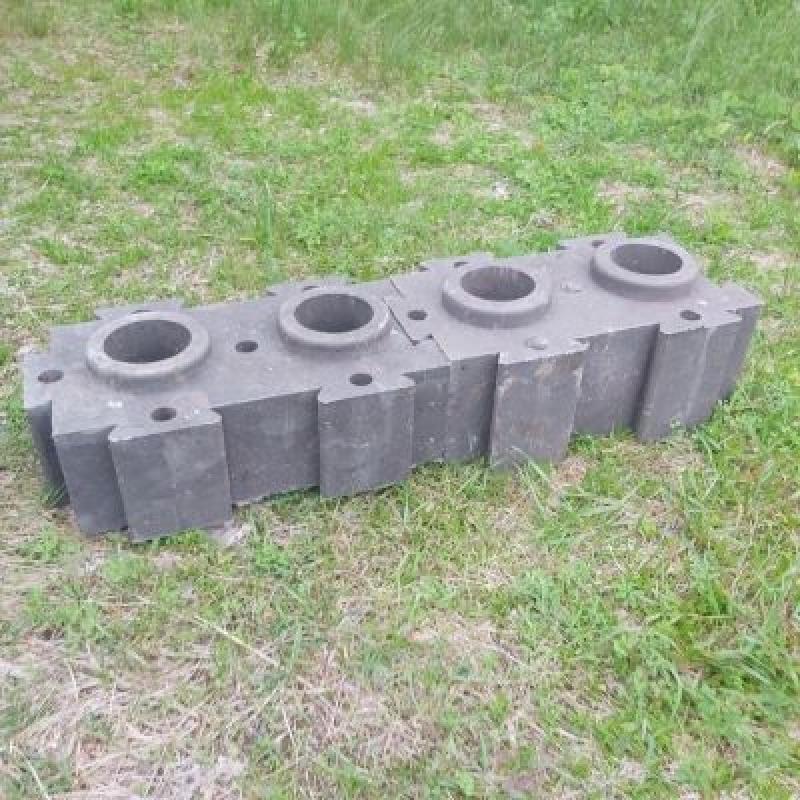
An “absolutely terrifying” statistic that hangs over the mind of Dustin Bowers is the average age of a skilled trades worker in North America: 60 years old, he said, meaning mass retirements are looming.
Bowers uses words like “apocalypse” to describe the coming labour situation in Canada (other estimates put the average age in the 50s). He is equally worried about mountains of waste building up around the world, particularly long-lasting plastics.
Bowers, a life-long construction and trades worker-turned-entrepreneur, is looking to help solve these two problems with his company PLAEX Building Systems Inc.
Based in Dieppe, N.B., PLAEX was formed after Bowers’ previous work experience in Vancouver, where he said it became “blatantly clear” solutions must be developed for managing waste and bridging the skilled labour shortage.
“We take difficult-to-recycle plastics and combine them in a unique composite material to form fully-interlocking building systems,” he said during an interview with Sustainable Biz Canada.
PLAEX-Crete
PLAEX is behind PLAEX-Crete, a material that is 90 per cent to 100 per cent made out of mineral construction waste and difficult-to-recycle polymers.
The material is manufactured at a demonstration facility in Dieppe, where plastic from its partners is sorted, shredded, processed and mixed into the composite to be molded into shapes.
By reusing the waste and polymers, PLAEX-Crete pulls out what would have otherwise lingered in a landfill or ocean and gives it a second life. Lab testing conducted at the University of New Brunswick found a brick of PLAEX-Crete offsets 42 kilograms of carbon, he said.
The company points to studies that show PLAEX-Crete is cost-effective, water-resistant, durable and insulating, making the argument for its use in a wide range of structures.
After touting its sustainability features, Bowers also pointed to the ease of use of PLAEX-Crete which is in similar fashion to Lego bricks. It is based on an interlocking panel system that does not require cuts or mortar, making it three- to four-times faster to build than traditional materials, the company says.
Being easy to assemble is intended to alleviate the labour shortage problem, requiring less of the experience and technical skills traditionally needed in homebuilding
“We need to simplify (construction). Our design is the simplest possible design that still incorporates many of the building facets.”
The simplicity of PLAEX-Crete also bolsters its use in automated homebuilding, Bowers said, furthering its potential as an answer in a future with fewer skilled workers.
PLAEX-Crete is designed to be part of the circular economy.
If the user changes their mind about the structure, walls can be disassembled and the bricks re-used. If the PLAEX-Crete brick reaches its end-of-life, the company has plans to take it back (provided it is located close to PLAEX or its partners) so it can be crushed and recycled into more PLAX-Crete, or put through a chemical recycling process.
PLAEX-Crete products
PLAEX-Crete comes in two forms: LinX and Brick&Panel.
Brick&Panel is the interlocking wall system designed to be intuitive for assembly, then covered by PLAEX’s panel product.
The PLAEX CEO said Brick&Panel is undergoing ASTM International standard testing to certify its use for the building industry and the company is hoping to receive the certification by 2025. He is confident the product will be certified for residential use, specifically low-rise construction ranging from two to three storeys.
LinX is a landscaping product intended for use in structures such as garden beds, sheds, walkway edging, patios and fences.
LinX is made to reach the market quickly, being simpler and retail-friendly, and has already been used in a few projects, Bowers said. By the end of 2023, the product will be offered in three to four retail locations on Canada's east coast.
The Stone Depot in Halifax is one of the retailers.
Pre-orders for the company’s products have been “wild,” Bowers said. Three months of pre-orders have covered 50 per cent of its 2024 production capacity.
PLAEX’s future
To expand PLAEX, Bowers said its investors intend to license its technology in Atlantic Canada in 2024 and deploy an automated factory. He hopes to have one to three deployments of PLAEX-Crete as well.
Bowers hopes to close PLAEX’s seed round by the end of January, and move on to its Series A round to assist in its ambitions for national and international scale-up.
Companies in Ontario, Alberta, British Columbia, the United States, Jamaica, Nigeria, England and the Philippines have expressed interest in licensing PLAEX, he added.