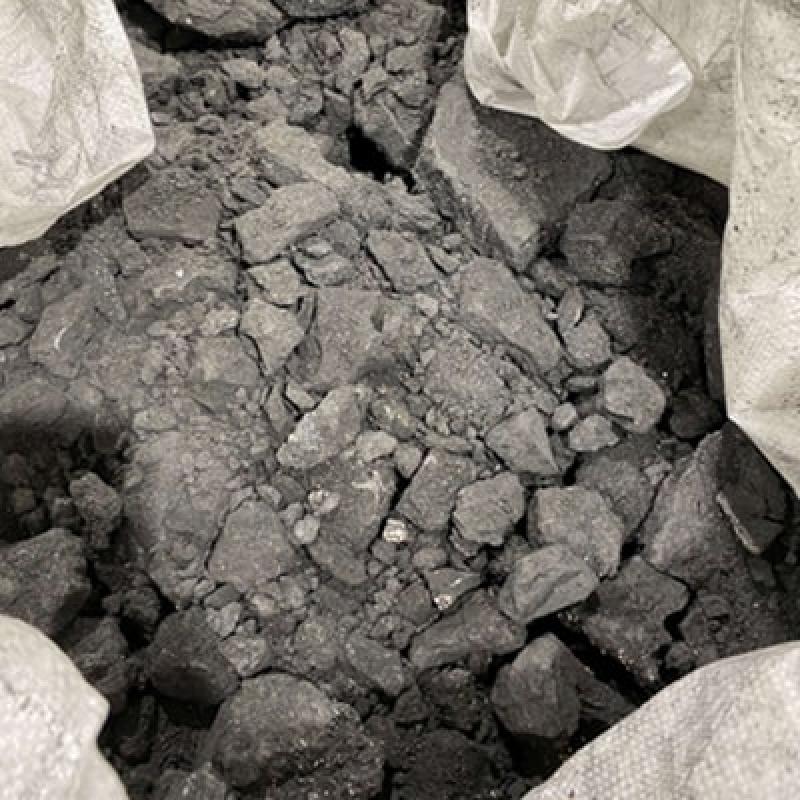
Electra Battery Materials Corporation says it has completed the first plant-scale black mass recycling at its facility north of Toronto, recovering minerals needed for the electric vehicle (EV) battery supply chain.
Black mass is an industry term for the waste comprising end-of-life battery cells. It contains high-value elements such as nickel, cobalt, manganese, copper, lithium and graphite. Once recovered, they can be recycled to produce new lithium-ion batteries.
Typically, black mass is recovered using a pyrometallurgical process. Electra believes its recovery is the first in which a hydrometallurgical process is used.
“These preliminary results represent a significant milestone for the company and the industry as we believe it marks the first hydrometallurgical plant-scale recycling of black mass in North America and the first recovery of a mixed hydroxide nickel and cobalt product,” Trent Mell, Electra’s CEO, said in a statement.
Toronto-based Electra's (ELBM-X) facility is part of a planned battery materials park located in Timiskaming Shores, Ont., where it is also planning a cobalt sulfate refinery as well as a nickel sulfate refinery.
Electra’s progress
Electra launched its black mass demonstration plant at the end of December 2022 and has processed material in a batch mode, successfully extracting nickel, cobalt, manganese, copper, lithium and graphite.
“These results pave the way for us to extend our trial beyond the 75 tonnes we initially planned and maximize the cash-flow opportunities generated through the sale of multiple products critical to the EV battery supply chain in North America," Mell said. "We have established relations with black mass producers in North America and abroad to support our continued efforts.”
Electra has decided to extend its black mass processing and recovering activities through June 2023. Engineering studies will be completed to assess capital costs for a permanent recycling facility adjacent to Electra’s cobalt refinery.
The total amount of material to be recovered will be determined in the coming weeks.
Electra has made significant progress on the commissioning of its cobalt sulfate refinery.
As of Feb. 10 it has completed all testing of existing brownfield equipment; completed 90 to 95 per cent of all procurement; completed 90 to 95 per cent of detailed engineering; completed approximately 90 per cent of the erection of the solvent extraction plant; completed construction of the cobalt sulfate loadout facility; and increased the facility team to 31 personnel.
Previously, the company stated the cobalt sulfate refinery would be commissioned in the spring. However, as a result of critical equipment being damaged en route to the park, all previous forward-looking statements are no longer applicable.
In light of that, Electra is completing a review of the refinery project scope, scheduling and capital expenditures and expects to provide results in the coming weeks.
“While we evaluate a number of options, including the procurement of equipment from alternative sources of supply, construction has progressed ahead of equipment deliveries,” Mell said in a statement.
“Site-level leadership is completing a baseline review of the project and the company anticipates providing an update in conjunction with our year-end results to be issued before the end of March.”
Electra’s battery materials park
In September, SustainableBiz reported on the scoping study for Electra’s battery materials park. At the time, it stated a refinery of that size would cost $731.2 million to $864.1 million, with operating costs between $166.1 million and $176.8 million per year.
Conversely, it’s expected to contribute $299.2 million of GDP impact during the construction phase, plus $551.8 million during the first 10 years of operation.
Scope 1 and 2 emissions would range from 14,000 to 16,000 of tonnes of carbon dioxide equivalent per year.
The location was attractive to Electra not just for proximity to its Toronto headquarters and the North American automotive industry, but also because the province’s hydroelectric grid can power the battery park.
“We will be basically 50 per cent less carbon-emitting relative to similar size refineries that would be done in China,” Joe Racanelli, Electra's vice-president of investor relations told SustainableBiz at the time. “From an end-user perspective, OEMs (original equipment manufacturers) in the space are obviously looking to improve ESG commitments.”
A September report from Clean Energy Canada and the Trillium Network for Advanced Manufacturing predicts given swift government action, a domestic EV battery supply chain could support up to 250,000 jobs by 2030 and add $48 billion annually to the Canadian economy annually.
With no government action, the report states the supply chain would still create 60,000 jobs and contribute $12 billion in GDP during the same time frame.