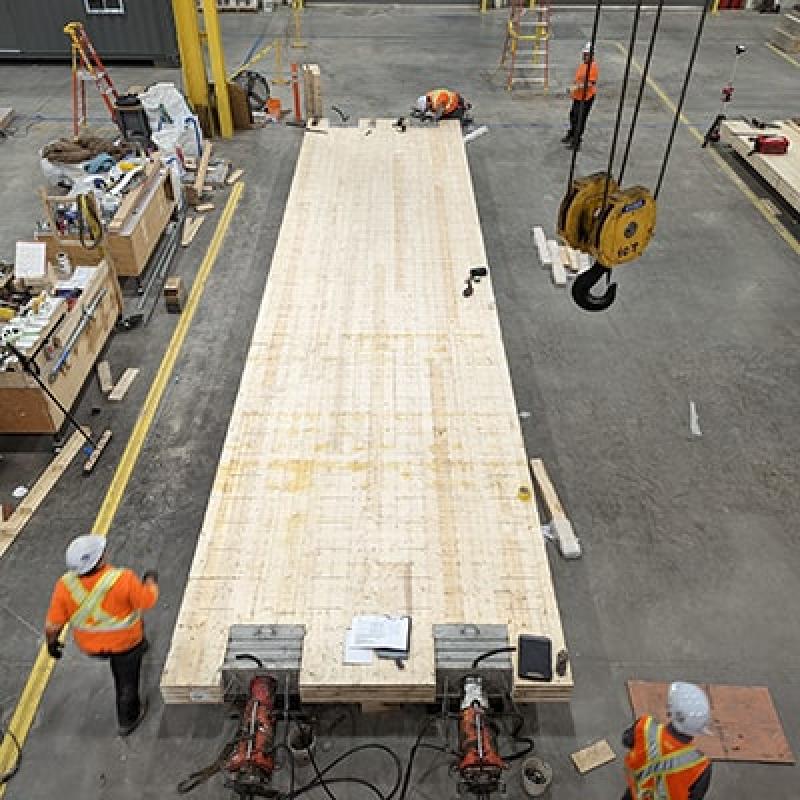
A patented hybrid timber floor system (HTFS) by EllisDon Construction and DIALOG has completed small-scale and fire testing and is now moving on to large-scale tests in Vancouver.
The assessments will take place over at least the next eight to 14 months.
The HTFS combines cross-laminated timber (CLT) panels with steel and concrete to reduce embodied carbon emissions by 25 per cent compared to standard steel and concrete methods, the companies say.
CLT panels are 2x6- or 2x4-(inch) planks which are cross-laminated in a stack to become one solid piece of wood.
The HTFS patent was filed last year by DIALOG, which has been working on it since 2018. The system is a 50-50 joint venture between DIALOG and EllisDon.
“Why don't we just build with wood? It's lower embodied carbon that will help solve our climate problems we have. But there's limitations with wood. One of the limitations with wood is the most efficient way to use wood is a smaller span,” Vince Davenport, EllisDon’s director of building and material sciences, told SustainableBiz.
“So 20, 25 feet is a fantastic span for wood. But it's a short span, if we're used to using concrete/steel. So the idea of this hybrid panel system is to get the same large-span spaces that we're used to with concrete and steel, but using wood, and we're using wood in combination with a little bit of concrete where it makes sense.”
Davenport estimates the price premium over standard steel and concrete is under 10 per cent.
Next steps for the HTFS testing
Two 12-metre long, three-metre wide prototypes of the floor panels have been shipped from EllisDon’s facility in Stoney Creek, Ont., to FPInnovations, a non-profit research institute on the University of British Columbia campus.
“For small-scale, what we did is we built about 20 structural samples. The crux of this technology is the wood working together in composite with the concrete. So there are two connections that force the concrete and the wood to work together. One is a screw and one is a curved (steel) plate. (There are) an array of screws and an array of steel plates,” Davenport explained.
“We built these small-scale samples in our factory, we shipped them out to the FPInnovations lab in Vancouver and we tested them for short durations. Immediate failure, eight hours, and then we also tested to all the way to 90 days to get some long-term creep.”
For the fire tests, EllisDon sent two small-scale samples to the Natural Resources Canada lab in Ottawa. Standard two-hour tests were conducted, which confirmed EllisDon’s calculations the boundary between concrete and wood was “not an issue.”
While the HTFS system is currently being tested for small buildings, its applications are varied.
“Not necessarily in a tall building, it could be applied anywhere in any commercial space,” Thomas Wu, structural engineer and partner with DIALOG, previously told SustainableBiz. “Whether you’re in Toronto or Vancouver or New York or Singapore, that will be ideal for us. And the idea is to promote the use of wood and try to break out of its limitations.”
The future of hybrid timber flooring
The first aspect of the large-scale testing will be to assess the vibrations of the panels in different arrangements.
“Then the second thing, then we load them for long-term creep, which is just like a sustained load for long-term,” Davenport said. “And then we eventually do sort of, test to failure if you will. But that wouldn't happen 'til the very end.”
EllisDon has a team of concrete experts looking into low-carbon concrete applications for the system as well.
“There's two parts that are concrete. There's a post tension beam, and then there's a concrete topping that goes on top of these hybrid panels,” Davenport said. “The idea would be that that topping can be poured with a low-embodied-carbon concrete. So like, you know, we could do . . . up to 70 per cent with that mix.”
He hopes within the next six to eight months, the companies will be able to publish a life-cycle analysis of the system.
DIALOG also hopes to utilize the HTFS in skyscrapers.
DIALOG’s 105-storey Hybrid Timber Tower design concept for Toronto was named by Fast Company Magazine as one of its World Changing Ideas of 2021. If completed, it would also become the tallest building in Toronto.
Currently, the plan is for EllisDon and DIALOG to be ready to begin work on a smaller building with the HTFS system in “six to eight months.”