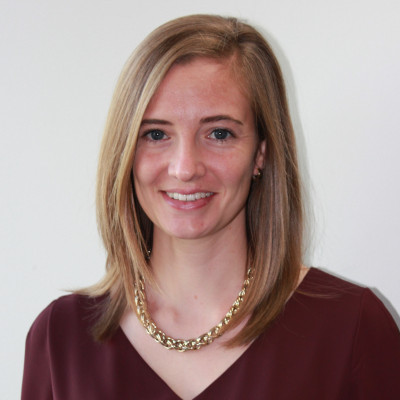
Sarah Bingham is director of development and sustainability at Adera Developments in Vancouver (Courtesy Adera Developments).
Canada’s construction industry plays a significant role in the economy, generating $156 billion in GDP in February of this year. In tandem with revenue generation, the industry produces one-third of the total solid waste in Canada, which equates to over 4 million tonnes of waste per year, according to a circular economy report by Delphi Group and SCIUS Advisory.
The findings conveyed that much of the value from these waste materials and resources is being lost from the economy at end of life. In order to minimize the waste produced from a project, development and construction teams must seek out innovative solutions to better improve and streamline output.
Today, we have the benefit of utilizing high-technology like that of building information modelling (BIM) and prefabrication to improve coordination and speed for a more efficient construction process.
A coordinated result
Over the last five years, BIM software has become more prevalent in the industry. Prior to its emergence, we relied heavily on our consultants layering 2D plans over each other to ensure coordination. Using BIM, they can now create 3D models of the pertinent building information we need; this has been a significant move forward for cross-departmental teams.
Structural and mechanical consultants may not have considered where beams and venting clashed, and this technology has since resolved a lot of the issues that were previously dealt with on-site. BIM uses advances in technology to coordinate plans that we have always used in construction, allowing us to resolve issues before we get to a site.
At Adera Development, we brought a BIM consultant on board with one of our first cross-laminated timber (CLT) buildings during the design stage; it allowed for better coordination of our structural and plumbing components, and to map out electrical and mechanical rooms. The use of BIM early in the development process allows teams to become more coordinated. It means issues can be discovered at the design stage before they become issues on site. When we are then on-site, construction can be accomplished in a more timely manner, without avoidable delays.
Waste reduction
The coordination that BIM brings forward leads to less waste by resolving issues before materials land at a worksite. Trades teams also take value from BIM; it assists with calculating material required, which further reduces waste and increases efficiency. Prefabrication is another method for minimizing waste in the development process, which sees building components or whole buildings assembled before arrival on a worksite.
There are many types of prefabrication developers can explore. Oftentimes, projects will prefabricate walls or trusses, or more futuristically, the entire envelope of a building or modules in line with a shipping container concept. CLT is another type of prefabrication that can be used as an alternative to concrete to form roofs, floors, and walls of new buildings.
If using CLT for prefabrication, panels are manufactured to the exact size using BIM, which converts to less wasted material through offcuts as the computer programs maximize the product’s efficiency. CLT panels can be quickly lifted into place on-site, with a smaller crew than traditional wood-frame construction, resulting in faster and more efficient construction.
Prefabrication is currently growing in popularity in B.C.’s North Vancouver. The contemporary- meets-industrial 1 Lonsdale Avenue Commercial Building is an example of CLT efficiency in action: it was erected in 10 days. It is a testament to the sustainable alternative wood-building brings over other types of construction. The speedy turnaround time for this mode of building resulted in a lower carbon footprint with fewer trucks required.
Almost two years ago, our team completed one of the largest mass timber residential projects in Western Canada in the same area with Crest – a development that saw homes sell out and interest in sustainable structures pique.
Barriers to implementation
When we look at the factors that might hold a builder or developer back from implementing BIM technology and, in turn, utilizing high-tech management systems to increase efficiency, time and finance are the first to come up.
The software could be considered as an extension of your consultant team. There is a cost and time investment involved with this type of coordination. BIM involves an upfront cost, but continuing a more intricate building process without it could result in a higher spend in the long run. Using BIM also limits human error and allows for mistakes to easily be corrected before building.
Having a dedicated member of your team in-house who specializes in building information modelling could be a valuable asset for large companies working on multiple complex buildings.
While the development sector evolves, Adera Development is dedicated to being at the forefront of sustainability and building practices. Technology is always more difficult to use the first time, but developers must keep up with the pace of a changing industry and see the value of high technologies for the future.