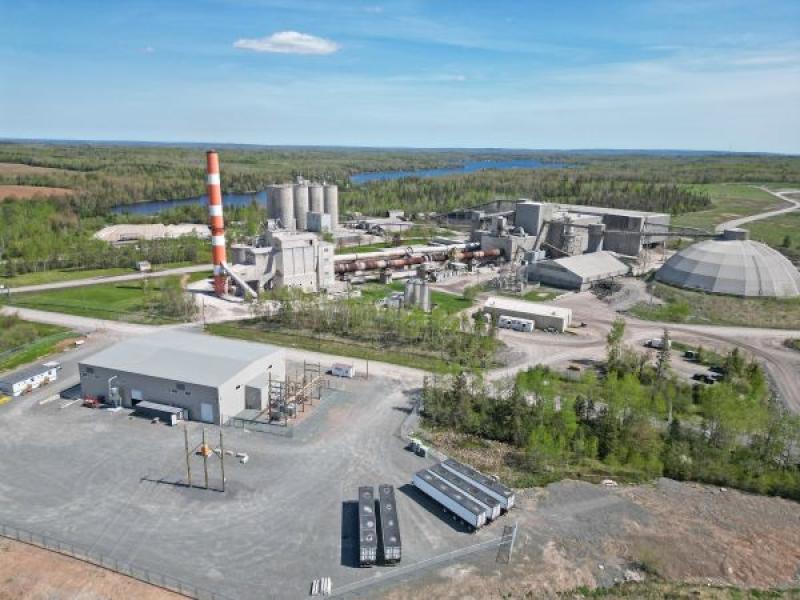
Geocycle has opened a facility that turns non-recyclable waste into a low-carbon fuel, which then powers a nearby Lafarge cement plant, a first for Geocycle in Canada.
Plastic and asphalt shingles are taken from nearby landfills and sent to Geocycle's Brookfield, N.S., facility, where the waste is shredded to a minuscule crumb. After further processing, it is transformed into a fuel that has up to 100 per cent less carbon intensity than coal, the fossil fuel that previously powered the cement factory.
Lafarge's relationship with Switzerland-based Geocycle's Canadian branch means the “cement plant staff of Lafarge Canada" can "focus on making cement and not having to manage all those contracts with different suppliers of byproducts and non-recyclable materials that can be reused as fuel,” Rob Cumming, Lafarge’s head of sustainability in Eastern Canada, told Sustainable Biz Canada in an interview.
“They’re kind of the bridge between the byproduct supply and cement plant,” he said about Geocycle.
Lafarge is a large global cement producer, and like Geocycle, is a subsidiary of Holcim Group. Lafarge and Geocycle have partnered for at least 20 years on every Canadian Lafarge cement facility where waste materials can be given a second purpose, Cumming said.
Turning garbage into valuable energy
Small by North American standards but representing the only cement plant in Atlantic Canada, the Brookfield site produces around 200,000 tonnes of Portland cement per year to service the region, Cumming explained.
At the Geocycle site across the street of the Lafarge factory, the waste materials are broken down and blended, then lingering metals are removed with magnets. Once a chemical analysis verifies the fuel is sufficient for use, it is trucked over to its Lafarge neighbour. The result is a fuel that has lower carbon emissions by virtue of offsetting the need to extract more fossil fuels.
Such a process took years of testing to refine. A series of emission testing programs were conducted alongside the Nova Scotia Department of Environment and Climate Change and Dalhousie University to ensure the fuel would perform up to standards for environmental and material handling needs, Cumming said.
At full production, it will divert 14,000 tonnes of waste per year, which results in reducing emissions by 12,000 tonnes of carbon dioxide (CO2) per year, according to Lafarge. Such a cut is about a 25 per cent to 40 per cent reduction compared to using fossil fuels, Cumming said. Over a third of the emissions from the Brookfield plant come from fuel consumption, he added.
The Geocycle facility has technology that captures solid particles and ash from burning the fuel, which means the combustion emissions are about as clean or better than using fossil fuels, he said.
Local construction and demolition waste materials are planned to be used to make fuel. “It’s all part of trying to minimize our consumption of virgin materials,” Cumming said. He expects it to take a few years until the Brookfield site is ready for such a transition.
The Geocycle facility cost over $10 million. Approximately a third came from the federal government's Energy Innovation Program, while the remainder was funded by Lafarge.
Commissioning started in June and production began in late September. Lafarge anticipates full production in 2025.
Lafarge’s other carbon reduction endeavours
The company has been making an effort to shrink its carbon emissions, as cement and concrete are responsible for up to nine per cent of global greenhouse gas emissions.
In Canada, Lafarge partnered with Geocycle on a pilot project in Quebec to recycle demolition waste into cement and to produce ECOPlanet low-carbon cement in Richmond, B.C.
In Bath, Ont., Lafarge launched a trial with Ottawa-based Hyperion Global Energy Corp. to capture the carbon from its operations and reuse the greenhouse gas to make ECOPact low-carbon concrete.
More facilities in the style of Brookfield project will be sprouting across Canada, Cumming said. The company announced the commissioning of a Geocycle low-carbon fuel facility at its Exshaw cement plant in Alberta. The $38-million facility will cut up to 50 per cent of the natural gas consumption for one of its kilns by using construction waste such as wood.
As for Lafarge Canada, the company has committed to Holcim's climate targets. By 2030, Holcim aims to cut its Scope 1 and 2 emissions by 26.2 per cent per of cementitious materials; by 2050, achieving net-zero across its value chain.
"We know we have to deliver solutions for our customers, for our people and communities. We can't be asking an individual at home to be solving this problem. It's our responsibility as an industry to find solutions that deliver those building materials that we so essentially need," Cumming said.
Steps to achieve this include:
- transitioning to producing only Portland limestone cement in Canada, which manages up to a 10 per cent reduction in CO2 compared to Portland cement;
- using only alternative fuels in its Canadian facilities by the end of 2023;
- switching asphalt production to warm mix where possible, which cuts CO2 by approximately 10 per cent;
- signing power purchase agreements; and
- installing electric vehicle chargers for its employees and customers.