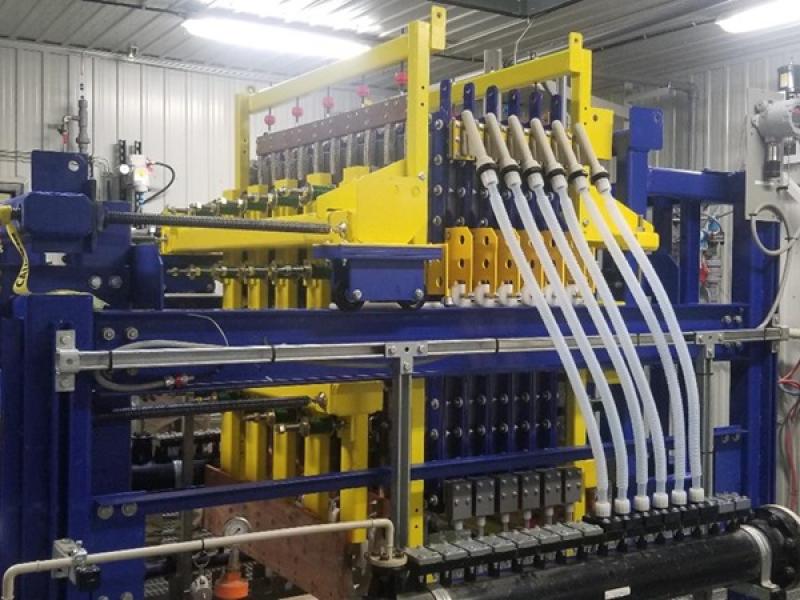
A spinoff of Vancouver-based chemicals company NORAM Engineering and Constructors Ltd. is aiming to utilize electricity to extract battery-grade lithium from brine at commercial scale, bringing a source of the critical mineral closer to home.
NORAM Electrolysis Systems Inc. (NESI) was formed in July 2022 as an offshoot of the electrochemical division of NORAM.
It was created to pursue business in the lithium battery space by converting lithium sulphate or lithium chloride to battery-grade lithium hydroxide, NESI’s president and CEO Jeremy Moulson told Sustainable Biz Canada.
“The rationale splitting NESI off as a separate entity was really around taking advantage of the growth opportunities we were experiencing for the electrolysis sector associated with the lithium-ion battery market,” he said.
To satisfy the amount of investment needed to evolve into a large-scale industrial technology supplier, operating as a separate entity made more sense.
The firm's NORSCAND electrolyzer can also extract lithium hydroxide from used batteries and electronics, or give waste effluents a second life.
With industrial production as its next goal, the company has received $4.5 million from Natural Resources Canada (NRCan) to support the development of the technology at a test facility in Richmond, B.C. as a critical step before commercialization.
From lab experiments to industrial tests
NORAM’s electrochemistry division was led by Clive Brereton, vice president of NORAM. A former chemical engineering professor at University of British Columbia, Brereton, who joined in 1996 after being enticed by NORAM’s potential, led NORAM's electrochemical technology development from laboratory-scale experiments to industrial-level tests.
The company’s work on lithium electrolysis began over a decade ago in its collaboration with Buffalo-based research lab Electrosynthesis. Later it worked with Nemaska Lithium Inc. to develop a technology that converts lithium sulphate into lithium hydroxide.
NORAM partnered with Swedish company Permascand AB in the early 2010s to develop NORSCAND, using a jointly-developed membrane called NORSCAND Cells that split the salts in brine through electrolysis. NORAM is the owner and designer of the cells, while Permascand is the manufacturer.
The electrolyzer takes in brine containing lithium chloride or lithium sulphate and feeds it through a stack of NORSCAND Cells. The cells split the lithium from the chloride or sulphate.
The lithium is then moved to a compartment that splits water using electricity to produce a hydroxide ion and hydrogen gas. The lithium is combined with the hydroxide ion to form lithium hydroxide, which is passed through a crystallizer to form lithium hydroxide monohydrate, an active cathode material for electric vehicle batteries.
A combination of NORSCAND systems at an industrial facility can produce approximately 30,000 tonnes of lithium hydroxide monohydrate per year, Moulson said.
He also touted the sustainability of the technology. It does not produce effluent emissions from the conversion process nor does it require caustic reagents. Lithium refining in China, where most activity is done globally, produces approximately 15 tonnes of carbon dioxide per tonne of lithium because most of the country's energy is from coal. But in the West using cleaner electricity and electrolysis, it produces one-fifth to one-third of the carbon dioxide emissions, Moulson explained.
Another application for the electrolyzer is repurposing effluent streams of sodium sulphate generated from battery recycling into chemicals such as sodium hydroxide or sulphuric acid, or squeezing out lithium sulphate from black mass that can be processed into battery-grade lithium hydroxide.
Testing and commercializing the electrolyzer
NORSCAND was utilized at Nemaska’s demonstration plant in Shawinigan, Que., and is being commissioned or operating at six to eight NORSCAND industrial demonstration plants located primarily in Canada, the U.S. and Europe, Moulson added.
In its Richmond facility, it operates industrial-scale cells on lithium brine that international clients have shipped to the facility to test NESI’s technology.
The NESI division has 50 full-time employees, triple what it had before it was spun out from NORAM, Moulson said. Most of NESI’s expansion has been self-financed by project revenue or with the assistance of NORAM.
Using the NRCan funding, NESI will establish a Lithium Electrolysis Test Centre in Richmond, B.C., where it will build an electrolysis facility to produce industrial quantities of lithium hydroxide from brines sourced from around the world.
“The idea with it is we will take brines from Alberta or South America or Europe or Australia," Moulson said, "and we will do the industrial-scale production of lithium hydroxide monohydrate, to then validate the engineering for the industrial plant.”
NESI’s next steps are establishing its manufacturing supply chains and assembly capabilities to supply NORSCAND Cells to large-scale industrial plants.
It plans to open a 50,000-square-foot electrolyzer assembly facility in Richmond this September, designed to push out enough electrolyzers to produce 100,000 tonnes of lithium hydroxide monohydrate per year, as a step to commercialization.