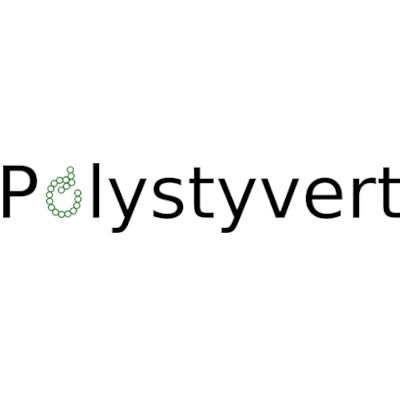
Polystyvert is one of only 100 companies worldwide to be recognized by the WEF as a technology leader. (Courtesy Polystyvert)
Montreal-based recycling company Polystyvert has secured the funding it requires to develop a plant capable of upcycling one of the most notorious plastic waste offenders – polystyrene.
The development will improve environmental protection efforts by reducing greenhouse gas (GHG) emissions and reducing the amount of waste which ends up in landfills or the environment.
In Canada, 63 per cent of plastic waste is comprised of single-use plastics and packaging.
Polystyrene is one of the most widely used plastics, employed in the creation of a variety of consumer products. Expanded polystyrene, commonly called Styrofoam, is used in the creation of packing peanuts, disposable cups, plates and take-out containers. Solid polystyrene is used to make plastic cutlery, yogurt containers, DVD cases and more.
However, despite occurring naturally in nature — specifically in foods such as strawberries, cinnamon, coffee and beef — Styrofoam is only recyclable if it is clean, un-dyed and uncontaminated, conditions that rarely occur considering the material is often manufactured as containers for food.
Being discarded in a dirty recycling bin with other messy materials can also contaminate the product even if it is clean when placed in a Blue Box. As a result, 80 per cent of Styrofoam products end up in landfills and the environment.
The release of the product into the atmosphere is all the more concerning because the International Agency for Research on Cancer (IARC) lists styrene — the basic building-block chemical used in the manufacture of polystyrene and Styrofoam — as a probable carcinogen. The material is also commonly contaminated with flame-retardant chemicals which can enter the environment and harm human health.
Polystyvert’s innovative polystyrene recycling
Traditionally, the toxic plastic has been practically impossible to recycle. However, Polystyvert discovered a way.
Founded in 2011 and aptly located on “rue de l’innovation” (Innovation Street), the company developed a breakthrough technology for recycling the plastic using a dissolution process effective for all types of polystyrene. The process earned it the distinction of being among just 100 companies worldwide to be recognized by the World Economic Forum as a technology leader.
The process works by combining polystyrene with the company’s specially-designed oil, which dissolves the product in seconds, at room temperature, eliminating the risk of emissions. The process does not produce any waste, since the solvent is recycled and is specifically selected for its high level of safety; it only dissolves polystyrene. This unique technology can also treat contamination (including food, labels and residue) that would otherwise prevent the plastic from being recycled.
The dissolution process does not alter the material’s properties; however, the resulting dissolved polystyrene (a liquid) requires 10 times less space to transport than expanded polystyrene (a solid).
“Dissolution is an efficient, low-energy technology which offers a cost-effective solution to recycle (polystyrene) in a closed loop,” said Solenne Brouard Gaillot, Polystyvert’s CEO, in a release describing the process.
The company also employs a filtration process allowing large contaminants — including cardboard, paper, plastics, and metals — to be rapidly removed. The recycled polystyrene is transformed into pellets suitable for applications such as extrusion or injection molding, either with 100 per cent recycled content or mixed with virgin polystyrene pellets. The process reduces the need for raw petroleum products, as recycled polystyrene can replace the same quantity of virgin material that would have to be made from fossil fuels.
In pioneering this process, the company created a circular economy for polystyrene, allowing upcycled products to be reused for multiple applications and opening the door to a larger market than mechanical recycling technologies. Polystyvert also developed a purification technology, which provides purified polystyrene products with the same properties as their virgin counterparts.
“The purification capacity of Polystyvert’s technology is unique,” said Ricardo Cuetos, vice president, standard products, Ineos Styrolution Americas, in a release. “The high quality of the final recycled (polystyrene) resin is essential to achieving a truly circular economy in key markets like food-service packaging.”
Polystyvert investors fund new recycling facility
A recent round of funding introduced new private investors, as well as European investor BEWI Group, which provides packaging, components and insulation solutions. The company is one of the largest integrated expandable polystyrene producers in Europe with an annual production capacity of 200,000 tons.
“BEWI sees great potential in Polystyvert’s technology because it has the ability to treat highly contaminated streams while remaining very energy efficient,” said Jonas Siljeskär, COO of BEWI, in a release. “We believe this technology could be a game-changer for using recycled material in food packaging.”
Polystyvert has worked with multiple partners over the past 10 years — including Sustainable Development Technology Canada (SDTC) and Technoclimat — to prevent polystyrene from ending up in landfills. Thanks to funding provided by these partners, Polystyvert will develop a new facility, which will be a milestone for the cleantech startup.
Some of the company’s other partners involved in the most recent funding round include:
– Cycle Capital Management;
– Anges Québec;
– Anges Québec Capital;
– Energy Foundry;
– Quadriam;
– Ineos Styrolution Americas;
– The Polymers Business unit of Total S.A.
“Thanks to the financial backing from BEWI, as well as existing investors, we will be able to demonstrate the technological maturity of the Polystyvert process and . . . prove it has the best (life-cycle assessment) on the market,” said Brouard Gaillot, in a release. “This funding, coupled with BEWI’s expertise, will enable us to expand our presence and commercialize our technology in Europe where the demand for recycled plastic is increasing the fastest.”