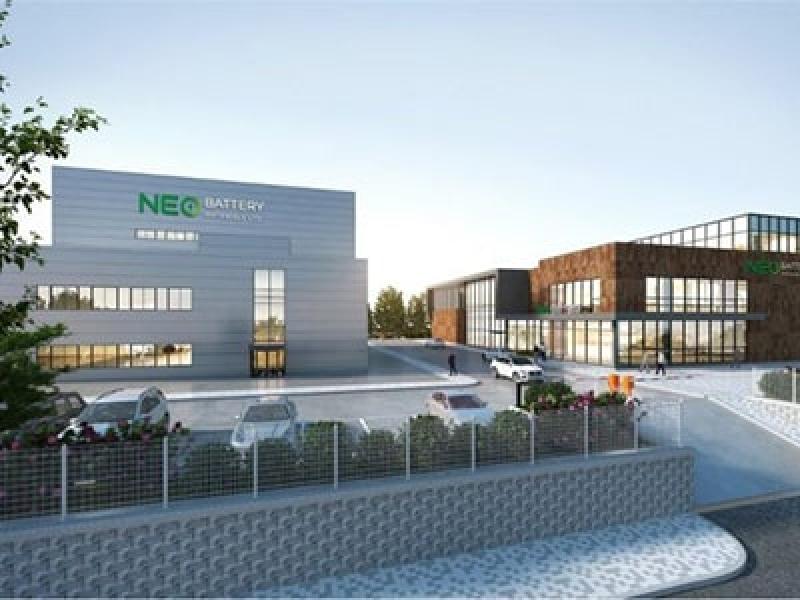
Vancouver-based silicon anode supplier NEO Battery Materials Ltd. has kept busy recently with a corporate move to Ontario, launching a U.S. subsidiary and planning a new South Korean commercial plant.
NEO (NBM-X) uses a proprietary nano-coating process to integrate silicon with graphite – the most common material for battery anodes. Anodes are one of two electrodes which comprise parts of a battery.
The company was founded in 2021 after CEO and president Spencer Huh took over a mining business that had been operating for over a decade.
“We are the only company in Canada that is solely focusing on silicon anode materials for lithium-ion batteries,” Danny Huh, NEO’s corporate development manager told SustainableBiz. “So currently, we're targeting the EV (electric vehicle) market specifically, but our materials can be also applicable to electronic devices as well.
“Our ultimate mission is to achieve the thousand-mile battery of electric vehicles using our silicon anode materials.”
NEO’s proprietary process
Graphite, when used in an anode, comprises around 28 to 30 per cent of a battery. This leads to a number of problems for the typical EV battery.
“Their slow charging time, obviously. We know that Tesla Model 3s, they charge for about 36 hours in your garage and that’s a problem. And also the limited battery run time, which translates into that anxiety factor for (the) consumer, is probably one of the main factors that are limiting the mass adoption of electric vehicles today,” Danny Huh explained.
“So there's actually a capital solution to resolving the problem with graphite, and this is integrating silicon into the graphite as well.”
However, regular silicon expands rapidly when inserted into the anode material, and unprocessed silicon breaks down after only 100 cycles. NEO’s nano coating solves both of these problems. According to a company presentation, it reduces costs while enabling ultra-fast charging and nine to 10 times more capacity – thanks to an input called metallurgical-grade silicon.
The company currently offers three anode products known as NBMSiDE. For now, it manufactures samples on a per request basis.
“So one of our largest testing parties in Europe, they've commented that just using five per cent of our materials is the same as using 10 per cent of the competitor’s material,” he said.
Spencer Huh noted the company has approximately 50 NDAs within the battery industry, including global battery manufacturers, electric vehicle automakers, chemical material companies and a U.S.-based investment bank.
Ontario redomicile and NEO America subsidiary
At the end of February, NEO announced it would begin to shift its corporate office to Ontario from Vancouver, as well as formally changing its focus from a mining issuer to a technology issuer.
The company also has an R&D facility and a pilot plant in South Korea. NEO plans to replicate both in Ontario within one to three years, likely via a joint venture.
NEO sees Ontario as a hub for growth across North America, with Spencer Huh singling out LG Energy Solutions and Volkswagen’s plans for battery plants in the province.
“We do see great opportunity to us because they will need silicon on those materials to improve their battery quality. So we do see great opportunity because there is no other company to develop silicon materials like us in Canada,” Spencer Huh said.
In March, NEO launched NEO Battery Materials America LLC as a private subsidiary after announcing the venture in January. It is incorporated in Delaware but the company is looking at Ohio as its top pick for headquarters. It also intends to establish a U.S. commercial plant.
“We already got contacted by some venture capital funds in the U.S.,” Spencer Huh said. “So because we do think we have a differentiation on our silicon anode materials, we will do better in (the) recycling business in the U.S., especially in Ohio.”
In the U.S., testing is planned with nickel-manganese-cobalt and lithium-iron-phosphate cathodes, both standard in lithium-ion batteries.
Silicon anode growth and NEO’s future
NEO cites QY Research in a company presentation showing the market for silicon anodes will grow from approximately $550 million in 2020 to around $20.6 billion by 2030. By 2028, annual global production is predicted to reach 170,000 tonnes.
Its new commercial plant is aiming to produce 240 tonnes annually, and is planned to operate 24/7. Its final capacity is predicted to be 2,000 tonnes, which the company states will serve 1.3 million EVs annually. Permits were approved in January and the company plans to hire around 20 people to run it.
NEO is also looking into incorporating battery recycling into its business. Danny Huh mentioned “securing” lithium-ion battery recycling experts in South Korea to help NEO enable the technology.
One such development is a memorandum of understanding NEO signed with a South Korean company that has the potential to recycle silicon waste from semiconductor and solar cell companies and transform it into a low-cost silicon, which could reduce NEO’s input costs by 40 per cent.
Spencer Huh once again used Ohio as an example for how this would work.
“The land (in Ohio) is so cheap, compared to Ontario,” he said. “That’s why we could find big land to accommodate that silicon anode material plant, plus battery recycling at the site as well.”
The company recently appointed Dr. S. G. Kim as its chief technology officer to aid in its commercialization. He previously served as the executive vice president and head of R&D of Hanwha Solutions’ advanced materials division, a South Korean chemical manufacturing conglomerate.
“Right now, silicon can only be put into the anode material (at) just five to 10 per cent. But what the industry wants is 100 per cent. This is one of the R&D directions that we will be developing through that five- to 10-year period,” Danny Huh said. “The whole globe wants to transition into electric vehicles, but right now, graphite supply is really taking a big (hit) to that, and graphite is probably the biggest bottleneck compared to lithium.”
EDITOR'S NOTE: Information about the production capacity of NEO's facilities was updated after this article was published to reflect new information provided by NEO.