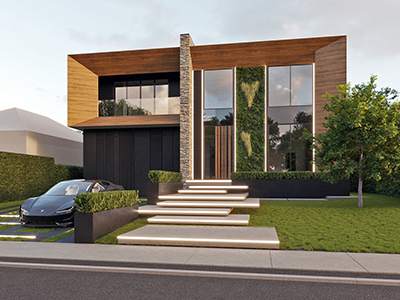
A rendering of the exterior of 241 Waterloo Ave., to be completed by Daylun later this year. (Courtesy Daylun)
Pre-fabricated housing company Daylun will soon begin construction of a net-zero, pre-engineered “concept” home at 241 Waterloo Ave. in Toronto.
Daylun is proposing to target a LEED (Leadership in Energy and Environmental Design) Platinum certification, the highest level of recognition for sustainable design, construction and operation. The project will begin construction this summer and is expected to finish sometime in the fourth quarter of this year.
Before launching Daylun in 2021, founder and CEO Arthur Zankowicz spent time in the sporting goods sector, the fashion industry and served as art director and production designer for over 300 commercials.
“My building background is not in engineering or architecture, it is in filmmaking, and I was an art director and production designer,” Zankowicz said.
“One of the things I had to do is build a nightclub in the middle of the forest overnight. I gained my chops there and I learned how to build quickly.”
The walls of the house will be constructed of a combination of oriented strand boards — panels made by compressing and gluing pieces of wood together – a steel structure that can be snapped together and closed spray foam on the outside.
While the production of materials and shipping can take three months, Zankowicz explained the actual construction can be completed within 14 days.
241 Waterloo Ave.
Daylun will utilize a number of other patent-pending technologies in the construction of 241 Waterloo Ave. This includes a board made of ethylene-vinyl acetate (EVA), as well as solar-heated exterior cladding that is described as a cost-effective, passive heat-gain system.
The EVA can be used as a backer board or drywall in house construction. According to Zankowicz, it is 60 per cent lighter than drywall, but strong enough to hold a wall-mounted air conditioner. It is also mold-resistant, fire-resistant up to 1.5 hours and biodegradable.
The process also incorporates a vegetable-based adhesive that reduces human and environmental toxicity. During his time in fashion and sporting goods, Zankowicz came up with the idea after noticing his feet sticking to a dirty floor in a bar.
The patent was initially developed in 2016 under his other company, 50 Unlimited Co. Technologies, which he said “is still going strong.”
“It works for shoes, and it works great for construction,” Zankowicz explained. “It’s completely organic. There’s a little bit of additive to get it going but there’s no smell and it’s 100 per cent vegetable.”
He personally holds the patents, so they can be used for Daylun regardless of whether or not they were originally developed for fashion.
Daylun and Zankowicz chose LEED certification for 241 Waterloo because of its stature within the industry and its recognizable brand.
“Everybody who’s involved, from the financiers, to the insurance company, to the city, if they know you’re building LEED… it helps with a lot of parts, including building a flagship house and trying to establish yourself,” Zankowicz said.
A host of other companies are lending their technologies and expertise to the home. This includes:
– DMX, a water membrane manufacturer for foundation and green roofing applications;
– Green Friendly Paint, a sustainable multi-application paint manufacturer;
– Milwaukee Tools, a power tool manufacturer for electrical, mechanical and plumbing applications;
– Green-tek, a manufacturer of HVAC systems that support enhanced indoor air quality;
– Terra Design, an interior design firm specializing in biophilic design; and
– LaFarge’s ECOpact low-carbon concrete, distributed by Innocon.
Zankowicz got the companies on board by pitching 241 Waterloo as a concept house for sustainability.
“I find that we’re right at the apex where a lot of companies want to get involved,” Zankowicz explained. “So by explaining to these companies this is what I’m doing and we’re trying to hit net-zero, we’re trying to be the most sustainable . . . it’s almost like a concept car, right? It’s a concept house.”
He highlighted Lafarge’s low-carbon concrete as an “easy sell” to use in the home given the material. The ECOpact concrete line reduces carbon emissions from making the product by 30 to 100 per cent compared to standard Portland cement.
The future of Daylun
Zankowicz plans to film the manufacturing and construction of 241 Waterloo as a 30-minute documentary.
“There’s a lot of people that were starving for this kind of show,” Zankowicz said. “Whether it be on HGTV or Netflix or online, we’ll get it out there.”
From 2002 to 2009, he launched and ran the sporting goods company Moreno which he explained was purchased by a promotional company to absorb the sales and designs. At that point he left Toronto for China and began to develop what would become Daylun.
He initially planned to launch Daylun and the concept house in 2023 or 2024, but after returning home for Christmas in 2019 and being locked down shortly afterward, the company grew at a much faster rate than anticipated.
While the materials are manufactured in China, he said there are plans to build another factory somewhere in the Caribbean within a year. In 2023, he hopes to build on the momentum gained from the completion of the documentary and the concept house.
“We have some ideas, we have some places that we want to build and we’ll be talking to builders and developers who want to use our product,” Zankowicz said. “But I think the medium density, the townhomes to high density is where this product will really excel.”