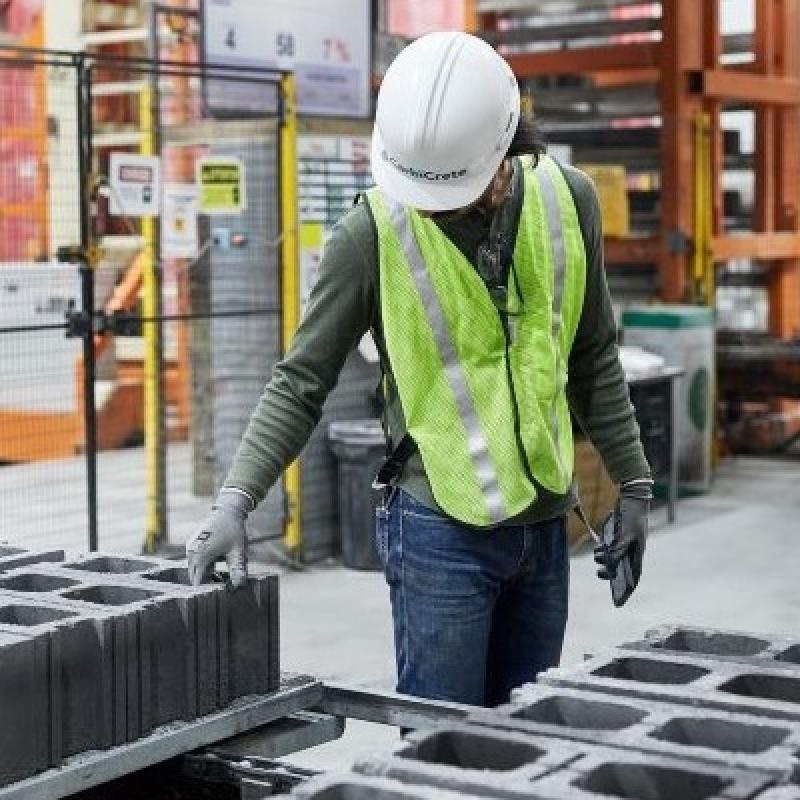
CarbiCrete is primed to become a major player in the North American construction sector after receiving an Environmental Product Declaration (EPD) validation from Climate Earth for its patented cement-free concrete.
The EPD results confirm CarbiCrete's cement-free concrete masonry units (CMUs) achieve a Global Warming Potential of only 11.7 kilograms of carbon dioxide (CO2) equivalent per cubic metre of concrete — 20 times lower than the industry average of over 200 kilograms.
This represents a new benchmark for low-carbon concrete manufacturers facing the challenge of transitioning from traditional concrete containing carbon-intensive cement, a material that accounts for eight per cent of global CO2 emissions due to the high energy intensity and chemical reactions involved in its production.
EPDs provide precise and transparent data to architects, engineers and builders when choosing materials vital to meeting sustainability goals. The Climate Earth certification gives Montreal-based CarbiCrete the equivalent of a manufacturing seal of approval for its cement-free CMUs.
CarbiCrete employs a technology first developed at McGill University that displaces cement with steel slag, a waste product from steel production. The steel slag is then ground into a fine powder and mixed with water, sand and stone as per the traditional method of producing concrete.
By using steel slag as an alternative to carbon-intensive cement, CarbiCrete is able to manufacture a new brand of concrete which can fundamentally reduce the carbon footprint of the built environment.
The company's concrete products are also classified as carbon-negative because of how they are cured with carbon dioxide, which is then mineralized and removed from the atmosphere.
