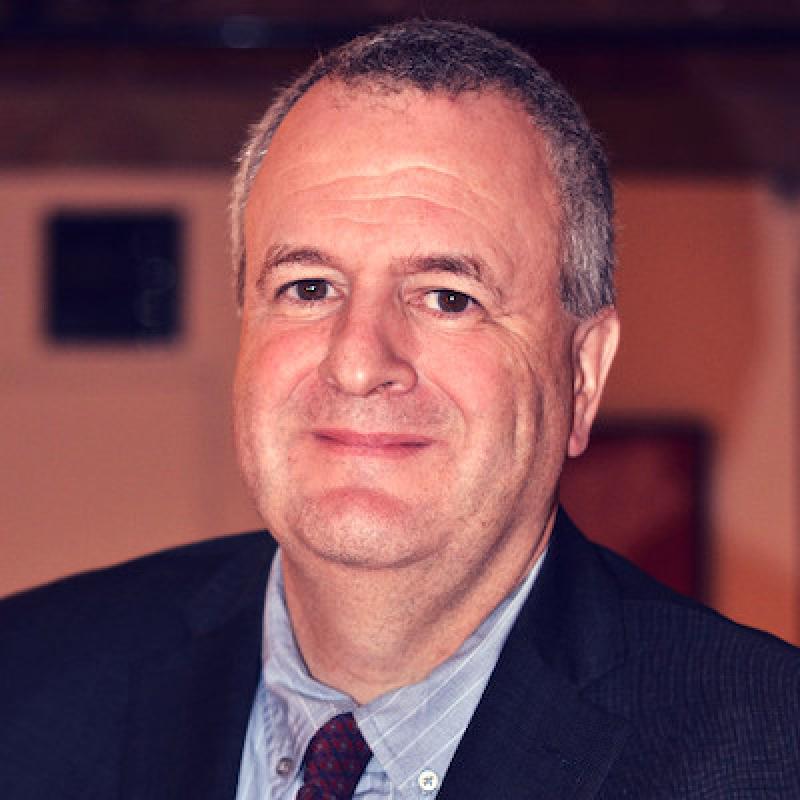
HPQ Silicon Inc. has announced its wholly owned subsidiary, HPQ Silica Polvere Inc., has developed a pioneering Fumed Silica Reactor (FSR) technology to convert quartz into fumed silica using a minimum of 86 per cent less energy than existing industry processes.
The FSR method of silica production is also expected to cut related carbon emissions by 50 to 60 per cent, the firm claims.
In late May, the company released the results of a critical study that confirms the potential of the breakthrough technology, which it believes could bring about a quantum leap in the way fumed silica is produced.
"This is a massive technological leap. We're replacing a known process that has been used for a hundred years with a completely new one. Now we're in the process of validating our initial results," Bernard Tourillon, president and CEO of HPQ Silicon and HPQ Silica Polvere, told SustainableBiz.
Fumed silica has a vast number of industrial applications. It is a key ingredient in the manufacture of paints and coatings, adhesives and sealants, silicone rubbers, pharmaceutical products, cosmetics, battery gels and unsaturated polyester resins, to name a few.
Currently, fumed silica is produced from silicon metal via an energy-intensive process requiring the use of hazardous materials and generating hydrogen chloride gas (HCL) as a by-product.
HPQ's fumed silica reactor is being developed in collaboration with technology supplier PyroGenesis Canada Inc. It employs new plasma technology that directly transforms quartz into silica as opposed to the conventional, highly polluting process that, first, converts quartz into silicon metal.
A new era in the silicon industry
This innovation could potentially reduce direct carbon dioxide emissions associated with fumed silica production by as much as 60 per cent, equivalent to a reduction of approximately five tonnes of carbon dioxide (CO2) per tonne of fumed silica.
"The Fumed Silica Reactor developed by HPQ Silica Polvere Inc. (in collaboration with its technology provider PyroGenesis Canada Inc.), perfectly embodies (our) commitment to green engineering processes. We are dedicated to developing innovative processes that minimize the environmental footprint while meeting the material demands of the industry," Tourillon said.
"(Moreover), the direct CO2 emissions reductions achieved by the reactor . . . does not encompass the additional (and) substantial indirect environmental benefits."
HPQ Silicon is an advanced materials engineering provider that offers sustainable silica (Si02) and silicon solutions. Headquartered in Montreal, the company is developing a range of value-added silicon products for the battery industry, the electric vehicle sector, and many other industries using silica and silicon metal in their manufacturing processes and products.
