’s manager of corporate communications for eastern Canada.
The products meet all required performance standards.
“All ECOPact concrete will meet or exceed the strength and durability specified for a project,” John McCabe, vice president and general manager, Ready Mix, eastern Canada, told SustainableBiz in an email exchange. “High CO2 reduction requires changes to the traditional mix that can impact performance; however, our process adapts the mix design to deliver the required performance.”
Four grades of ECOPact concrete
Four ECOPact products are either currently available or on the horizon, ranging from ECOPact (30 to 50 per cent reductions) to ECOPact Prime (up to 70 per cent), ECOPact Max (over 70 per cent) and ECOPact Zero (100 per cent, currently including offsets).
They largely differ based on the carbon intensity involved in the manufacturing process. ECOPact Max and ECOPact Prime are long-term goals for Lafarge. Currently, such extreme carbon reductions are difficult from a practical perspective.
“Carbon neutral without an offsetting strategy will be very challenging in the next five to 10 years,” McCabe explained. “However, we remain optimistic in our capabilities to reduce the CO2 emission in our concrete by up to 70 to 90 per cent. Electrification of transport and the circular economy to replace fossil fuels are among our sustainability initiatives.”
ECOPact Zero is the ultimate objective, effectively a net-zero product. Carbon capture is another long-term Lafarge objective as it moves toward becoming a net-zero operator.
“As far as carbon capture, our goal is to utilize methods and technology to capture the greatest reductions in CO2 and adopt effective technologies that can further reduce CO2 in our products, which is what we have developed with the ECOPact product range and continue to expand,” said McCabe.
Reducing the impact of cement
In addition to recycling high-grade materials, another area of focus is cement, which constitutes 10 to 15 per cent of a typical concrete mix to bind sand, gravel and other components. But producing cement is nine times more energy intensive than the manufacture of concrete itself – meaning it can account for up to 80 per cent of the GHGs according to Environment Canada.
McCabe said while reducing the amount of cement in the mixes is one part of the process, ECOPact is substantially more than just that goal: “Our carbon-emission reduction actions are thought of at every stage of the supply chain. One cannot design low-emission mixes based on cementitious replacement.”
In a typical cement manufacturing process, gravel, sand and water are combined. This is heated in a kiln with temperatures nearing 1,500 degrees then cooled, finely ground and combined with other materials like gypsum, limestone, fly ash or slag to produce cement. The resulting mixture is added to water and aggregates to form concrete.
A blended cement introduced to Canada in 2011, Portland Limestone cement (PLC), performs the same as standard concrete while reducing carbon emissions by 10 per cent.
The majority of greenhouse gases emitted are from fixed-process emissions resulting from the chemical process that occurs when limestone breaks down under heat. PLC incorporates more ground-up limestone, producing 10 per cent fewer emissions at no additional cost.
ECOPAct versus traditional concrete
Cleaner-burning fuels can also reduce the environmental impact of cement production, explains Samantha Bayard of Environment and Climate Change Canada. These range from construction and demolition materials to agricultural waste, hydrogen-based fuels or electric heaters that run on renewable power. To control air pollutants from some alternative fuel sources, proper emission control devices must be incorporated into the process.
‘McCabe said like any specialty mix, the ECOPact products have higher price points than traditional mixes due to higher production costs, but that will vary depending on the mix required for a particular job.
“This (pricing) is dependent on the level of (carbon) reduction being requested and is provided to the purchaser early in the process allowing a decision to be made in the design process,” McCabe wrote, noting a number of other technical factors will also be involved. “Specialty mixes such as ECOPact often require additional constituents, increased production capabilities, additional research and development, certification and documentation . . .”
But the long-term benefits of carbon reduction must be factored into the overall project to better assess its broader value.
The concept of carbon offsetting is also growing in importance. The benefits of carbon offsetting are not only carbon-emission reductions, but depending on the offset project, they can lead to other social, environmental or biodiversity benefits. Lafarge is using these offsets in its efforts to achieve carbon neutrality.
Other available initiatives
In addition to products like ECOPact, Environment Canada identifies three other initiatives the construction industry can undertake to reduce its environmental impact:
* incorporating steel slag – a by-product of steel manufacturing – and curing the molded mixture with CO2 to produce concrete blocks;
* carbon upcycling, which reduces the proportion of cement in concrete by adding an enhanced fly ash – a coal combustion product – increases the strength of concrete by up to a third. Using technologies to introduce recycled CO2 into fresh concrete reduces carbon footprint without compromising performance;
* CO2 can also be used as a raw material in the production of aggregate.
Bayard said carbon taxes imposed across Canada are encouraging companies to take these, and other measures to reduce their footprints.
“By making polluting activities more expensive a price on carbon pollution creates alternatives for individuals and businesses such as cement manufacturers and the construction industry to choose cleaner options,” she explained.
The government is also considering requiring the use of low-carbon concrete in its tendering process, Bayard added.