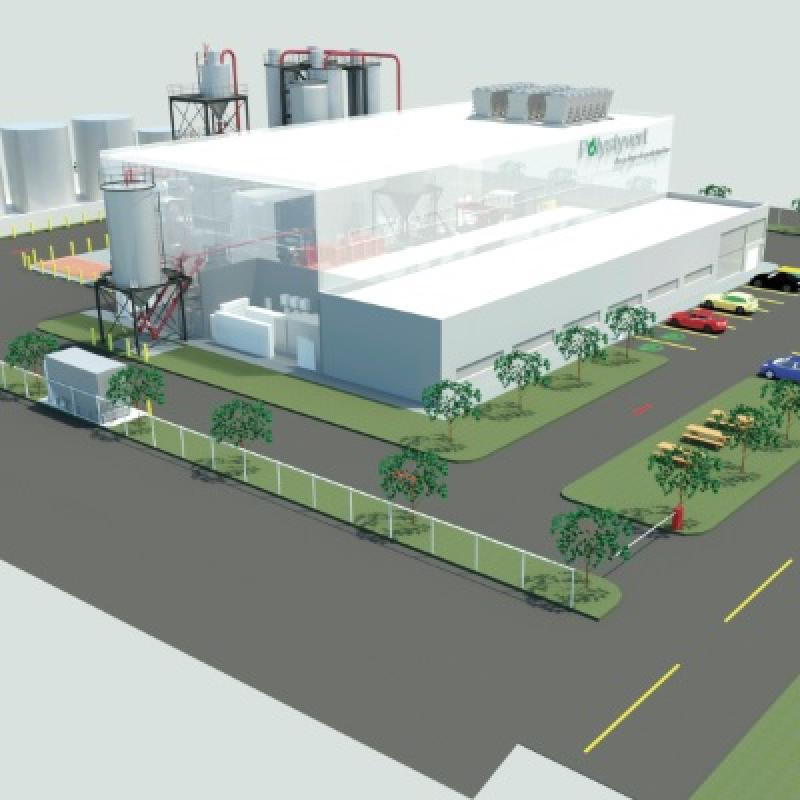
Polystyvert Inc. is constructing a recycling facility in Greater Montreal as part of its efforts to foster a circular economy for polystyrene, a particularly difficult-to-recycle plastic.
Founded by its chief growth officer Solenne Brouard in 2011, the Montreal startup has developed an alternative to mechanically recycling polystyrene. The polymer, used to make Styrofoam, is easily contaminated from other plastics, food, metals, paper and various chemicals, presenting challenges to recycling.
Polystyvert’s energy efficient method purifies polystyrene and outputs it as a food-grade resin that can be reused as virgin material.
After years of testing, the company has partnered with two major industry figures and received $40 million in funding for a recycling facility, which is “the realization of my dreams,” Brouard told SustainableBiz.
With plans to recycle 15 per cent of the polystyrene waste that is disposed of in Quebec per year, the facility is promising not only quantity, but energy efficiency in a compact package that can be replicated across the world.
A “breakthrough” plant
To recycle polystyrene, Polystyvert devised a purification process that can handle high-grade recycled materials.
The feedstock is mixed with an essential oil called cymene that only dissolves polystyrene, after which large contaminants like paper and metals are filtered through a mesh. Next, a low-temperature flocculation process further filters contaminants such as ink or flame retardants from the cymene mix until they are reduced to a size of one micron.
The liquid mix is then turned into a paste through a process called precipitation, where a fire-retardant chemical is added. The cymene is captured for reuse.
The paste is pushed through an extruder to be shaped into pellets. The resin has “the same mass, the same mechanical properties so you can reuse it for the same thing” and is like virgin plastic, Brouard said, because of the low-temperature process.
The recycled resin is economically competitive with the cost of creating virgin polystyrene and can be used for products like insulation panels, packaging and petri dishes.
Feedstock will be provided by two industrial partners that Brouard would not name, but were said to be large and well-known figures in the polystyrene field.
The industrial partners helped fund the facility, which also leveraged support from the Quebec and federal governments. Altogether, funding came to $40 million. The “breakthrough” facility, as Brouard described it, is expected to recycle 9,000 tonnes of polystyrene per year on a building footprint of a relatively compact 25,000 square feet.
She expects to hire 25 people to work at the facility, along with some engineers. The hires will give Polystyvert just over 50 employees.
It is expected to be operating by the end of 2024.
“That’s a pretty small building because most of the equipment can be outside, so that’s pretty efficient. I think the efficiency is really something really linked to the process because it’s low temperature. So the cost of operation remains affordable, as well as the cost of equipment. Since we are low temperature, we don’t need equipment that could resist to a high pressure and temperature.”
These features make Polystyvert’s process scalable and affordable, she concluded.
Rather than focus on selling the recycled plastic, Brouard emphasized how Polystyvert is selling the technology. The plan is to use the facility as a showcase and license out the company’s technology around the world.
Energy efficient process
In addition to the benefits of recycling polystyrene, Polystyvert’s process is energy efficient and reduces greenhouse gas emissions.
An independent European firm named Neue Materialien Bayreuth conducted a life-cycle analysis and found the company’s recycling can reduce greenhouse gas emissions by 90 per cent compared to incineration and conventional production of virgin polystyrene, according to Brouard.
In addition to reducing plastic pollution, the recycling process is water-free, eliminating the need to use the precious resource.
The technology is useful for areas with polluting electricity grids or expensive electricity such as Europe, Brouard said.
Interest in licensing Polystyvert’s technology has come from around the world. Brouard said organizations from Europe, North America and Asia have expressed interest.
Pilot plant plans
Polystyvert is also advancing a pilot plant to recycle a polymer called acrylonitrile butadiene styrene (ABS). It is frequently used in casings for cellphones, toys, automotive parts and cosmetic packaging, Brouard said.
The pilot plant is located in the company’s research and development centre in Montreal and expected to be constructed for $3 million.
“There is large potential in ABS. There is very high demand for recycled ABS and mechanical technologies are even less able to handle ABS than polystyrene, because there is much more contamination in ABS . . . We are currently speaking with very large players in order to deploy this technology around the world.”
Polystyvert is raising funds and Brouard said she is feeling good about the company’s traction, because investors are seeing the trends for the value of recycled plastic.