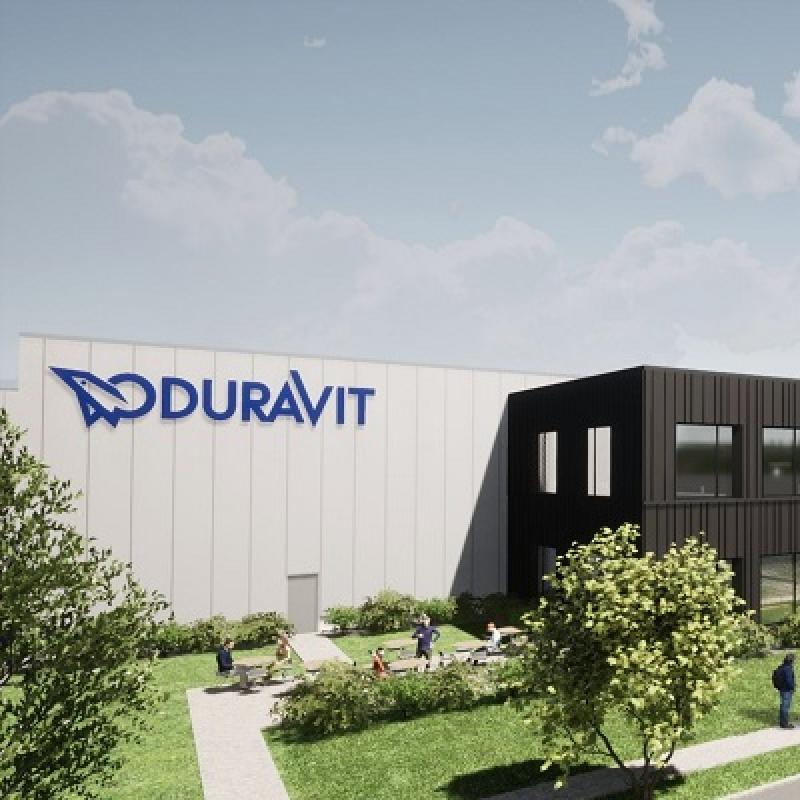
German ceramics company Duravit AG will build what it bills as the world’s first ‘climate-neutral’ ceramics facility in Matane, Que., with plans to run it entirely on hydropower to eliminate greenhouse gas emissions.
Duravit, headquartered in Hornberg, produces washroom furniture and porcelain products such as toilets, bathtubs and wash basins. Its North America office is in Duluth, Georgia, with operations in China, India, Tunisia, Egypt, Germany and France. The Matane facility is its production entry point into the North American market.
Ceramics is a polluting industry, with one paper estimating ceramics manufacturing in Europe creates 19 megatonnes of carbon dioxide each year, and brickmaking to be responsible for 2.7 per cent of global greenhouse gas emissions annually.
Duravit’s Andreas Wegeleben, head of corporate communications, told SustainableBiz in an interview the Matane facility is “a key player and a key component of our sustainability strategy,” as it seeks to reduce its Scope 1, 2 and 3 emissions by 20 per cent by 2030 and be a carbon-neutral company by 2045.
“There is no planet B,” Christian Gilles, the CEO of Duravit Canada, also said in an interview. “We have to take care and work with (the) planet we are having,” with every company having a responsibility to reduce their greenhouse gas emissions.
Why Duravit chose Quebec
Duravit opted for Quebec because the province could provide clean, affordable electricity at costs cheaper than natural gas in Germany, Gilles said. Clean electricity is better than alternative fuels like hydrogen right now because it is more affordable and cuts out a processing stage, he added.
Besides the cost of clean electricity, he also said Quebec offered free land, and Matane has a port which makes it easier to transport a 110-metre-long kiln from Italy by shipping vessel.
The Canadian government contributed $19 million with a repayable contribution, while the Quebec government offered an $11 million loan.
The government funding played an important part in reducing risk of the project, Gilles said. The kiln is a “completely new development” which cannot be tested in Germany and re-installed in Matane. The funding will cover the cost of trials which have to be held in Canada, because Duravit cannot produce ceramics on the first day and must hire and train workers.
Matane factory's green credentials
Expected to begin operating in early 2025 and reaching full manufacturing capacity in 2028, the Matane facility will feature what Duravit claims is the world’s first electric roller kiln, which will be powered by hydroelectricity.
Duravit expects to create 240 jobs at the factory.
Gilles said the company conducted research and talked with some of the biggest suppliers in the industry to prove its climate-neutral claim for the incoming Matane facility, and discovered it was a first. No other ceramics company contested their claim.
The roller kiln, created by Italian manufacturer SACMI, will operate using heating elements powered by electricity rather than natural gas burners.
By being powered by renewable, clean electricity, Duravit states it will be climate-neutral, meaning it will produce no Scope 1 and 2 emissions. This will eliminate around 11,000 tons of carbon dioxide per year compared to gas-powered ceramics factories, according to the company.
Duravit will also make efforts to reduce supply chain emissions. Raw materials will be sourced in Canada or from the U.S. “as near as possible” to reduce transport distances, rather than import from Europe or North Africa. When possible, the company will use electric vehicles and electric-powered forklifts in logistics. The ceramics will also be largely used for the North American market.
A role model for the industry
If a country offers clean electricity at a good price, Duravit can also use renewables to power its operations, Gilles said. It installed solar panels on its Chinese and Egyptian factories to run certain activities, though not kilns.
Wegeleben said he is optimistic the Matane plant will be a role model for the industry to show how factories can run on green energy. “With this new plant, we are doing a big step for us but also for the ceramics industry."