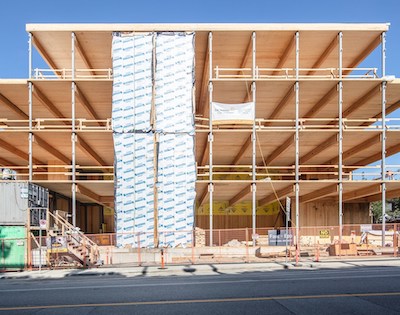
The superstructure of the new Fast + Epp head office in Vancouver was completed in four weeks. (Michael Elkan Photography / Fast + Epp)
Vancouver-based structural engineering firm Fast + Epp has incorporated a home-grown product, B.C. timber, as a major structural component in its new four-storey head office. The project, supported by funding through Natural Resources Canada’s Green Construction through Wood Program, is far from the company’s first foray into mass timber construction.
“We hope to bring the industry forward and support the growth of timber construction,” said Carla Dickof, a timber specialist working in Fast + Epp’s technical division on research and development projects.
Using wood for such a project offers two significant environmental benefits. The firm estimates there are 500 metric tons of carbon captured in the wood it is utilizing, and it avoids creating an additional seven hundred tons of carbon which would’ve resulted from the use of other materials.
Fast + Epp “pushing the limit” on design
The building is located near downtown Vancouver on Yukon Street, and features thermal, moisture and vibration monitoring. The cross laminated timber structure features glulam beams and steel posts. It is constructed with long-span floors designed to withstand a potential earthquake.
“We’re really pushing the limit on design particularly from the vibration perspective, which really comes down to the human experience,” said Dickof.
The building also incorporates smart glass so Fast + Epp will be better able to control energy usage in its mechanical systems.
The GCWood Program promotes wood as a renewable construction material, especially given its availability in the Canadian market. The Canadian government announced $39.8M in funding two years ago to support green building materials. Construction best practices utilized within the GCWood Program are being shared among the design community.
The investment is paying off, according to Dickof.
“I would say it is gaining popularity across North America,” she said. “It certainly wasn’t the first choice for head offices at a time, but we are starting to see a shift.”
Brock Commons and other projects
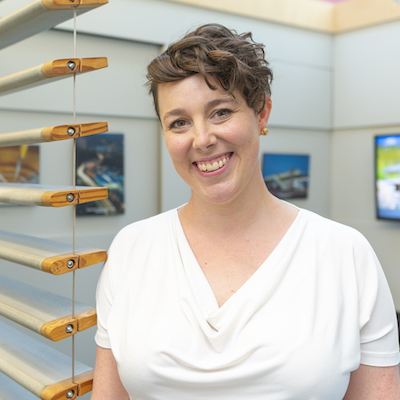
Carla Dickoff, a timber specialist and associate with Fast + Epp engineers. (Fast + Epp)
Fast + Epp has been playing its part in that shift, at previous projects such as Brock Commons at the University of British Columbia. The $51.5 million, 18-storey building was the world’s tallest mass wood, steel and concrete hybrid development.
Now, thanks to its innovative work, the company has been contracted for other ambitious wood construction projects in the United States.
“We’re working on Walmart’s head campus in Arkansas,” said Dickof.
She believes Fast + Epp’s decision to follow this course with its own head office will also carry weight with future prospective clients and developments.
“Being able to use our home office and other projects really helps show large companies they can have beauty, while also achieving sustainability,” said Dickof.
By hosting meetings at its head office, potential clients can see the quality of a wood-made structure, while also getting a feel for the biophilic design – a concept used to connect building occupants to the natural environment.
“We see the opportunity to be able to share the experience in more depth with architects or developers or whoever is interested, really about what a wood building can look like and how it feels,” said Dickof.
Time, costs savings with mass timber
Wood and mass-timber construction can also offer time and cost savings. Dickof said Brock Commons was completed nearly four months ahead of schedule – in part because the prefabrication process cuts down on the actual construction work needed on-site.
Completion of the superstructure for its head office took just four weeks.
“Wood offers the opportunity to really speed up the erection of a structure, which really has more to do with the extent of prefabrication that happens,” she said.
Wood finishes can be simpler and more cost effective because there is often no need for materials like drywall, which could add significantly to the cost of a large building. In structures like its head office, the timber is simply finished and left exposed, showing the natural qualities of the wood.
In Fast + Epp’s case, it’s B.C. location is also a geographical benefit because of its proximity to the forest industry.
“We’re very lucky to be in B.C., where it has really strong and well-regulated forestry practices so we know the wood meets all the certification,” she said.
Wood materials have been involved with a significant amount of Fast + Epp’s projects since Dickof arrived at the firm in 2012. She previously worked at Blackwell Structural Engineers as a project engineer on commercial, recreational, educational, and residential projects.
Broader applications for wood construction
She believes every completion of a wood construction building moves the industry a touch closer to using the material more consistently.
“I think every new timber building offers an opportunity to help grow that basis of knowledge, to help grow that understanding of how great timber is as the main construction material,” she said.
Down the road, she would like to see wood materials compared more often to concrete and steel for building construction projects, though she acknowledges each of these techniques has its place.
“I’d like it to be a consideration for every building where, you know, an architect or a developer sits down right at the beginning (and) they’re considering wood as an option equal to steel and concrete,” she said. “I really think that to some degree, the sky’s the limit.”