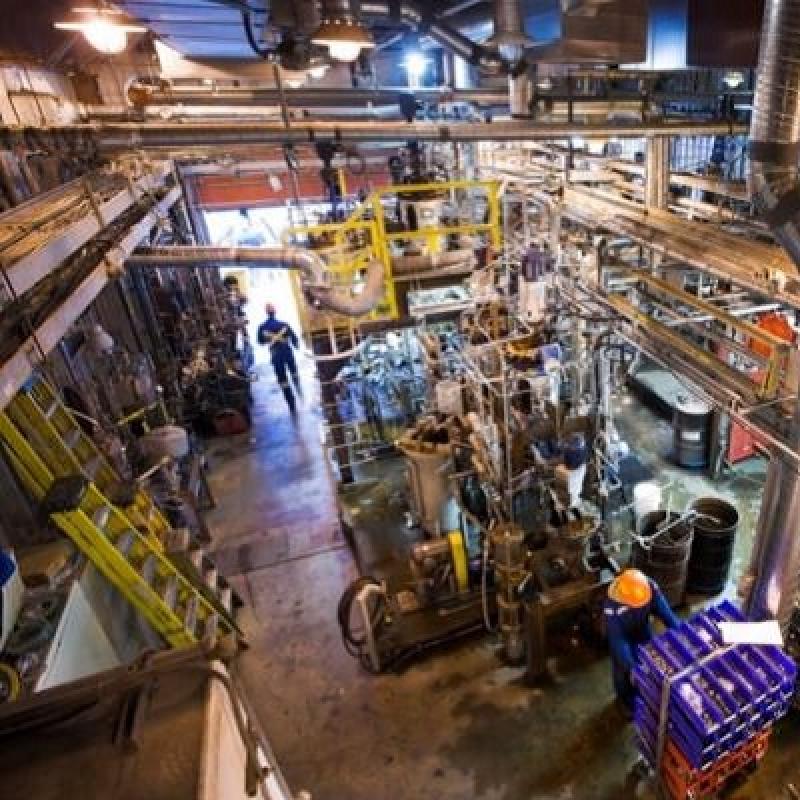
Calgary-based CVW CleanTech Inc. (CVW-X) has developed a process to clean up the tailings from the oil sands industry and unlock their critical minerals, which could put a notable dent in their environmental impact.
The CVW team is behind a solution – developed over the course of 15 years – to solve the problems created when oil sands mine tailings are disposed of in large manufactured lakes. The disposal not only pollutes the local environment, it wastes resources that could be repurposed and emits methane, a powerful greenhouse gas.
CVW, formerly known as Titanium Corp., was looking to remove critical minerals from the tailings. Talks with oil sands operators revealed the tailings would first have to be cleansed of hydrocarbons before the critical minerals could be extracted.
CTO and executive vice president Kevin Moran, a former researcher at Syncrude Canada, developed a means of cleaning the hydrocarbons from the tailings before recovering the critical minerals.
“You need to utilize technology and innovation to lower the carbon impact of that oil production and its eventual uses,” CVW CEO Akshay Dubey said, as hydrocarbons will remain a critical component of the global energy mix and economy.
“Some folks may call it greenwashing, but our technology reduces Canada’s emissions by half a per cent . . . We do think we are an environmental solution as the world goes through a transition.”
CVW’s solution for froth treatment tailings
Recovering and processing oil sands bitumen to refine synthetic crude oil creates a waste byproduct called froth treatment tailings. A typical destination is a tailings pond, potentially polluting the local environment and emitting methane from the solvent.
CVW takes the froth treatment tailings and filters them through a concentrator located near an oil-sands mining froth treatment plant, where they are subject to solvent extraction and distillation to extract the hydrocarbons.
Over 85 per cent of the bitumen and over 90 per cent of the solvent is recovered, which means per site, CVW’s technology can produce approximately two million barrels of oil and 300,000 barrels of solvent per year.
The majority of fugitive emissions from tailings ponds are eliminated with CVW, Dubey said. A company estimate claims it can abate between 380,000 tonnes to 850,000 tonnes of carbon dioxide equivalent emissions per site, reducing site-wide oil sands emissions by five to 12 per cent.
If used on six oil sands operations, this could mean eliminating three megatonnes of carbon dioxide equivalent emissions per year — approximately 0.5 per cent of Canada’s annual national emissions, according to Dubey.
Critical minerals extraction
Once the tailings are cleaned, they can be put through a mineral separation plant to filter for titanium and zircon concentrates.
Titanium can be refined into a metal or used as an ingredient in paint pigments. Zircon has applications for ceramic tiles or can be turned into zirconium for use in nuclear power.
CVW is exploring also extracting rare earth minerals, which can be used to make batteries, electronics and clean energy generation equipment like wind turbines.
The processed tailings can be disposed of and remediated through a thickening, while the recovered hot water can be recycled for use in oil sands operations, such as through heat recovery.
The oil sands operator can generate revenue from the recovery of hydrocarbons and critical minerals, as well as carbon tax avoidance and operating cost efficiencies.
A company report estimates annual revenues from the application of a hydrocarbon-focused project to be approximately $248 million per site and $446 million for a facility that also produces critical minerals.
Steps to commercialization
CVW has received over $80 million in grants from the federal and provincial governments for research and development and has spent over $100 million developing its technology.
Dubey said CVW is in a “fairly strong” position on cash and liquidity (its Q2 financial results showed $6.6 million in cash on hand), and is not expecting to raise more capital until it has a project to build.
Its technology was piloted at CanmetENERGY in Devon, Alta. from 2010 to 2014, where Syncrude, Suncor and Canadian Natural sent their feedstock for testing and worked with CVW to review the data. Engineering firms such as Stantec and government agencies such as Emissions Reduction Alberta and Sustainable Development Technology verified the results.
CVW is on the “precipice of commercialization,” Dubey continued, which would involve signing a deal with an oil sands operator for a site, raising financing and completing the engineering and construction for the concentrator and minerals separation plant.
The company is focused on talks with potential oil sands partners for what a commercialized project would look like, with a deal ideally reached in the next 12 months. CVW would then enter into a construction period to build a facility.
Dubey would like to see CVW lead as a cleantech company by partnering with other innovators in the space to support them as they look to bring other technologies to market.