CarbiCrete partners with Canal Block on Ontario concrete plant
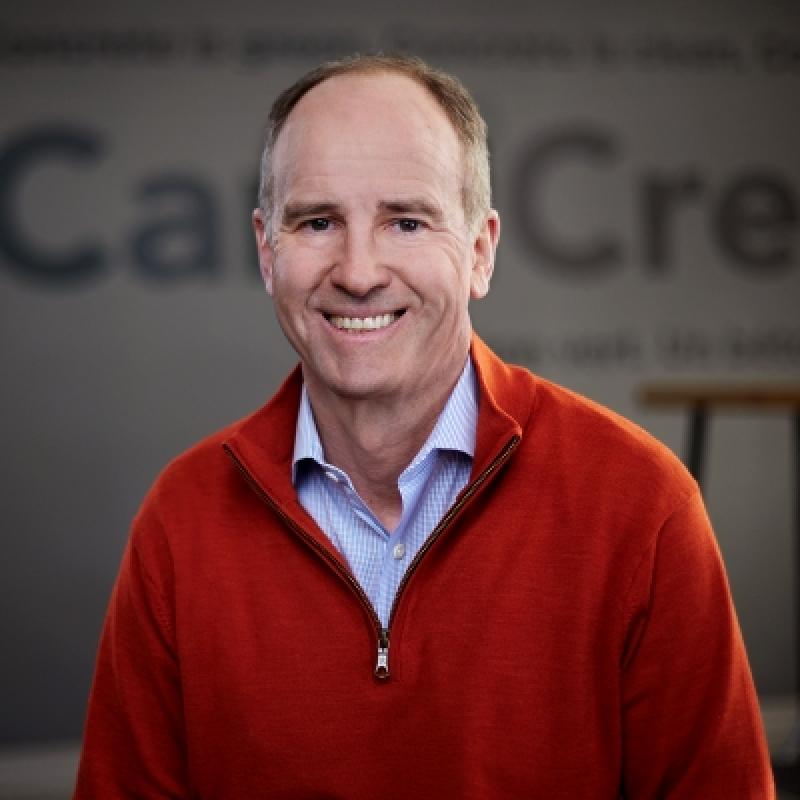
In January, CarbiCrete announced it was proceeding with construction on an $8-million concrete plant in partnership with Canal Block after receiving $3 million in funding from NGen – Canada's global innovation cluster for advanced manufacturing.
The new facility is the first large-scale concrete manufacturing plant of its kind to be built in Ontario. It involves repurposing an existing masonry plant in Port Colborne, owned and operated by Canal Block, that integrates CarbiCrete's technology into the production of cement-free concrete.
This deal has been structured to allow CarbiCrete to expand its market reach while limiting cap ex infrastructure costs. The Port Colborne facility will primarily produce carbon-free CMUs which are a major component of the pre-cast concrete product market that includes cinder blocks, paving stones for walkways and retaining wall elements.
"We expect the Canal Block project to begin production in Q1 of 2025. About 95 per cent of their business comes from selling cement-based concrete products and they're very excited about how CarbiCrete products will help grow and penetrate the market in Ontario for reduced carbon building materials," CarbiCrete CEO Jacob Homiller said in an interview with Sustainable Biz Canada.
". . . Canal Block was eager to build the plant with us because they understood that our technology delivered a very robust CO2 reduction. Overall our concrete products contain only 11.7 kilograms of CO2 per cubic metre of concrete as compared to virtually every other traditional product on the market that is well into the 200s. We're 20 times lower in carbon content than anyone else."
Pre-cast concrete represents an estimated 31.4 per cent of concrete production in North America, while ready-mix concrete (the kind poured at construction sites, roads, driveways) accounts for the remainder.
This offers potential for CarbiCrete to market its zero-carbon concrete tech to a vast client pool of pre-cast concrete manufacturers anxious to meet increasingly stringent embodied carbon standards.
"We're getting more and more traction in the market . . . There are over 2,000 concrete product manufacturing plants in the U.S. alone that are pre-cast facilities. That leaves us with a very large number of companies we can approach to adopt our technology," Homiller added.
"We're also seeing many states and provinces lowering the content requirements for embodied carbon for buildings and other projects - there's going to be stronger and stronger demand for our CarbiCrete solution."
CarbiCrete driving adoption via licensing
Not only does the Canal Block plant guarantee CarbiCrete a stable annual revenue stream, it's also a template for similar scalable cement-free concrete manufacturing facilities in the future.
"In our discussions with Canal Block, they've expressed an interest in future expansion once this capacity comes on the market. But our primary strategy is to license our technology to a variety of concrete product manufacturers and proliferate CarbiCrete products out into the marketplace," Homiller, who was appointed CEO in February, said.
Under his leadership, CarbiCrete is looking to expand into the U.S. market by building a wholly owned concrete plant in Arkansas next year.
"This will enable us to demonstrate the promise of CarbiCrete technology at full scale as well as the improved economics we can deliver to manufacturers."