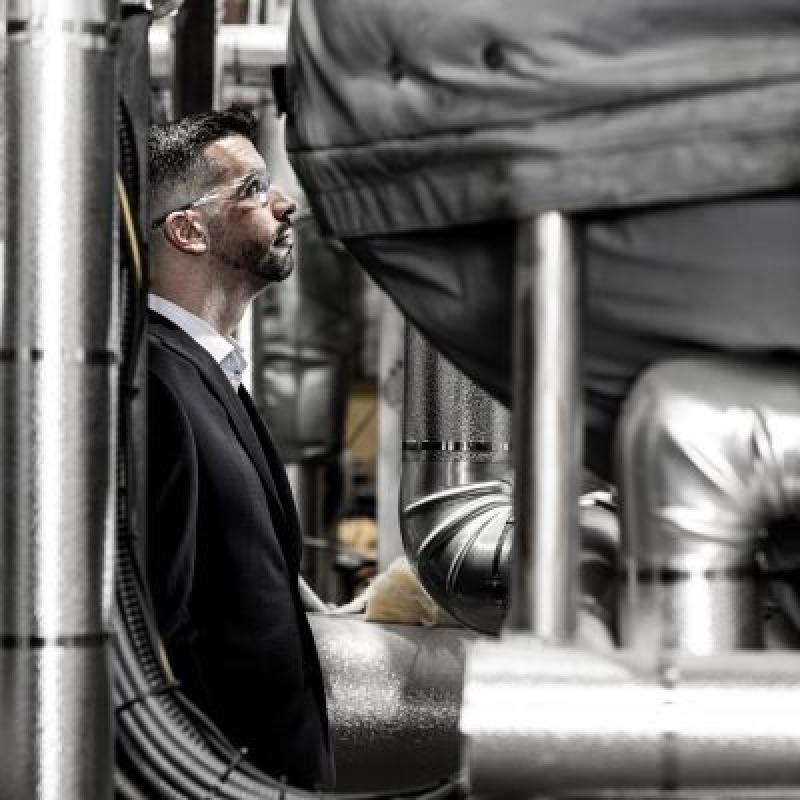
After showing off its years of work on microwave-based plastic recycling technology last year, Montreal's Pyrowave has revealed efforts to also utilize microwaves for greener cement production.
“One thing that we have now internally is the know-how around microwaves and how we can use it for a plurality of different materials to make them lower carbon,” Pyrowave CEO Jocelyn Doucet told SustainableBiz.
“One of our values at Pyrowave is we want to have impact and by working on two of the three largest emitters in terms of materials – cement and plastic – we want to maximize our impact using our technology, as in that context that we decided to deploy our microwave platform to manufacture cement with a low carbon footprint.”
Cement is one of the largest global sources of greenhouse gas, responsible for approximately eight per cent of global emissions. After developing a way to recycle plastics with microwaves, Pyrowave realized microwave ovens could also be used to heat limestone to make cement clinker, an ingredient in Portland cement.
Pyrowave claims to not only cut carbon emissions by 40 per cent compared to traditional cement production, but to speed up cement manufacturing and lower costs.
Microwaving cement
Doucet said Pyrowave isn't pioneering a new process – rather, it's reviving an idea whose time may have arrived. He said microwave ovens were explored in the 1970s and 1980s by the cement industry as an alternative to using carbon-intensive fuels to heat limestone. But the lack of concern over global warming at the time, combined with no differences in production, meant there was little to no interest.
Today, the environmental landscape is very different.
Pyrowave is reviving the idea because it has the know-how and intellectual property to do it at the industrial scale. It has discovered significant advantages in using microwaves to heat limestone to form the clinker.
The first is the reduced greenhouse gas emissions. Pyrowave uses electricity rather than hydrocarbons to power its process, so a cleaner electrical grid will decrease pollution. Doucet pegged the carbon reduction at 40 per cent compared to traditional measures.
It's also faster than conventional cement making, which is time-intensive because the heating mechanism has to compensate for its conductivity and cement’s insulating properties. Pyrowave’s microwave ovens heat the limestone with an electrical field rather than heat conduction, so it significantly reduces the reaction time, Doucet said.
This means kilns and reactors can have a smaller space footprint, which also increases cost effectiveness.
Finally, Doucet said it avoids introducing air to cement. “So the CO2 (carbon dioxide) that is produced by the reaction itself is a pure stream of CO2. It is not contaminated with combustion air, so therefore the capture or sequestration of CO2 from our process is therefore more cost-efficient.”
Partnerships and the future
Thus far, the technology has only been tested in a lab environment. Pyrowave hopes to scale up to pilot projects to quantify and demonstrate its energy efficiency.
It has already lined up an “important” partnership, and will be announcing another with a university with a specialized department for cement production. A cement industry association is also supporting Pyrowave’s efforts to scale up its technology.
Doucet said Pyrowave does not want to be a cement manufacturer and prefers a business model selling its technology to existing manufacturers.
“I think there is a lot of pull from the industry to have new technologies," he said. "There’s a lot of demand from the market, driven by public procurement because most of the cement is purchased by the governments and municipalities and public works.”
The Canadian government and a cement industry association published Roadmap to Net-Zero Carbon Concrete By 2050, outlining a plan to slash the industry’s emissions.
If the results are promising, Doucet said Pyrowave may spin off its cement side and raise money.
“I think this industry (is) more than a century old and yet they’re still using the same technologies and the same fuels and the same recipes as before. I think there is a lot of movement in the cement industry . . . I think we’re bringing something really new to this industry," he concluded. "I would hope that our technology is pretty much everywhere years from now and people can now use electricity to make renewable materials.”