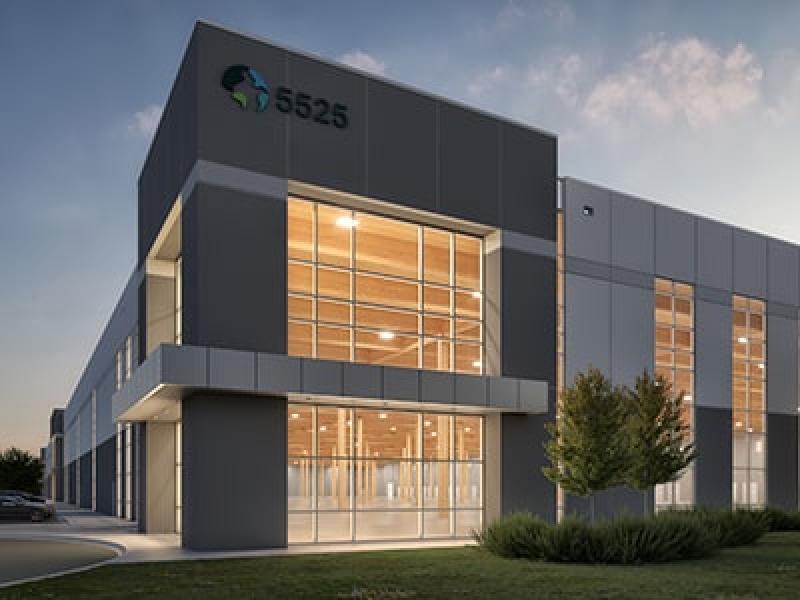
Prologis Inc. says it is the first company in the Americas to utilize prefabricated panels and mass timber to reduce embodied carbon emissions in its construction of a Hwy. 50 distribution centre in Brampton, Ont.
Work on building three at the Hwy. 50 and Countryside Drive property will begin in June, and is to be finished in September 2024. The company states the construction techniques will reduce embodied carbon emissions by 1,480 metric tonnes – equivalent to the annual emissions of 186 homes.
“We've experimented a lot of times, highlighting one innovation (at) a time on a project. Really, this came as a challenge from senior leadership to say, 'how many different things can we try and experiment at once?’ ” Travis Harvey, Prologis’ (PLD-N) head of development for east region, told SustainableBiz.
"The challenge is, our projects, when you design it and build it takes a couple of years, right? So we really wanted to be ambitious on this one and strive to see how far can we plant the flag down the field on this carbon reduction approach?”
The building is targeting LEED Silver certification.
Prologis is a real estate investment trust that invests in logistics facilities, headquartered in San Francisco. It is present around the world, with other headquarters in Shanghai, Tokyo and Amsterdam. Last year, the company launched a net-zero emissions goal by 2040.
Prologis’ Hwy 50 Distribution Centre
The panels will be sourced from Squamish, B.C.-based Nexii Building Solutions Inc. and the mass timber will be certified as sustainable by the Forest Stewardship Council.
Nexii produces Nexiite, a concrete alternative that is poured and cast into prefabricated panels in the same fashion as traditional concrete, but contains no Portland cement, lime or adhesives. Nexii says Nexiite can cut embodied carbon by 36 per cent compared to regular concrete.
“Other panel options were out there, but you start introducing more steel bracing and you're kind of slipping back from any of the gains that you're making, is how I would describe it,” Harvey said.
Prologis has an innovation council that examines options for different building materials, such as Nexii. The Squamish company “checked a lot of boxes” for Prologis; they are prefabricated with windows, fit Prologis’ height requirements and weigh about one-sixth of a typical pre-fabricated panel, to name a few of the features.
According to Prologis, Nexii's panelling cuts carbon emissions by 17 per cent compared to its precast concrete counterpart.
"We explored what were alternatives to the embodied carbon in the steel,” Harvey explained, “and that's where we ended up with mass timbers approach to replace the columns, the joists, girders and the metal deck as well.”
Mass timber is a combination of cross laminated timber roof panels and glued laminated beams and columns. Prologis states the mass timber offers a 62 per cent decrease in embodied carbon emissions compared to the steel skeleton structure it is replacing.
“The mass timber will be sustainably sourced and that's one of our requirements that we're going to make sure we apply to anybody who is supplying the project,” he said.
The panels and timber combined will net an estimated 24 per cent reduction in embodied carbon emissions over the entire building structure.
“The whole goal is to really learn best practices here. That's the exciting part, was just being able to share globally, lessons learned,” Harvey said. “We have counterparts in Europe that are very advanced on the ESG and green initiatives, so we're always looking for solutions that we can apply at a broader scale.”
Other sustainability features
The facility will be equipped with multiple electric heat pumps for air conditioning in lieu of gas, feature an electric vehicle charger and be solar panel-ready.
“We're looking at this on a 40-, 50-year lifespan of the building and want to make sure that we've built to withstand that time,” Harvey said.
‘Solar ready’ refers to the electrical switchgear and the solar loads that are introduced, and the lifespan of the roof, which increases the time Prologis can have photovoltaic panels installed. There is currently no estimate of how many megawatts the building could support, only that it will be ready for solar installation.
Fifty per cent of the vehicle stalls will be ready for electric-vehicle charger installation when the site is complete, and five per cent will have chargers already installed.
For overall building emissions reductions, Prologis is working with a third party to complete a full life-cycle analysis.
“One of the biggest parts of our net-zero strategy is to continue to help look at ways to electrify other aspects of our customers’ operations, whether that's their fleets or their energy use on the buildings,” Suzanne Fallender, Prologis’ vice-president of global ESG, said. “So that's the bigger part of the net-zero strategies.
"Once they're in the building, then it's continuing to partner with them on what those future opportunities are.”