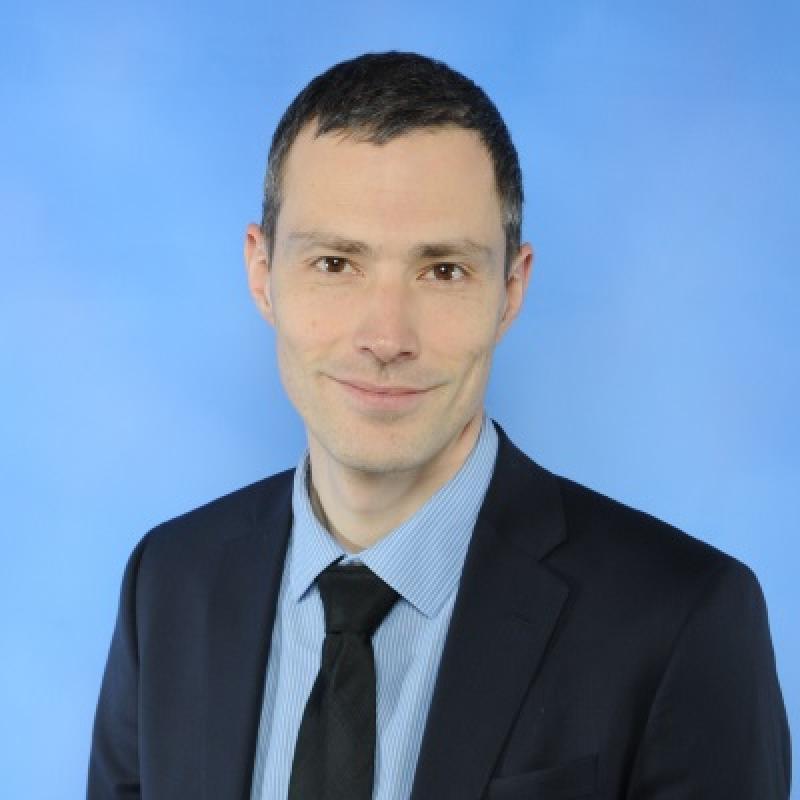
Montreal-based Geomega Resources is moving ahead with the construction of a magnet recycling demonstration plant in Quebec designed to help pave the way for growth in the province's rare earth metals industry.
It is located in a new industrial complex in Saint-Bruno-de-Montarville, 20 kilometres outside of Montreal. The plant has been conceived as a cost-effective, scalable and sustainable means of recycling up to 4.5 tonnes of wasted rare earth metals – in the form of magnets that are currently being disposed of in scrapyards or stored in landfills.
Construction of the demo plant is expected to begin in late spring, as soon as engineering and other preliminary work has been completed. The project is the latest step in Geomega's pioneering development of advanced new processes that allow for the extraction, separation, and reuse of rare earth elements, commonly referred to as rare earth metals.
Geomega can now accelerate its push to the construction phase following the Jan. 30 announcement that Geomega has been awarded $3 million in funding from Quebec's Technoclimat Program, administered by the Ministry of the Environment and the Fight Against Climate Change, Wildlife and Parks.
"Developing new technologies that will make the future environmentally sustainable while remaining competitive with legacy technologies is challenging, but the continuous support from the government over the last few years has allowed our team to achieve that," Kiril Mugerman, CEO of Geomega, said. "As we continue with procurement of equipment and approach the construction phase, we get a step closer to bringing the rare earths industry to Quebec."
Rare earth metals critical to EV and wind turbine sectors
Rare earth metals such as praseodymium, neodymium, terbium and dysprosium are ubiquitous. They are essential components of the permanent magnets used in the motors of electrical vehicles and wind turbines, and present in smartphones, elevators, trains, MRIs, missile guidance systems, LEDs and many consumer durables.
With the explosive growth of the electric vehicle (EV) industry in the U.S. and Europe, there are fears of looming shortages in rare earth metals vital to industries which are critical to reducing our carbon footprint.
Mugerman, who studied geology at McGill University in Montreal and previously worked as an exploration geologist in the gold industry, believes there is unlimited untapped potential in recycling magnet waste.
"Our demonstration plant is part of a viable and sustainable solution to the vast quantities of mineral waste produced by mining companies," Mugerman said. "The promise of our technology is that it provides the means to recycle this waste material by chemically separating and recovering the rare earth metals for sale to the magnet industry."
Geomega's long-term goal is to offer mining companies the means to environmentally dispose of their waste and extract some value from material that would otherwise go into a landfill. By recycling the material essential to the production of permanent magnets, Mugerman said his company is "advancing the goal of a green energy ecosystem and helping create a circular economy."
