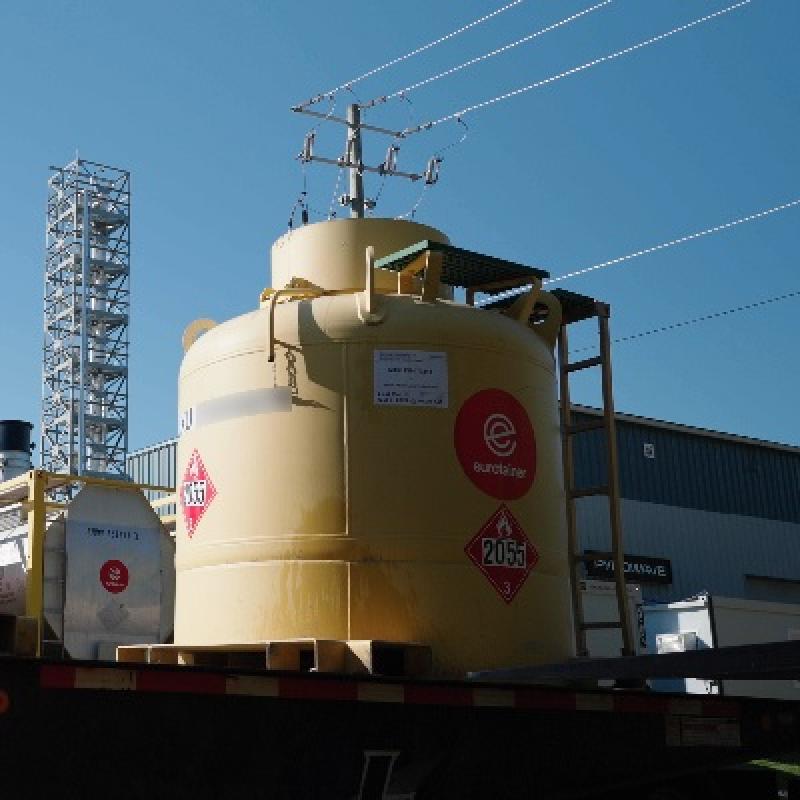
A container of styrene recycled by Pyrowave's microwave technology is headed for a Michelin tire plant in France to produce tires. (Courtesy Pyrowave)
Pyrowave, a Montreal-headquartered firm, is looking to make its mark in the plastics recycling industry with its use of energy efficient, electric microwaves to produce an almost pure, traceable plastic polymer that broadens the recycling market.
Founded and led by CEO Jocelyn Doucet, the company spent a decade of “intense R&D and investments” to bring its technology to scale.
It transforms polystyrene waste, like Styrofoam, into its root chemical called a monomer. The monomer can then be recycled into an end product.
The company offers an alternative to mechanical recycling that faces the challenge of non-removeable additives like pigments and fillers, limiting their market. Pyrowave’s microwave technology resets the plastic to its original shape and removes additives to output something “that has identical application as the virgin material,” Doucet said.
“Now you really fully reset the clock of the polymer.”
Doucet hopes to deliver environmentally-friendly recycling that runs on clean electricity, thus reducing oil consumption and greenhouse gas (GHG) emissions, and supports the circular economy.
The Pyrowave process
Recycling begins in the liquification tank, where plastic waste is liquefied to remove contaminants like labels and additives. The liquid plastic waste is transferred to a reactor, where microwaves reach around 300C to break up polystyrene chains and release the styrene monomer.
The liquid monomer is purified in a distillation column to reach 99.8 per cent purity, compared to 50 to 60 per cent purity from other methods.
Unlike other recycling methods, Pyrowave stands out for its use of electricity, said Doucet.
“Being able to use electrical energy to break up the polymer chain, it’s more energy efficient and you have a lower carbon footprint, because you’re using eventually renewable energy instead of burning something . . . That’s why we’re really focused on electrification of the chemical industry.”
Before it installs its recycling system, Pyrowave conducts a sensitivity analysis to determine the impact from the electricity grid. The cleaner the grid in a particular area, the cleaner the recycling process will be. Doucet claims Pyrowave’s recycling process can significantly reduce GHG emissions in countries with clean grids, like Canada or France.
Producing one kilogram of styrene monomer with Pyrowave’s electric technology slashes GHG emissions by 40 to 45 per cent, compared to producing one kilogram of virgin styrene monomer from fossil fuels.
Even regions without the cleanest grids still benefit, as the microwave technology is energy efficient and only needs to reach about half the temperature required for typical pyrolysis.
Pyrowave is competitive and cost-effective for virgin styrene manufacturing, Doucet said, and decouples the manufacturer from fluctuating crude oil prices.
Traceable plastics for a circular economy
Another benefit to Pyrowave is that it produces traceable plastic.
This assures consumers the plastic they buy has the quantity of recycled plastic material promised on the label, Doucet said. It provides more assurance than certificates or corporate claims, he said, which closes the opportunity for greenwashing.
“We’re able to track systematically every drop of styrene monomer and physically count it into the final product. And this is really the breakthrough we bring to the table. We’re able to demonstrate that with the proper technology, you’re able to do physically segregated, traceable recycled content.
“So at the end of the day when the consumer buys product with our styrene monomer, they know 100 per cent of the molecules are actually physically in the product. It’s not just an allocation or an accounting scheme.”
Doucet said the technology can increase recycling rates for plastic that would have been otherwise incinerated or left to decompose in landfills. He pointed to a seven to 10 per cent recycling rate as a problem of markets, not technology.
Plastic waste imbued with additives offers limited recycling options such as being used for car parts. Pyrowave's process produces near virgin-quality product, opening up the market, creating more demand and reducing water and energy consumption.
The Michelin partnership
Pyrowave partnered with French tire giant Michelin to produce approximately 1,000 passenger car tires with three tons of recycled styrene.
Doucet said Michelin chose Pyrowave because of the traceability of the plastic waste, aiding Michelin’s commitment to using 40 per cent recycled material by 2030.
It is the result of a partnership forged in 2020 when Michelin invested an undisclosed sum into Pyrowave.
Pyrowave “industrialized” its operation with Michelin, Doucet said, licensing the process to the tire maker.
Doucet said Pyrowave impressed industry figures at the Advanced Recycling Conference in Germany with its lifecycle assessment. Pyrowave was “one of the few companies that showed the real numbers . . . Most organizations have been very happy to see that for the first time, companies can show hard numbers that have been generated through full-scale performance.”
Funding and future
The company is continuing to gain traction, with “exponential” growth over the past two years, Doucet said. Tougher regulations for recycled content in products, especially in Europe, has helped drive its business.
Doucet said it is a “signal” for the plastics industry to adopt new technology.
Pyrowave is also catching on Asia, he said, due to new regulations and influence from Asian business leaders who see a market shift.
Doucet said Pyrowave is raising funds to finance growth for the next five years.
He said the firm has received “tens of millions” of dollars to develop the technology. Pyrowave has achieved commercial scale with less money than its competitors because of its modular approach, he said, making it cash efficient.
Pyrowave also plans to expand to other markets and applications. Announcements planned for 2023 include a new platform for new materials. There is also a plan to move beyond plastic polymer recycling to other applications, and a core focus on having impact on climate change, the “challenge of this century.”