Silicon is a semi-conductive material and the second-most abundant element in the earth’s crust after oxygen. Like other energy metals, including lithium, graphite, cobalt and nickel, silicon does not exist naturally in its pure state, which requires it to be extracted via complex processes.
Decarbonizing the silicon industry
HPQ Polvere's technology carries significant implications for the decarbonization of the silicon manufacturing sector and lowering the carbon footprints of hundreds of commercial products containing silica or silicon.
Companies currently producing fumed silica via the standard carbothermic process could soon consider adopting HPQ's fumed silica production technology.
According to Tourillon, his company's proprietary FSR tech will, for the first time, enable the large-scale production of commercial-grade fumed silica "with greatly reduced carbon footprints relative to today’s commercially available technologies."
Today in Canada, approximately 24,000 tonnes of fumed silica are consumed annually. The adoption of the HPQ Silica Polvere process would result in a reduction of 120,000 tonnes per year in CO2 emissions.
HPQ is ramping up operations in wake of tech findings
HPQ began developing its FSR technology with funding from the Quebec government that has allowed the company to prove the process actually delivers on its theoretical promise.
"We're basically using the power of plasma to replace what was previously done by the same chemical process that has been used for nearly a century," Tourillon explained. "Some work in this new field had been done before at McGill University and other places, and there was a great opportunity for us to carry it forward.
"We were anxious to see how close we could get to making fumed silica using this streamlined method."
HPQ began tests in 2021 and was pleasantly surprised with the energy consumption and emissions reductions.
"As soon as we proved that the FSR process works, we knew we had a project that could replace the conventional chemical process. I'm very happy about the results . . . I never imagined that the CO2 emissions reduction would be so massive," Tourillon said. "However, I was sure that the production process was going to be much cheaper because . . . we're talking about massive cost saving in the production of silica and silicon.
"We're about taking quartz, which costs approximately $500 per tonne, and using it to produce industrial-grade silicon that is selling at $6,000 per tonne. So it's like a no-brainer with respect to the profit margin."
As the company works to validate the initial results, it is also preparing to bring a second pilot project in Montreal into production.
"That's why we've signed NDAs with companies interested in our work, because really they want to see whether we can produce the silica on an industrial scale level."
Expanding, transforming the fumed silica market
"The way I see the fumed silica market, it's going to take as many as 10 big companies entering this space because you can't be a small player in fumed silica. With respect to the traditional production process, you're talking about a cap-ex of half-a-billion to a billion dollars, and you're dealing with a very dangerous chemical, HCL. Plus the cost of handling that waste residue is massive."
Tourillon has outlined ambitious goals for his company that he hopes will take the silicon industry to the next level and oblige it to transition to FSR technology.
"Our goal, and I'm simplifying in this regard, is to match our new FSR technology with what the bigger players are doing using the old carbothermic technology. Microsoft didn't develop ChatGPT, but they were quick to buy (into) it. Microsoft and Google were completely surprised by the concept of AI, but are now heavily invested in that tech.
"But I think our fumed silica process is going to have a major impact. There are so many big players in the silicon industry in the U.S. and Europe which have a massive carbon footprint, that there will be tremendous pressure on them to reduce their CO2 emissions.
"The dirty little secret that is not generally publicly known is that silicon metal as an industrial feedstock is the highest CO2 generator there is."
HPQ's next steps and production timeline
Tourillon said once the second pilot plant is operating, it will take up to a year to "crunch the financial numbers" before constructing a full-scale production facility. Such a facility is expected to involve up to $40 million in investment before it can start generating cash flow, "but we'll be producing silica at a fraction of the cost of all of the traditional process."
If all the initial promise is proven out, he expects significant interest from end-users as well as established fumed silica producers.
"I think there's going to be an off-take agreement along the way, although it's clear that we have to show that there are going to be substantial potential revenues," Tourillon said. "I am skeptical personally that we will get all the way to where we're producing silica on an industrial level ourselves, because once we prove it works, there'll be a major producer that says, 'okay, we want to have this technology exclusively'."
In the meantime, HPQ is also developing a parallel technology, the Quartz Reduction Reactor (QRR), pioneering a new and clean method of producing silicon metal.
"Our QRR system is an enclosed process of producing silicon as opposed to the open smelter process that is used throughout the silicon metal industry. But our process is a massive improvement in that we don't release CO2 in the atmosphere.
"We have built a small, scalable modular system which enables us to go and attack the niche market by producing higher purity silicon that is required in the battery sector. And QRR technology can deliver a higher purity material than anybody else and do so in one step."