Reducing dependence on China
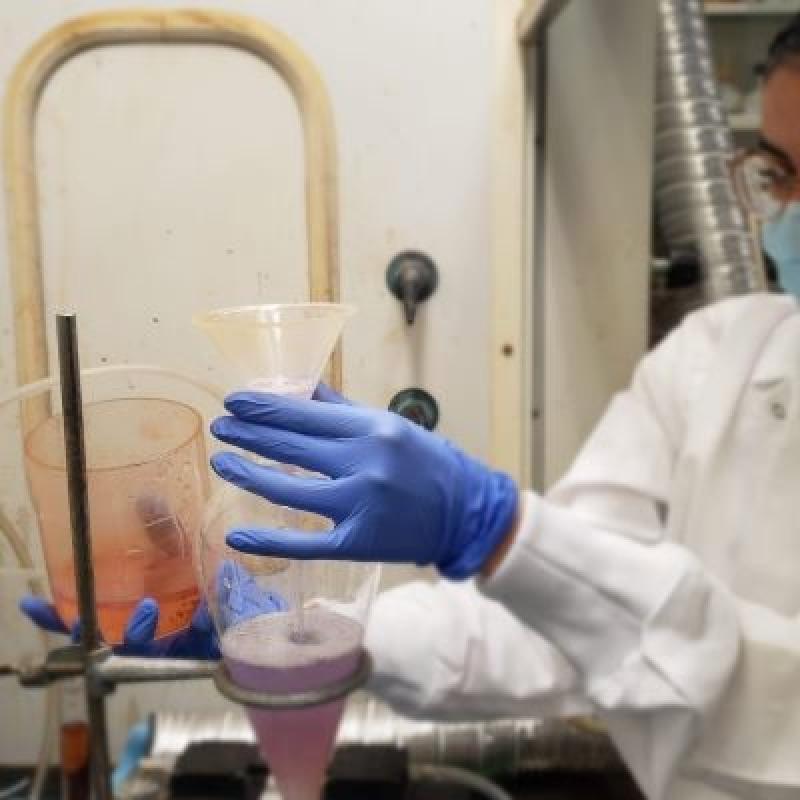
It would be an understatement to say China has cornered the rare earth metals market – supplying 95 per cent of the world's rare earth metals and an estimated 75 per cent of material used in electric vehicle batteries.
The world's second-largest economy saw the benefits of mining and processing rare earths over a decade ago, and has since built up a vast processing industry that has allowed China to gain a monopoly in the supply of rare earth metals.
This has created considerable economic and political anxiety in the West, especially in light of the Russia's invasion of Ukraine and subsequent cut-off of oil and natural gas exports to Europe.
Mugerman said China's waste magnet recycling industry has increased its capacity "tremendously" over the last 10 years to keep up with rare earth production.
But, "China has a lot of plants that are processing those metals and doing so in way that is not very efficient and likely not in a very environmentally friendly way," he added.
To keep up with production of rare earth minerals in Europe or North America, Mugerman said the only choice is to come up with new, clean and sustainable technologies. It will require infrastructure to build the collection points for magnets and the means of transporting the waste to centralized processing plants to produce oxides that can be reused to make new magnets.
Major automakers sourcing rare earths directly as part of transition to EVs
Heightened geopolitical risk and general concerns over rare earth metal supply bottlenecks have led some of the world's leading automakers – General Motors, Volkswagen, BMW, and Tesla (the first to do so) - to guarantee supply by purchasing minerals directly from Western mining companies, or in some cases, investing directly in mining operations to help grow production to meet future demand.
Mugerman believes Geomega can be part of a Western crusade to reduce dependency on China by recycling the rare earth metals that feed into the North American magnet industry.
Mugerman has seen more European companies announcing projects to create a supply chain for that continent.
In North America, he believes there will be a significant amount of new magnet production facilities built over the next two to five years. He referenced General Motors' partnership to build two similar kinds of magnet facilities and a few Chinese companies that are also preparing to enter the field.
In parallel fashion, Geomega is on the frontier of a new industry that will occupy an important niche in the permanent magnet industry. Demand will rise exponentially over the course of this decade as the electric vehicle industry continues to increase its share of the auto market.
Permanent magnets have been critical to the development of the electric vehicle industry.
They're used in the electric drive trains of EV engines that allow the motors to operate more efficiently.
"Tesla saw as far back as 2016 that an important means of accomplishing that was to switch to magnets because the induction motors they had been using for their EVs at that time were very heavy, consuming more energy and therefore reducing mileage," Mugerman said.
"Switching to permanent magnets in the drive train of EV engines allowed Tesla to build a much more efficient motor that would cover a greater distance with each charge. And by producing batteries using rare earth magnets, they were also able to develop more efficient battery energy storage systems."
Wind turbines are now being powered by permanent magnets
In Canada, the wind turbine industry is becoming increasingly vital to the green hydrogen sector. Newfoundland will soon install 164 wind turbines along its Port au Port coastline as part of the ambitious green hydrogen project led by John Risley, chairman of World Energy GH2.
"This is another important application for these magnets," Mugerman said. "As the wind power industry has been maturing in recent years, you've seen more and more producers shift towards the permanent magnet.
"By placing these magnets into the big rotor inside the turbine, the turbine becomes much more efficient being driven by magnets rather than by lots of copper coils and gears and other components that were part of the old technology."
Geomega also targeting bauxite Quebec aluminum industry
The implications of Geomega's rare metal extraction technology are vast. In addition to its magnet recycling demonstration project, the company is also proceeding with the development of a Bauxite Residues project in Boucherville, Que.
Last April, Geomega announced that Rio Tinto, a major Quebec aluminum producer, would provide $1 million in financing to Innord Inc., a wholly-owned subsidiary of Geomega. The funds will go toward a feasibility study as well as construction of a $4-million bauxite residues pilot plant this year.
Geomega hopes that its Innord bauxite facility will demonstrate how its processing technology can extract value from mining feeds, tailings and other industrial residues which contain rare earths and other critical metals.
"Bauxite residue is a problem and we are developing a solution to help eliminate that problem," Mugerman said. "So imagine a plant that produces one million tons of bauxite residue per year. We are trying to reduce that by up to 95 per cent by applying our processing technology to the extraction of metals from the residue and then produce them in a form that's sellable."
The extraction technology may ultimately be useful in producing iron, titanium, rare earths, and other metals that could then be sold on the market.
"Looking at the long-term picture, our technology (could be) applicable to every single bauxite residue facility around the world and that is a very good growth opportunity for us."
EDITOR'S NOTE: This article was updated after publishing to reflect that the demo plant is not yet under construction, but rather in the preparatory phase before breaking ground.