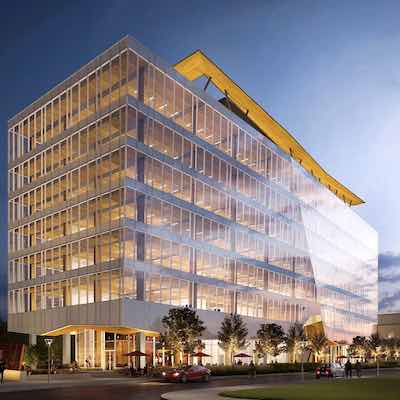
77 Wade in Toronto is an eight-storey office building being constructed using mass timber techniques. (Courtesy 77Wade.com)
Wood buildings can now be constructed up to 12 storeys thanks to changes to Canada’s National Building Code, but the updated regulations come with a catch that can negate one of the most pleasing features of wood construction.
Drywall remains a requirement in many cases, to provide additional fire protection.
“One of the things you’re not able to do is actually benefit from the biophilic qualities associated with living, working and playing in a wood building,” said BNKC Architects principal Jonathan King, “because you’re not actually exposed to the wood at the end of the day, if it’s all covered up.”
Fortunately, though, there is a technique builders can employ to attain the needed fire protection standard, while also showcasing the aesthetic qualities of wood construction. Nail laminated timber (NLT) is a tried-and-true construction method and it’s safer, according to King.
NLT the “simplest form” of mass timber
Nailing standard-dimensioned timber such as 2x6s or 2x8s together is “the simplest form of engineered mass timber system” he said. “This system is evident in many of the historic warehouse spaces on Spadina (Avenue). Look up and you will see these systems.”
It’s a technique being employed at 77 Wade, where King is the lead architect. The project is an eight-storey commercial wood building in Toronto’s Junction neighbourhood.
The building is a hybrid timber, concrete and steel project developed and managed by Next Property Group. It’s being marketed as Toronto’s first NLT office building to reach these heights.
For 77 Wade, NLT is being integrated with other materials to provide “a solution that meets the specific objectives,” King said. “By combining NLT together with concrete, as a composite structural slab system, we achieve the fire resistance rating required, allowing for exposure of wood in the space without the need for drywall.”
For buildings above six storeys, the Building Code considers wrapping of mass timber structures in drywall the preferred method to achieve fire prevention standards. It’s not the only solution, however.
Innovations at 77 Wade
“In designing 77 Wade, we demonstrated an ‘alternate design approach’ which allowed us to meet or exceed the authorities’ requirements and expose up to 78 per cent of the mass timber in the project.”
Innovations in the overall design of the building included sizing the mass timber elements differently, placing sprinkler heads closer together, and the addition of a firefighters’ elevator.
The notion of mass timber “and specifically tallwood is nothing new to our industry,” King said.
He pointed out that until recently, China’s Fogong Temple was the tallest wood structure in the world at just over 200 feet. The temple, which was built in 1056, proves wood “stands the test of time,” he said.
Having said that, fire safety is always top of mind with wood construction.
“The distinction between commercial and residential is that in a commercial building, you need a two-hour fire resistance rating between units,” he said. “So, in our particular solution for our commercial office building, we designed NLT 2×8 assembly to withstand up to two hours of a fire event, so that it would allow the safe exiting of the building by its occupants.”
King’s team designing 77 Wade for “the digital, urban worker” demographic which is seeking loft-style environments. The design focuses on understanding their needs, sustainable practices and quality of life.
To that end, the developers are pursuing both LEED Gold WiredScore Platinum certifications.
Other benefits of wood buildings
Other benefits of employing mass timber in commercial projects is that it can compress construction schedules, deliver a “significantly improved product’ which commands premium leasing rates, and improves sustainability ratings.
One potential downside could be cost, but the gap between mass timber and other contemporary construction techniques is shrinking, King said.
“Currently, there’s probably a premium associated with the use of wood, structurally, in the building,” said King. “The market is reacting, stepping up to provide solutions where that cost is beginning to come down.”
More fabrication facilities are being created to take advantage of the increase in mass timber construction.
“Obviously, the Canadian market is rich in resource,” King said. “So it’s about harnessing those resources to create the opportunity for that fabrication in various factory settings.”
Mass timber is already a “far more mature industry” in Europe, where King said it is considered a viable alternative to concrete or steel.
In B.C., which adopted the new building code standards in 2019, a groundbreaking ceremony took place last fall for a 12-storey wood residential and commercial building called Tallwood 1 in Langford, B.C.
It’s the inaugural Canadian project under the new standards.