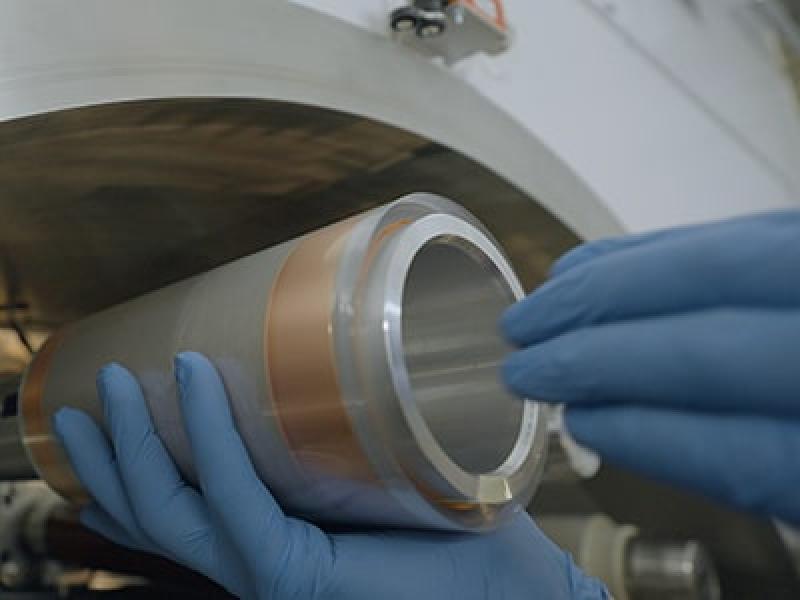
Li-Metal Corp.'s new CEO Srini Godavarthy has set out the company's updated priorities: which include a focus on scaling anode production, lithium metal production and continuing to grow industry partnerships.
In April, the Toronto-based lithium metal anode and lithium metal technology developer enlisted Mustang Vacuum Systems Inc. to provide physical vapour deposition (PVD) machines to Li-Metal (LIM-CN) and its customers. The machines will increase the productivity and commercialization of Li-Metal’s roll-to-roll PVD technology, which produces battery anodes via its vaporized lithium metal deposition process.
The company expects to achieve commercial anode production in 2024.
“Initially the thought process of the company was, we would scale up (lithium) metal first. Because there’s an existing market for metal . . . Metal is important, but metal is more capital-intensive. And given that we are where we are, we want to be profitable, at the same time managing our capital raise that's needed,” Godavarthy told SustainableBiz.
“So we are prioritizing anodes short-term because we see that in the next 18 to 24 months, we can start generating substantial revenue from anodes – while we continue processing metal with strategic partners, we still have some work to do.”
Li-Metal’s anode production
Anodes are one of two electrodes that comprise a battery, including those in electric vehicles (EVs). In traditional anode production, chunks of lithium are flattened into a very thin foil. Li-Metal uses what it refers to as deposition technology, using lithium carbonate as its main input.
The end product has the same storage capacity, but is more cost efficient and allows for more cells to be used in the battery. To date this year, the company has produced more than 5,787 metres of sample lithium metal anode material – compared to 4,200 metres in 2022.
The company is expanding its workforce at its Rochester, N.Y. anode facility to meet customer demand.
Li-Metal has commissioned a pilot-scale lithium metal anode scrap reprocessing facility, which will allow the company to recycle its anodes back into ingots to be reused. However, Li-Metal has not decided where the reprocessing facility will be located, and there is no timeline for completion.
For the anode production with Mustang, Godavarthy estimates it will take six to nine months to get the machines operational.
“You need about three to four machines to generate about half a gigawatt (of) anodes . . . Whenever we talk about the first machine, within the next 12 to 24 months, we are really looking to get to that three commercial machines,” he said. “(One) commercial machine can make anywhere between a million to a million-and-a-half square metres (annually) of anode capacity, depending on how much thickness you need of the lithium.”
He estimates the three machines will cost around $30 million.
This year also marked Li-Metal’s first major recurring commercial order for anode materials with a battery developer.
“My short term goal is to get us to that half a gigawatt anode capacity as quickly as we can,” Godavarthy said. “Because at that point . . . the company's profitable and it can sustain itself and invest in whatever is needed to really enhance the technology, enhance product.”
Modular lithium metal production
In June, Li-Metal was awarded more than $1.4 million in grants from the Ontario Vehicle Innovation Network and the Critical Minerals Innovation Fund to develop its lithium metal production technology.
Company figures state the projected demand for lithium metal is to increase by 10 to 12 times the current capacity by 2030 – to 40,000 tonnes annually.
“So our thought process was we had to really facilitate the anode uptake, so that the metal demand can go with it,” Godavarthy said, “and that means driving the cost of the anodes down first.”
The lithium metal facility will also be more capital intensive, as Godavarthy estimates it will cost around $100 million. Li-Metal is not currently raising funds, but might in future consider raising capital to assist in building the anode production machines, then use profits from that operation to aid in funding the lithium metal facility.
Li-Metal has been advancing a modular technology and expects to finalize a key study with its global engineering partner this year. The initial facility, which will itself be modular, may also be in Rochester, but that could change as it scales up.
Godavarthy expressed hope the company will announce partnerships with other battery companies by late 2023. While Li-Metal is theoretically open to partnering anywhere in the world, for now, he stressed, the focus is in western nations.